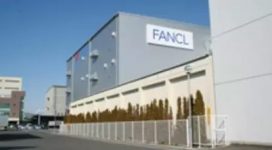
RFID technology has created the most advanced distribution center for FANCL
[ad_1]
Project Background
FANCL Corporation (headquartered in Yokohama, Kanagawa Prefecture) established a mail order company for additive-free cosmetics. Today, FANCL also sells health products, food and beverages in retail stores and convenience stores across Japan. In August 2008, FANCL opened a new “Kanto Logistics Center”, which concentrated operations in eight locations. In addition to installing an automated material handling system in the new factory, FANCL also added 14,000 RFID tags to improve the accuracy of order fulfillment. The delivery rate of the distribution center reached more than 90% on the same day, and the transportation accuracy was close to “zero error.”
Project requirements
The FANCL distribution center used to be near the production bases in Chiba and Yokohama. However, the company found it increasingly difficult to expand its business and respond to different product demands.
In order to solve these challenges, FANCL established the Kanto Distribution Center. The 13,200 square meter (142,084 square foot) facility incorporates more than 2,500 items, including 600 cosmetics and 300 supplements. It can handle up to 30,000 mail orders and manage 2,200 goods to domestic retail stores and international locations.
solution
With the help of Daifuku, the Kanto Distribution Center implemented a warehouse management system (WMS) and a small automatic storage and retrieval system (AS/RS) to process mail orders and deliveries to domestic and international retail stores. The facility also has various automated picking systems, which are provided by AS/RS.
The order was consolidated into one of 14,000 containers guided by RFID tags. 154 tag readers are installed on the conveyor belt of the equipment, which can realize fast and accurate transportation.
With the new material handling system in place, the company has achieved higher throughput and transportation accuracy. By extending the order deadline from 4 pm to 6 pm, the same-day delivery rate rose from 78% to 91%. In addition, the transportation error rate dropped from 0.04% to less than 0.005%.
Project analysis
1) Small load AS/RS storage supplementary products; flexible handling of diversified plastic containers and cardboard boxes.
2) The received product is stored on the pallet.
3) There are 66 radio stations in the mail order inspection area.
4) The operator can put the ordered items on the temporary table in advance to improve throughput.
5) The automatic replenishment system is equipped with two cranes on the aisle on the side of the picking rack.
6) The picking line of each destination store. There are 4 skin care products classified by product category.
7) Surf sorter for each delivery company (5 slides).
8) Each order is associated with a container by placing a label on it. The post office has 15 radio stations.
Project benefits
The implementation of this project helped FANCL to reduce material handling costs while reducing its environmental impact. Quickly deliver products to customers and meet their needs. The integrated website realizes the unified management of products and one-stop order issuance. By reforming the company’s business methods, FANCL has reduced logistics costs and increased annual sales by 10%.
Previously, the number of on-site staff required was 280. But through the implementation of the project, now only 200 people are needed (a reduction of 30%). In addition, the transfer time between the warehouse and the number of trucks to be transported was significantly reduced, reducing 1.3 million tons of CO2. The new paperless order system will save 7.4 million different forms of cost each year.
Project renderings
[ad_2]