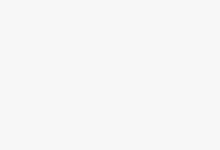
Itong-MBMS industrial manufacturing quality traceability system was successfully applied to BLT Medical Technology Co., Ltd.
[ad_1]
The itong-MBMS industrial manufacturing quality traceability system has been applied online for one year in BLT Technology Co., Ltd., and the barcode scanning is generated during the whole process of raw material inspection, material receiving and dispatching, production assembly, quality inspection, product maintenance, product storage, sales and after-sales service. Product history archives, and integrated application with ERP system, not only achieve product quality traceability goals, but also greatly improve the company’s refined management of manufacturing links. In the past, it was time-consuming and laborious to query product archives and product production process data, which has become more than easy. , In order to greatly satisfy domestic and foreignFDAThe strict certification requirements for medical devices replace the previous temporary work of various departments of the entire company, saving everyone time and labor costs.
1. According to FDA certification requirements, adjust existing system functions and establish a standardized BLT medical equipment manufacturing traceability information system
The second phase of the project focuses on the needs of this part. Based on the content of the survey and the existing system functions, we have made the following additions and adjustments:
1) Traceability management of key parts and semi-finished components
1.1 Redefine the key material and product barcode rules, the system assigns codes according to batch number + serial number, and the general barcode material system is managed according to batch number;
1.2 The barcode labels of incoming key parts or semi-finished products can be read through the barcode system. Without barcode labels, they are all printed and archived through the barcode system;
1.3 Scan package barcode labels for incoming materials, scan body labels or package batch number labels for semi-finished products, and automatically record the batch number and serial number of the material;
1.4 The barcode of general materials is automatically written into the electronic product file of the “device history record” according to the batch number as the quality traceability number system;
1.5 The key parts and semi-finished products are automatically written into the product electronic file of the “device history” according to the SN number as the quality traceability number system.
2) Traceability management of product files
Device history file record
Order number: Product model version number number:
Serial number: Production order number, program download table number, feeding BOM number
Production Date:
Serial Number Key Accessory Name Model Material Code Quality Traceability Number Inspection Report Number Record Number Remarks
…
Reserve manual input column
2.1 The second phase of the barcode system adds an integrated application with three core documents of Kingdee sales order, delivery notice, and production order, and automatically writes the sales order number, product model, serial number, production order number and other information into the “device history” ”Product Electronic File
2.2 When there is incoming material inspection, the system generates an “Incoming Material Inspection Form”, displaying the inspection order number,
2.3 The inspection content is divided into two application schemes on the system, which can be filled in and not required to be filled in. When filling in, the incoming inspection data is input through the system. When not filling in, only the inspection order number is tracked to the product file;
2.4 When the system electronic incoming material inspection form is not used, only the barcode label of the inspection form number is printed out and pasted on the manual paper incoming material inspection form as a basis for future inquiries.
2.5 The incoming material inspection order number is used as the inspection report number system to automatically write into the “device history” product electronic file;
2.6 The application method of semi-finished product inspection is as the above-mentioned incoming inspection.
2.7 The “record number” is defined on the barcode system for material and semi-finished product inspection forms. When the inspection form is generated in the system, it will be automatically written into the product electronic file of the “device history record” as the number recording system.
Three) Quality inspection barcode system management
Due to the complexity of the original quality records and many forms to fill in, the quality inspection of this program considers two informatization application methods. Paste it on the manual form; the other is to imitate the existing document format and enter in a systematic way, which is more convenient for retrospective management. The first method is determined in this period, and the second method is applied through the platform development in the later period.
3.1 Monitor test record: This form is more complicated, and proceed according to the first simple method mentioned above. If according to the second method, consider recording only abnormal data, other data sets the standard range, and the system automatically fills in the standard value range data.
3.2 Daily inspection records of process control: The content of this order is acceptable. According to the first simple method mentioned above, if you follow the second method, you need to create a form and manually enter some data in the system.
3.3 The first inspection record table of the monitor: The content of this order is acceptable, according to the first simple method mentioned above, if according to the second method, you need to create a form and manually enter some data in the system.
3.4 Label Printing Inspection Record Form: This form is relatively simple, and it is carried out according to the first simple method mentioned above. If according to the second method, you need to create a form and manually enter some data in the system.
3.5 Packing Inspection Record Form: The content of this order is acceptable, and proceed according to the first simple method mentioned above. If you follow the second method, you need to create a form and manually enter some data in the system, and the key parts supporting system will automatically display;
3.6 Aging inspection form: The content of this order is acceptable, proceed according to the first simple method mentioned above, if according to the second method, you need to create a form, you need to create a form, and enter some data in the system;
3.7 Mainboard debugging record table: This order is more complicated, just follow the first simple method above, if you follow the second method, consider only recording abnormal data, other data sets the standard range, and the system automatically fills in the standard value range Data within.
3.8 Complete machine program download record table: The content of this order is acceptable, and the product model, production task number, batch number, SN number, and program version number can be automatically obtained, according to the first simple method mentioned above, such as the second method , You need to build a form to enter some data in the system.
Through the expansion of the above three functions, the materials, semi-finished components, finished products; records, documents, reports, and product files can be dynamically checked vertically and horizontally, forming a more complete company quality traceability management system, and it is convenient for all aspects of inquiry and FDA certification management.
2. Traceability management of production tasks and production plans
2.1 Combine the quantity of the production task list and the production day plan (including packaging, inspection, etc.). To achieve the purpose of tracking the completion of the production task list and online inventory. (It is possible to distinguish the completion status of each production order and which process the machine is in in time), and generate daily reports.
2.2 If the production order is completed, an alarm upper limit (such as three days) can be set. This product is not in storage, but the system has a prompt. The operator can understand the reason why the machine is not in the warehouse in time.
2.3 During the SN tracking process in the current production task list, due to the company’s certification issues, there is a bar code that distinguishes the certification information. In order to find the machine easily, theoretically the fifth position on our machine serial number is the argument position. Therefore, you can ignore this bit when recognizing the barcode, and you can query this machine by directly inputting it.
3. Key parts are traced with batch number + serial number barcode, and ordinary parts are traced and managed with batch number barcode.
3.1 Purchasing key parts needs to track the batch number and SN number, adjust each link of the system, and add batch number barcode information;
3.2 Ordinary materials that need to be tracked by barcode are only managed by batch number barcode;
3.3 The tracking SN number of production semi-finished products and finished products remains unchanged from the existing system;
4. Scan and judge the production and assembly process of key parts, and compare the consistency according to the assembly BOM
4.1 Barcode system integration of key material data of Kingdee production task feeding BOM;
4.2 Define the product process collection route and procedure according to the production task list
4.3 The acquisition system downloads production tasks, and assembles and scans according to the production tasks;
4.4 When scanning online production and assembly, feed BOM according to the production task for material assembly
4.5 When the scanned material does not meet the production feed BOM, the collection system prompts early warning control;
4.6 When the materials do not match, re-maintain the feeding BOM or reload the scanning assembly;
4.7 Packaging key parts are included in the feeding BOM for control;
4.8 The early warning control can continue to scan and assembly after the workshop management personnel release it.
4.9 Collect and scan assembly information: production team, production process, production order number, product model, product batch number, assembly material batch number, production responsible person, production time and other information.
5. Product production process and quality traceability according to production tasks
5.1 Barcode system integration Kingdee system has issued an unclosed production order;
5.2 Print the serial number barcode of the production product body according to the variety and quantity of the production task list;
5.3 Scan and collect data in each assembly process according to the production task list;
5.4 Carry out product patrol inspection and complete machine inspection according to the production task list, and collect inspection data;
5.5 Carry out product packaging according to the production task list, and automatically write the sales order number (when producing according to the order);
5.6 Scan the barcode of the packaging product, the system will automatically print out the barcode label of its packaging box, and the barcode of the packaging box will automatically associate with the barcode of the packaging product;
5.7 Scan the barcode of the packaging box, and automatically display its packaged product and serial number information;
5.8 Tracking record of the software version number of the whole machine and the software version number of each key main board;
5.9 Scan the barcode of the packaging box according to the production task list, and the system will automatically compare the model and quantity of the produced product, and automatically generate a Kingdee system product warehousing list after confirmation and submission;
[ad_2]