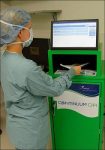
The operating room at the University of Tennessee Medical Center uses RFID technology to monitor the safety of medical items
[ad_1]
University of Tennessee (UT) Medical Center plans to expandRFIDThe scope of the system is used to track equipment trays and consumables in 36 operating rooms. This solution, called Continuum OR, was designed by medical product company DeRoyal. Currently, the 5 operating rooms of the hospital have used this technology to track items. UT Medical Center is also considering the use of fixed, handheld readers to take inventory of medical supplies on the shelves and record the surgical supplies used by each patient.
This fall, 36 operating rooms in the hospital will begin to use this RFID system.
At the same time, DeRoyal is also promoting the Continuum OR solution on the market, which uses its own software, readers and tags. The system is designed to provide doctors with the correct consumables and tools and record them during the operation. At the end of this year, UT Medical Center is expected to use this system to record items that patients need to pay for during surgery.
UT Medical Center has 36 operating rooms, including five orthopedic operating rooms. The hospital can provide 14,000 operations each year, of which orthopedic operations account for 4,000.
Like most, UT Medical Center used a doctor’s preference card system in each operating room in the past. The doctor told the hospital staff that he needed the tools needed for each type of surgery. On the day of the operation, the staff will find the medical instruments printed on the preference card and send them to the operating room. About 50% of the items are not in use. On the contrary, if a certain device that needs to be used is not found in the operating room during the operation, the staff needs to stop the operation to find the device. In addition, the staff also need to manually check whether these devices have expired.
Becky Ashin, vice president of Advanced Orthopedics Center at UT Medical Center, said: “We hope to redesign this system.”
In 2013, UT Medical Center began to cooperate with DeRoyal to develop RFID solutions to solve these problems. DeRoyal has provided operating room management software for 35 years. In 2002, the company sold its operating room software business to GE. The company’s CEO Brian DeBusk said that since then, DeRual has turned to developing laboratory efficiency solutions. Currently, UT Medical Center is using operating room management software provided by GE.
DeBusk recalled that after conducting some research, the hospital found that this solution was surprisingly simple. Beth Kaylor, DeRoyal’s Director of Clinical Innovation, suggested installing RFID readers and antennas on trash cans to read waste packaging.
UT Medical Center decided to pilot this system in five orthopedic operating rooms. DeRoal and UT Medical Center also tested the system in the laboratory before installing the system on the trash can in each operating room. The hospital has Android Impinj Speedway Revolution readers outside each trash can with a built-in Laird antenna. At the same time, a monitor is installed above the trash can to display the read data, which will also be transmitted to the DeRoyal cloud software.
Seneca, the hospital’s surgical medical supplies supplier, is responsible for attaching labels to sutures and gauze. The company uses passive EPC UHF RFID tags from multiple suppliers. Ashin said the hospital would mark Seneca’s unmarked items.
The data of each item is stored in GE software. When the RFID tag is read for the first time, these data will be transferred to Continuum’s OR software and a corresponding relationship between the tag ID and the item itself will be created.
The staff will still use the doctor’s preference card to select the items needed for the operation and place these items on the tray to the operating room. Before the operation, the staff needs to data the patient ID number in the DeRoyal software. DeRoyal calls on this part of the GE software related to surgery data. Then, when the waste packaging is thrown into the trash, the UHF reader will read the unique ID number and record it in the surgical supplies list. In the future, this list will be used for surgical cost statistics.
Currently, the pilot has lasted for 6 months. Ashin said that although most hospitals only use RFID to track high-value items, UT Medical Center believes that any item is worth tracking. This is because the system can identify problems before they occur. For example, if medical items are past or cannot be used on a particular patient, DeRoyal software will display a warning on the display to remind staff not to use it.
Usually, when employees discard the marked bags, the medical items themselves do not touch the patient. Ashin said: “In the future, we plan to scan all items before they are opened.”
DeBusk said that DeRoyal abandoned the use of HF RFID tags due to the reading distance. When using UHF tags, workers only need to throw the packaging into the trash can, and the tags can be read, which will not disturb normal work.
Ashin said that in the past six months, the Continuum system allowed employees to know the items needed for each operation by displaying the items actually used in each operation. This also reduces the number of times items are taken out and put back.
A nurse said: “It lets us know what is really needed during the operation.” As the solution is promoted and used in other operating rooms, the hospital will also study the installation of Impinj xArray readers on the ceiling to obtain real-time data. These data will also be used for inventory management.
(Exclusive manuscript of rfid world network, please indicate the source author for reprinting!)
[ad_2]