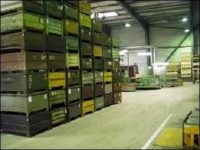
RFID Logistics Freight Container Tracking at Outland Steel Plant
[ad_1]
In 2007, the management of Outland Steel Plant launched a real-time positioning system project, in which active and passive radio frequency identification technology was used to track the position and movement of forklifts and containers. Through this project, the material flow, warehousing and information flow of the Altland Steel Plant have been upgraded to make these processes more transparent and efficient, so as to better handle high production.
For example, the Altland Steel Plant uses a radio frequency identification (RFID) system to track forklifts and containers in the plant. After the system is fully activated, the system will send out ultra-wideband (UWB) active radio frequency identification tags to track 20-30 forklifts, and it can also transmit passive ultra-high frequency (UHF) radio frequency identification tags to track 10,000 metal turnover boxes and their Loaded products. Through this RFID real-time positioning system, all transportation processes are recorded with the help of the system, and the number of workpieces is updated in time, so as to grasp the automatic operation data in real time. As a result, the management of the Outland Steel Plant can obtain real-time detailed information to control the process and processing.
According to the current plan of the project, the forklift is equipped with two Ubisense tags, one on the roof and the other on the outside of the driver’s cab. Two more Ubisense tags are installed on the fork. The tag collects signals from 6 to 8.5 GHz at a frequency of 20 times per second. Ubisense sales manager Holger Hartweg (Holger Hartweg) said that due to the large bandwidth of 1.2 GHz, the signal suffers less interference, which makes the forklift positioning error within +/- 15 cm. A total of 11 readers were installed in an area of 2500 square meters to clean the cast parts. A total of three locations will implement a forklift tracking system, this is just one of them. The real-time positioning system captures the signal from the forklift tag and its ID code, and then analyzes the location of the forklift in the warehouse. Since the tags are installed on different parts of the forklift, the system can also determine the direction of the forklift.
In addition, the Altland Steel Plant installed a passive UHF RFID system for tracking containers. The system is expected to be fully operational in the summer of 2009. The Altland Steel Plant places the turnover boxes on pallets and transports them to different locations. A passive RFID tag will be installed at the bottom of each turnover box. After the turnover box is filled with casting parts, it will be transported to the warehouse and temporarily stacked on the floor or storage rack. When the driver picks up a tote, the reader of the forklift will recognize the UHF radio frequency identification tag of the box, and the system will identify which tote and when it is moved. Subsequently, this information is summarized with the location information of the forklift, so that the manager can understand which turnover box was removed.
Currently, Ubisense installs scales on forklifts to weigh the turnover boxes. The system subtracts the weight of the empty container (such information is stored in the database) to obtain a negative weight. Since the turnover box may be loaded with different casting products, these data will help determine the content of the products in the turnover box.
[ad_2]