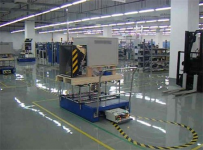
Application of AGV trolley based on RFID
[ad_1]
AGV is an automatic navigation mobile device, which can often be seen in automated storage systems or various automated production environments. Quickly and accurately determine the location of the goods, so that the AGV can respond quickly and move efficiently.

AGV can be divided into electromagnetic guidance, laser guidance and visual guidance. Practical application shows that electromagnetic guidance has the advantages of high cost performance and smooth ground. However, there are still limitations such as cumbersome track layout and difficulty in changing the path. If the number of stations is large, the track design is more complicated.

Schematic diagram of typical electromagnetic guidance methods
Double track
A portable reader is installed under each AGV trolley, a label is installed on each node on the ground, and the track is selected through the system (as shown in the figure below).

Schematic diagram of RFID dual-track guide
The use of an absolute positioning automatic logistics system makes the positioning of AGV trolleys, cargo markings, and positioning more convenient, and improves the transparency of the system.
Equipment List:

UHF 800mm, RFID reading equipment, 24V power supply can be connected.
system requirement:
The RFID tag will be installed on the path of the AGV trolley. The RFID reading and writing device is installed on the AGV trolley and provides a suitable horizontal reading range. When the RFID tag needs to be replaced, the data content in the replaced RFID tag must match the data content of the original tag. Because AGV cars often use non-contact inductive loops for power supply, the corresponding RFID system must have higher EMC characteristics.
Convenience:
1. High degree of automation and precise system status.
2. Accurate logistics management.
[ad_2]