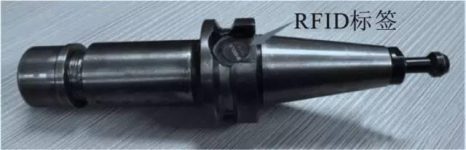
RFID machine tool information management realizes intelligent control
[ad_1]
With the rapid development of modern numerical control technology, the varieties of equipment and processed parts are diversified. Due to the actual application needs of production and processing, a large number of tools are frequently used in the tool library and flow exchange between machine tools. CNC machine tools have become the core equipment of the machining workshop. The number and types of tools are constantly increasing and it is difficult to manage. A large number of tools in the production workshop frequently flow and exchange between the tool warehouse and the machine tools and machine tools. As a result, the existing tool management solutions can no longer meet the diversified needs, and RFID radio frequency technology will be applied to various CNC tool information collection.
RFID has the characteristics of fast scanning, small size, strong anti-pollution ability and durability, reusable, penetrating and non-barrier reading, large data memory capacity and strong security. Therefore, it has the advantages of production data collection, monitoring, and data transmission. Huge application potential. This article is based on radio frequency technology, installs the RFID chip on the tool handle, realizes the collection and management of tool information, and reduces the comprehensive production cost.
Existing tool management cannot analyze the records and data of the entire life cycle of the tool, but only realizes the collection and monitoring of tool information at the time point, and cannot obtain the unprocessed data; traditional tool management lacks M2M (Machine to Machine) information interaction , It is impossible to realize integrated management; the existing tool management plan is aimed at meeting the production requirements, and the cost issue in the entire life cycle of the tool is not considered.
Intelligent management is carried out for the use of tools in the machine tool, the tool parameters are transferred to the machine tool, and the tool is added to the machine tool magazine for the processing program to call. When the tool processing is completed, the production time of the tool is written into the RFID of the tool to realize the functions of real-time tool information collection and tool status tracking. Tool information management system parameter collection and setting. The tool information management system refers to the use of radio frequency technology, CNC and RFID readers to adopt serial communication technology based on the communication between the machine equipment (such as CNC machine tools, tool setting instruments, etc.) and RFID readers in the manufacturing unit. Realize the information monitoring and storage management of the tool in its life cycle.
The prerequisite for the tool management of the machine tool is that the tool has been grouped, and the tool has been set by the tool setter. In order to realize the corresponding functions of the tool, the machine tool needs to initialize the tool magazine and write the tool processing time into the tool holder RFID. Because the reading and writing distance of high-frequency RFID is relatively short, when reading and writing the RFID of the tool holder, the antenna must be close to the RFID tag through a pneumatic device.
1. Initialization of the machine tool magazine
To realize the intelligent transmission of CNC tool information, we must first rely on CNC machine tools. In order to ensure that the tool is automatically loaded into the tool magazine when the tool is loaded into the machine tool, and the tool parameters are read from the RFID tag into the machine tool magazine, the machine tool magazine needs to be initialized. When the machine tool changes, the machine tool needs to control the rotation of the cutter head One week (see Figure 2), reinitialize all tools to the machine tool magazine; for each tool, the following operations are required: CNC drives the cylinder to lift the RFID reading head through instructions, after the cylinder is in place, the CNC obtains the sensor switch status and starts RFID reading The writer works; the cylinder status is maintained for 500ms, and the CNC drives the RFID reader to read the RFID chip of the tool holder through serial communication; retracts the cylinder and the CNC detects that the cylinder magnetic induction switch is in place, and the tool continues to run; the function that needs to be controlled: in the CNC A button is added to the operation interface, and the cutter head automatically rotates one circle each time the button is pressed to ensure that it can rotate one circle each time the tool is changed, and initialize the machine tool magazine; it is not allowed to directly install the tool into the tool magazine holder of the machine tool.
2. Tool production time record
When unloading (group) the tool, the tool production (processing time) will be written into the tool management system. The process of writing the machining time of the machine tool into the RFID of the tool holder is as follows:
1. Before unloading the tool or after grouping the tools, the machine tool records the used tools, rotates the cutter head, and writes the tool processing time one by one;
2. The cylinder status is maintained for 500ms, and the CNC drives the RFID reader through serial communication and writes the RFID chip of the tool holder;
3. After retracting the cylinder, CNC detects that the cylinder magnetic induction switch is in place, and the cutter head continues to rotate.
To ensure the smooth operation of the above program, a button needs to be added to the CNC operation interface. Before unloading the tool or after grouping the tools, press the button once to make the machine tool rotate one circle and write the tool usage time to finally complete the tool life control. Pay attention to the operating specifications when operating the program flow.
3. Tool data storage in RFID chip
Tool code is the important information to determine the uniqueness of the tool’s identity. It is written into RFID, and each tool is managed through the tool code. When writing the corresponding program, the nominal diameter, nominal length and corresponding program of the tool can be determined according to the specification and model of the tool, and then the corresponding diameter compensation and length compensation can be given according to the actual situation. Since the same tool can be installed on different machine tools, and the same machine tool can process different products, abnormalities may also occur when processing products, so the above processing information needs to be displayed during processing. It can be controlled by the program to display the tool code, processed products, product quantity, abnormal information, etc., and the tool code, tool life, tool used time and other information in the RFID record.
The entire life cycle of a tool generally includes multiple links such as planning, purchasing, marking, warehousing, lending, assembling, using, returning, regrinding, and scrapping. The tool holder is equipped with an RFID electronic tag to read, write, and collect and identify life information throughout the life cycle of the tool. Install RFID reader devices on the host of equipment such as CNC machine tools to allow the RFID electronic tag to interact with the main control system. Establish the RFID tag as the information carrier to realize the information interaction between the tool and the host and the host and the host, so as to achieve the prediction of the tool life.
[ad_2]