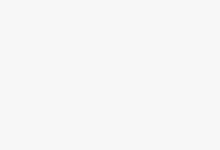
Application case of electronic tag picking system in a warehouse logistics center of a pharmaceutical company
[ad_1]

Before the warehouse transformation, the traditional paper order work was used, and the shipping orders were printed according to the customer’s needs. The pickers picked the required goods one by one according to the orders, and then proceeded with the inspection and shipping processes after the picking was completed. With the large increase in shipments, traditional paper order picking will cause picking errors, low picking speed and efficiency, and long training time for new employees, which will seriously affect the company’s efficiency.
The company is now renovating the warehouse. In terms of hardware: on the second floor, the acceptance inspection, cold storage and drug shade storage, drug storage area, and the third floor medicine, non-medicine, and health care products section are equipped with active guide rails and our company’s visual electronic tags are installed; Software aspect: Integrate its warehouse back-end management system and the company’s electronic label picking system, and the two cooperate to realize the full electronic management of storage, inventory, picking, and outgoing. During the picking process, the warehouse management staff can check the progress of each order and the quantity of the remaining goods in each location at any time, so that picking is fast and accurate, replenishing goods in a timely manner, and guiding the pickers to the greatest extent correct, fast and easy Complete the picking work properly.
Picking process:
All use Qualcomm GT-E3T24C, CAN bus 2.4-inch TFT color screen (visualization) electronic picking labels, one-to-many mode, the screen can display the number of picks and any information you need (graphics, numbers, barcodes, two-dimensional Code, etc.). The entire inventory area is divided into several channels, each channel is associated with a scanner, and each order is associated with one or more turnover boxes. When there is an order, the picker takes the turnover box to the picking area, and the picker scans the box number with a scanner. The electronic label light corresponding to the goods in this channel in the order lights up, and the workers follow the goods position and The quantity is picked. After the picking in this channel is completed, the picker will pick the next channel, and the other pickers will repeat the above process until all the picking is completed (of course, several channels can be performed at the same time). Then, the turnover box is sent to the shipping area for review, and finally packaged and shipped. The entire picking process is orderly, achieving high speed, high efficiency and low error rate.
Working principle diagram

[ad_2]