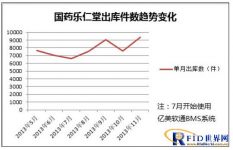
Case Analysis of Emeisoft BMS Sinopharm Lerentang Informationization of Warehouse Inspection and Sorting
[ad_1]
In the early stages of their own development, enterprises in traditional industries generally focus their energy on market development, brand building, product quality control, sales channel development, etc., while often neglecting the basic planning and construction of their own informatization. When an enterprise develops to a certain scale, labor costs continue to increase, personnel efficiency continues to decline, and error rates soar. This results in a layout of information planning. This may be the problem that most traditional enterprises are facing and considering.
Why use the BMS system
Sinopharm Lerentang Pharmaceutical Co., Ltd. is a large-scale pharmaceutical commercial enterprise focusing on drug logistics and distribution. It started from Shijiazhuang, Hebei Province, and gradually expanded its business to the whole province. Its business scope involves 100% of the top three and second class hospitals in Hebei Province; 80 % Of county-level medical institutions. Sales exceeded 10 billion in 2013, and the number of orders showed explosive growth.
In March 2012, the distribution of essential drugs entered the Sinopharm Lerentang logistics center. From April to May 2013, the monthly average number of shipments from the logistics center reached 165,000, an increase of 51.6% compared to 2012. At the same time, the sorting and distribution of basic medicines presents the characteristics of more customers and fewer goods, which greatly increases the difficulty of reviewing products. The traditional mode is used (using the outbound list to check the information by seeing the goods and finding the ticket, and fill in the various types manually. Documents), which brings tremendous pressure to the review sorting group. According to statistics, 27 people in the sorting group during the peak period, 289 items were checked out per capita, which is still unsatisfactory.
In the re-inspection process of warehousing and logistics, labor issues have become increasingly prominent. Prior to the manual review of paper documents, the daily work efficiency of a single person was basically constant, and meeting the order demand would increase a lot of personnel costs, and at the same time face the risk of an increase in the error rate.
What is the effect?
After a number of comparisons between companies, Sinopharm Lerentang finally chose Emeisoft to cooperate withPDAEquipment to carry out warehouse inspection, inspection, packing, short inspection, printing review list, printing packing label, loading and transportation, etc., instead of the traditional paper delivery order check method, regardless of the cost of personnel Still work efficiency has been significantly improved.
Through the Emeisoft BMS solution, using PDA equipment to enter the optimized sorting review process, the per capita number of review and picking out of the warehouse during the peak period has increased to more than 500 pieces, the efficiency has increased by 70%, the error rate has dropped to less than one in a thousand, and internal customers are satisfied. The degree is increased to more than 92%, which greatly reduces the intensity of personnel work and shortens the time of personnel work.
Use Emeisoft Handheld Terminal to review goods
What did imax do?
First of all, the BMS system of Emeisoft is connected with the sales and warehousing system of Sinopharm Lerentang, receiving the data wave sent by the automated distribution machine, and synchronizing it to the professional PDA terminal and the back-end system, and making the electronic label. The inspector provides the data basis.
Secondly, the re-inspector scans the barcode of the warehouse goods through the PDA device, and corresponds to the shipping order to check whether there is any missing or wrong picking phenomenon (caused by the phenomenon of out of stock and out of stock during sorting), thus replacing traditional paper documents. Check the signing process.
Third, after inspection, the process of closing the box will be completed according to the batches of the drugs sent to the address, and the barcode printing will be performed again, and the verification document will be printed to provide a proof of getting off the truck and receiving the goods.
Fourth, by loading and transporting to different city hospitals, unloading the goods and using PDA to scan the bar code after closing the box again to complete the mobile inspection work at the destination. Of course, the BMS system of Emeisoft also supports the binding of cargo vehicles. The GPS function in the PDA can be used to view the delivery process and the location of the vehicle on the background GIS map. Sinopharm Lerentang will implement this function in the future to ensure the delivery of medicines. Safety.
they said
The person in charge of Sinopharm Lerentang informatization stated that the review and sorting is the “last mile” in the warehouse. Together with transportation and distribution, it forms Sinopharm Lerentang’s external service window, which improves the on-time delivery rate and the order error rate. The reduction will greatly improve the customer satisfaction of Sinopharm Lerentang, and will have an immeasurable potential impact on further consolidating market control and improving the integration of the pharmaceutical distribution market.
The BMS solution of Emeisoft iSoftStone has not only greatly improved the efficiency of the review and sorting group of Sinopharm Lerentang, but also reduced the labor intensity of on-site personnel and saved labor costs. The manual bill filling is transformed into an information flow, which fills in the blank of information construction from the logistics out of the warehouse to the customer’s “last mile”.
[ad_2]