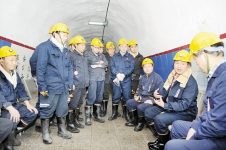
Miner’s lamp management application scheme based on RFID technology
[ad_1]
Strengthening the management of the use of miner’s lamps in coal mines, including the management of mining equipment storage sites, maintenance locations, distribution, etc., to ensure that the miners’ lamps are in good condition and can effectively meet the use of normal and special conditions underground is an important condition to ensure safe production in coal mines. The purpose of studying various management methods of miner’s lamp is to obtain a safe production environment and seek the best economic benefits of mining, and to ensure the needs of safe production and normal production.
The intelligent management software of the miner’s lamp can realize the automatic management of the personnel and the miner’s lamp: each employee of the mine is equipped with a unique barcode data identification ID. The software is used in conjunction with the barcode technology to record the situation of the miners entering and exiting the miner’s lamp room.
The barcode combines the employee number and various other codes, allowing or restricting access to a predetermined area. The detailed information contained in the barcode can be collected by the smart light system. At present, the barcode is closely combined with the unique number on the RFID tag. RFID The label is fixed to the miner’s lamp or other equipment. This process is part of the primary design of the database and is associated with the allocation of the miner’s lamp in the system. Once completed, the rest is just a maintenance issue-adding new allocations when new employees arrive , When an employee resigns, the previous assignment will be removed.
1 System planning and program selection
Applying RFID systems to mines proved to be a serious challenge. Initially, 125 kHz low-frequency and 13.56 MHz high-frequency passive tags were used to tailor tags for the (mining) cap lamp battery box. Install a reader (transponder) in the equipment distribution room and near the turnstile at the exit from the miner’s lamp room to the shaft. The turnstile is also equipped with a barcode scanner to read the ID card of each miner to confirm whether Allowed to pass.
However, the RFID system failed to meet the requirement of a minimum reading distance of 600mm, because there are 3 areas where miners must pass through turnstiles. If the reading range of the system is less than 60O mm, reading errors may occur. Active tags are also studied. If an active tag is used, the RFID system can have a greater reading distance when tracking items. However, since the cost of active tags is too high compared with passive tags, this solution is not desirable.
Another option is 900 MHz UHF passive tags and readers. Since water and metal can cause interference with RFID and cannot achieve a high read rate, all tools used by miners are artificially made of different materials. Because the lamp is made of plastic. It has no effect on the reading of 900 MHz UHF tags, and tags with cap lights are easier to handle. The fully equipped self-rescue bag is surrounded by a stainless steel container. The gas detection equipment that interferes with the reading of 900 MHz UHF tags is also wrapped in stainless steel, which interferes with the working frequency of the tags and readers.
2 System implementation and equipment selection
Dual-frequency RFID technology combines the advantages of low-frequency (125-135 kHz) transmission and high-frequency (6.8 MHz) RFID high-speed data transmission capabilities. RFID readers transmit low-frequency signals to provide energy to the tags. The tag uses a high-frequency spectrum to transmit signals to the reader. This dual-frequency performance can achieve the successful reading of multiple tags, even when many miners gather and the number of people going down the mine continues to decrease. The system can read 7,200 tags per minute on a continuous basis, with a reading range of 0.6 to 2 m. The system can run through liquids and even some metals. The performance is better than 13.56MHz and 860~960 MHz RFID systems.
A test was conducted with 18 dual-frequency readers and 5,000 tags in a miner’s lamp room. In addition, the installation work includes setting up a local area network (LAN) to connect the reader and determine the configuration of the reader in the miner’s lamp room, so as to optimize the operation of the system. the result shows. The dual-frequency system can “reach a high degree of accuracy” and can meet the need to track the movement of miners in and out of the miner’s lamp room. In essence, the miner moves along a predetermined route equipped with a reader, so that the data of the miner and the cap lamp can be collected, because the cap lamp has passed these predetermined points.
The system combines the RFID reader network with the mining enterprise resource planning (ERP) system. The system obtains time and field data from the human resource module of the mining ERP system. Time and field data are integrated with the item release information of the miner’s lamp room. The item release information of the miner’s lamp room is collected from the RFID reader. These integrated data. In the past, it was usually used to make bills related to the use of miner’s lamp rooms and equipment, as well as management information. Using smart light system, can give a list of all units. In order to make bills.
3 System characteristics
The main advantage of the intelligent light system using RFID and system integration is that it can track the situation of the miners passing through the turnstile. It can mark the path of the workers from the ground to the underground. Since the first system was tested and installed, the reading success rate of the system was 100%. The system can track the movement of equipment and miners on a continuous basis. The implementation of RFID tracking (system) can be used for the second stage of mine safety inspection. , The information generated by the system allows any miner to quickly confirm when he has not returned to the miner’s lamp room after his shift to determine his location.
The RFID system tracks and records the number of shifts in daily operations, and obtains information such as the number of employees working underground in each shift and the maintenance status of safety devices. For all equipment and procedures that have been manually managed, a complete maintenance history is very necessary. of. The repaired or maintained equipment is recorded in the repair platform through the RFID system. A miner’s lamp is equipped with a unique identification code, and then all repaired and replaced parts can be collected through its unique miner’s lamp number, thus constructing a complete service log. The smart light system keeps a complete list of spare items, components and their respective prices, so that it is possible to track the cost and usage of spare items and components. The generation of some necessary reports electronically reduces the demand for labor in this area and also reduces human errors.
The RFID system integrates smart light application software, and also takes into account the safety verification of turnstile passing points. Only when the mining tool has an allocated miner’s lamp, a fully equipped self-rescue bag and portable gas detection equipment, is it allowed to enter and exit the shaft through the turnstile. The information collected through the RFID system can prevent counterfeit use of identification cards and prevent other personnel from entering and exiting the mine, because only qualified miners have barcode ID tags. The barcode number of the miner and the RFID tag code of the equipment must be entered with it. The codes assigned by the smart database in the past match the RFID data obtained from the reader (transponder) into various reports according to the needs of each mining site to locate the movement of personnel. Loss of equipment, and tracking of equipment taken for repair or exchange.
4 Conclusion
Before this system was put into operation, the monthly loss rate of miner’s lamps at a specific location was as high as 25%. Because there is no mechanism to identify the device, and it cannot be associated with a specific individual. It is impossible to specify who was lost or damaged. Now it is very different. The adoption of the “lamp for life” concept will share the responsibility to the individual, so that the miner’s lamp holder will be the owner of the miner’s lamp. The connection between the ID code of the miner and the ID code of the miner’s lamp label will enable the assigned equipment owner to be responsible for the loss or damage of the equipment. As in the initial stage of any important technology, the training of employees is a successful RFID configuration. Key factor. Once the correct technology is determined, personnel are trained to accept the system. Will become an important challenge. Although some miners are skeptical of the new system and see it as an assessment mechanism for them, the benefits of the RFID system are very clear to all mine owners. It improves the safety mechanism of mine operators. It optimizes the cost-effectiveness of equipment maintenance and management. More importantly, it controls equipment loss and makes it possible to manage equipment usage more accurately.
[ad_2]