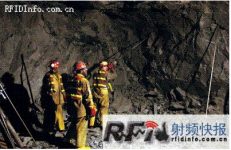
U.S. W.Va. uses RFID system to track miners to prevent sudden casualties
[ad_1]
The RFID tracking management system called “Mine Tracer” was jointly developed by Venture Design Services (VDSI) and Helicomm. In an emergency (emergency) event, the system can locate the location of the miner in the underground passage, and track and locate the underground infrastructure of the miner and coal mine in real time.
Most American coal mines have simple or no suitable tracking or wireless communication systems. The company can only know who is working in the coal mine at a certain moment, but it does not know the location of each person. However, in the next few years, this situation will now be changed. In 2006, 14 miners died in the Sago coal mine accident in West Virginia. Subsequently, Congress passed the Coal Mine Improvement and New Emergency Response Act of 2006, requiring all coal mines to be equipped with wireless tracking systems for miners before 2009. In addition, Virginia has enacted its own legislation requiring coal mines to order wireless communications and tracking systems before July 2007.
Last week, Southwest Virginia Resources began to introduce the “Mine Tracer” system, which is based on a network that can locate miners at any time within 75 feet. This network uses the ZigBee network protocol for communication arrangements.
During the introduction period, the company issued badges embedded with 2.4 GHz RFID active tags. Kenneth Hill, Helicomm’s sales director, said that these labels produced by VDSI meet Helicomm’s internal design standards. The tag’s read-write chip can process up to 100 bytes of data, but in this project, only a unique identification code is compiled. Every 200 feet in the coal mine, the company will install a VDSI reader as a communication node, which will receive data from each identity badge.
These nodes record the badge’s identification code and signal strength, and then wirelessly transmit the data to nearby readers through a ZigBee communication connector. The RFID reader then forwards the information to the next reader, all the way to the computer that manages all readers. These data will be transmitted from the source to the destination via a maximum of 27 relays. Then, the software on the computer can calculate the location of the miner’s badge within 75 feet by comparing the signal strength of several fixed readers.
RFID system can play a role in ensuring the safety of miners
Mike Propst, the head of the coal mining company, said that currently there are only four miners working in coal mines that have applied RFID systems. This gives the company the opportunity to test the system on a small scale, even though the mine itself is quite large. Propst said, “We want to see how this system works. This is the only coal mine in the company where this system is installed.”
An RS-485 serial line connects the underground controller and the available server on the ground through the network. The Helicomm software installed on the server sets the data so that the location of each badge can be identified on the mine map. So the company can detect the whereabouts of every miner in the coal channel.
Propst believes that he can use this system to know where his employees are. Therefore, if he needs to send a message, he knows where to call and where to use warning lights to warn miners of dangerous situations. There is also an emergency button inside the label, and the miner presses it twice to indicate that he is in trouble. “I think it will be very worthwhile,” Propst said, because the cost of the Helicomm-VDSI solution is lower than that of other competitors.
In an emergency, the system can still operate after the coal mine’s power supply is cut off. Hill said the coal mine would shut down the power supply in an emergency because of potentially explosive gas. In this project, the “MineTracer” system has a backup power supply that can continue to work for 48 hours after the accident. “Our entire system,” Hill said, “is designed to work in that environment.”
[ad_2]