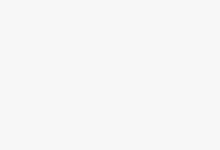
BP RFID personnel tracking system application
[ad_1]
Region: Washington State, USA
Operating frequency: 6.0 GHz-6.5 GHz
User: BP Cherry Point Refinery
Label type: active
Implementing company: Multispectral Solutions, USA
British Petroleum (BP) applied an employee tracking system based on RFID ultra-broadband technology-“Location Aware Safety System” (LASS) at its Cherry Point refinery in Washington State. The system can keep track of the whereabouts of 2,000 refinery employees, contractors and visitors.
The Cherry Point Refinery was established in 1971 to process crude oil on the North Slope of Alaska. It is the largest refinery in Washington State with a crude oil processing capacity of 230,000 barrels per day. It can produce 3.5 million gallons of gasoline, 2.5 million gallons of jet fuel and 220 diesel per day. Million gallons. In the refinery processing areas, oil depots and docks, all staff, contractors and visitors must wear RFID badges. Once a fire or explosion occurs in the above areas, the refinery manager can confirm the employees and others in the first time. The location of the person.
Tim ONeill, a senior safety engineer at Cherry Point refinery, said that the positioning safety system strictly complies with the process safety management (PSM) hazardous chemicals standards announced by the U.S. Occupational Safety and Health Administration (OSHA) in 1992. “We need to be very clear about employee information in emergencies.”
Cherry Point uses an RFID badge produced by Multispectral Solutions in the United States, with a built-in active ultra-wideband RFID tag (ultra-wideband technology, or Ultra-wideband, abbreviated as UWB, and its frequency is between 6.0 GHz and 6.5 GHz). According to the information transmitted by the tag, the positioning security system uses IBM WebSphere software for data collection, enabling rapid identification, positioning and tracking of employees, visitors and other personnel. According to Rob Mulloy, senior vice president of Multispectral Solutions, each RFID badge contains a unique ID, and the radio frequency signal is transmitted every second. The badge has a thickness of 0.25 inches, a net weight of 1.8 ounces, and is powered by a micro battery; its battery life is approximately two years. The price of RFID badges is US$40 per piece; in addition to badges, Multispectral Solutions also provides 10 sets of fixed readers and handheld readers to Cherry Point Refinery, of which the price of fixed readers is US$150,000 /set.
Before using the RFID security system, the Cherry Point refinery used barcode ID cards to track personnel entering the factory. However, it is very troublesome to use barcodes to track whether employees are safe. It requires scanners to scan ID cards individually in a closed environment, which is time-consuming and laborious. Later, Cherry Point replaced the barcode ID card with a passive RFID badge, and employees wearing passive RFID badges can enter the factory area through a turnstile. This passive RFID system covers an area of 600,000 square feet and connects eight areas. There is a monitoring device in each area, and managers can find out how many employees remain in the work area when an emergency occurs, so as to guide the employees to evacuate to the designated safety zone in time in the next step. The passive RFID security system greatly improves the efficiency of discrimination, but there is a problem that during the evacuation process, if many employees are evacuated on foot or when many vehicles pass through the exit quickly, the accuracy of this passive close reading is not Very high.
With the active RFID security system, the RFID reader can accurately identify the information data of employees wearing badges at each evacuation exit. If someone is stranded in the workplace, the monitoring equipment can also display the person’s location map. When the manager’s pointer slides over the person’s image, the employee’s badge information will be seen.
The Cherry Point Refinery carried out performance tests of the active RFID system at the beginning of this year, and plans to continue to increase the application range of the system to 1.5 million square feet in the third quarter of this year. Rob Mulloy said: “The RFID reader can identify the badge wearer within one foot and give accurate positioning; if the badge wearer stands between two readers, the reading range can reach 1000 to 1500 feet. Of course, there are some technical challenges, for example, we need to consider how to read accurately in a metal environment. In a special environment, Multispectral Solutions’ RFID system has passed the test and can work very well; RFID tags emit short waves Ultra-wideband signals, even around metal, can be read accurately.”
[ad_2]