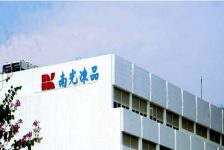
Warehousing management application case of Macau Nanguanggufeng Distribution Co., Ltd.
[ad_1]
Customer background and needs
At present, Macau Nanguang Gufeng Distribution Co., Ltd. has not introduced advanced technology bar code management for the inbound, outbound, and inventory management of more than 1,000 varieties and approximately 33,000 quantities of goods. Or use traditional manual recording of goods outbound and inbound data, and manual inventory of goods. Under this mode of operation, problems such as low efficiency and high error rate of finished products exporting, warehousing and inventory counting are prone to occur, resulting in difficulties in data maintenance and traceability of goods exporting and warehousing.
Therefore, the company currently needs to introduce barcode recognition technology and a computer management system to improve the efficiency of goods out, warehousing and inventory.
Project Objectives
◆ The goods in the system support two management methods: repeated barcodes and unique barcodes.
◆ Use the scanning gun to scan the barcode of finished products when they are in and out of the warehouse, and record the data of the goods out and in the warehouse through the system.
◆ Use bar code recognition technology combined with the management system to improve the efficiency and accuracy of the goods out, warehousing and inventory.
◆ Manage warehouse locations to facilitate the search of goods when entering and exiting the warehouse.
◆ Through the system, it is possible to manage, retrospectively export, warehouse, and inventory goods and information after the goods are split.
◆ Realize the first-in first-out function of goods out of the warehouse.
◆ Through the system, the inventory information of the goods can be managed and traced. The inventory can be performed once a month or once a year according to the needs of the user.
◆ Through the system, according to the time period, the data of goods import, sale and storage can be provided to users in need for viewing and analysis.
◆ It can realize the data connection with the user’s existing ERP system
solution
This solution makes full use of existing IT equipment investment, adopts one-dimensional barcodes as the identity of goods (using low-temperature-resistant labels), and supports two management methods: repeated barcodes and unique barcodes. And combined with PDA to carry out bar code data collection, in order to achieve the management, tracking, and query of finished products in and out of the warehouse and finished products in stock.By setting the first-in first-out attribute of the goods, the first-in-first-out control of the goods is realized when the goods are out of the warehouse.
Program implementation plan
Main stage task time
1 The project started to set up a project team. Define detailed phase goal plans and assign project tasks.
2Customization analysis 2.1 On-site investigation We will conduct customer demand investigation on site according to the content, scope and requirements of the subject matter specified in the contract.
2.2 Demand analysis The two parties jointly conduct a detailed customized demand analysis. Submit the “Requirement Specification” to you.
2.3 Review of “Requirements Specifications” You will review the “Requirements Specifications” and give back to us for revisions. Repeat the above process to form a finalized “Requirements Specification”, and both parties will confirm in writing on it.
3 Design and development 1) Carry out detailed design and code compilation.
2) Perform quality inspection on the system.
4 Software system installation and testing We implement the installation and testing of the application terminal software system at the implementation site.
5 System Comprehensive Performance Test We conduct overall tests on all functions of the software, software operating data correctness, hardware operability, and data connection at the implementation site.
6 Delivery of system files We will deliver to you all relevant documents such as “System Installation Instructions” and “System Operation Instructions”.
7 System training. We conduct system application training for relevant operators in different departments and positions in your office.
8 System delivery
(Trial run) The system test data is cleared, and the system is officially put into use.
9 Project Acceptance 1) We deliver all products to you and submit the “Acceptance Application Report”.
2) You will perform the acceptance inspection and reply to our acceptance conclusion in writing.
3) Pass the acceptance or repeat the acceptance process.
10 The project is completed and enters a one-year free maintenance period
[ad_2]