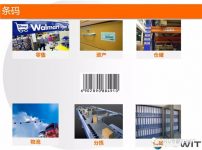
Application of RFID technology in automobile manufacturing
[ad_1]
RFID is a new generation of automatic identification technology. It started relatively late in China. The earliest large-scale application in China is also a relatively closed-loop railway system in our country.
Therefore, the popularity of RFID is not high. As an application engineer, I am often asked by my customers what RFID technology is, so I usually introduce barcode technology to them first.
Barcode technology originated in the 1920s, and its application in all walks of life has been very mature.

Including supermarkets, warehousing, express logistics, supply chain management and some industrial process control that everyone is very familiar with, it provides reliable and simple automatic identification applications through simple binary number attributes. In the traditional manual transcription mode, It has greatly improved the efficiency of enterprise resource management, so it has been quickly popularized, and very mature applications have been created in various fields. Because of this, everyone has a good understanding of its technical characteristics.

For example, it is visible light, the typical recognition distance is about 50cm, can only be read individually, does not have the ability to read through, low storage capacity, poor security, etc. These technical characteristics, in the process of modern enterprise resource allocation management, Obvious constraints have been formed.
Including the early modern logistics management, as well as the just proposed intelligent manufacturing, industry 4.0, etc., it actually formed a situation in which the development of the industry forced technological innovation. The field of automatic identification urgently needs a new technology that can overcome the current situation. There are technical shortcomings, forming a broader, more efficient, and safer application technology to realize simple identification and richer applications.
This is actually the RFID technology we are discussing today, to be precise, UHF RFID technology.

When it comes to auto factories, we are actually focusing on smart manufacturing.
At present, smart manufacturing has become a hot spot in the global industry.
First, because it is the current strategic goal of many countries.
Including domestic Chinese manufacturing 2025, German industry 4.0 and so on.
After rising to the national strategy, it means that there will be more policy support and financial support, which will play a major role in promoting the actual application of technology.
Therefore, in the current manufacturing industry, the application of RFID technology has a better policy soil.
As far as the technology itself is concerned, the current development of readers is becoming mature and stable. The prices of tags and chips are showing a trend of declining, while the types and performances have kept rising. Therefore, this has also promoted more rfid in the manufacturing field. Application in the link:
Including warehouse management, process management, distribution supply chain and so on.
Using rfid technology to promote manufacturing enterprises to achieve “standardization”, intelligent upgrades, lower production costs, flexibly respond to market changes, and better meet customer needs, ushered in a good development opportunity.

Automobiles are relatively sophisticated manufacturing, and the designed crafts and processes are more complicated.
But in general, you canIt is divided into four major processes: stamping, welding, painting and final assembly.
The automobile manufacturing industry has developed to this day and has become very mature. The manufactured cars are becoming more and more high-end and their performance is getting better and better. But in fact, there are still some unavoidable problems in its four manufacturing processes, or we can say yes. There is room for improvement.

For example, in the press shop.
The stamping workshop is mainly to stamp steel plates one by one through a large mold to make the door, frame, roof cover and other skeletons of the car we see.
Therefore, stamping is actually the production of raw materials. The accuracy of its inventory statistics and the real-time tracking of warehousing information are necessary. It is of great significance for enterprises to balance production and supply, formulate scientific production plans and resource scheduling.
The spraying workshop mainly sprays colors on cars. The environment is very disadvantaged and is not suitable for personnel to operate, so there is an urgent requirement for automatic identification;
The final assembly workshop is to complete the assembly of engines, seats, interior and exterior trims, etc., different processes in different links, different parts of different cars, so it is more cumbersome, the automatic identification of the car body will help improve the efficiency of the final assembly and reduce the error rate. Realize the scientific allocation of resources.

Therefore, different workshops have different requirements. When the RFID system is implemented, it is necessary to formulate different solutions according to these different requirements.
For example, in the stamping and welding workshops, we focus on controlling the production quantity, inventory quantity, and outbound quantity of stamping raw materials. Realizing accurate statistics on the data flow of these links can provide data for the intelligent scheduling and scientific decision-making of the entire production management system. support.

Our basic realization idea is to install electronic tags on the racks for transferring stamping raw materials.
Deploy RFID reading nodes at the end of the production line, warehouse entry and exit ports.
When the stamping parts are produced and loaded on the rack, the information will be automatically written into the rack label to complete the information binding.
After that, it will be transported to the warehouse by a forklift, and a reading device will be installed in the warehouse. By reading the electronic tag, locate the raw material information on the rack to complete the storage information record.
For the same raw materials, we deploy reading equipment at the exit.

We can take another look at the pictures of the on-site implementation. It is basically the same as our design.
Such a system can solve the inventory transparency of raw materials from stamping to welding. The real-time automatic statistical data flow improves the formulation of production plans and achieves a good balance between supply and demand. affim.

The paint shop is mainly to install electronic tags on the sliding skid of the transport car body,
When the car body is placed on the skid, the car body information will be entered.
Deploy RFID reading nodes on the machine rolling machine in key positions of the workshop,
After the skid transports the car body to a key position, the reading device will read the electronic tag information on the skid to locate the identity information of the car body and transmit the information to the PLC to guide the completion of related operations.

In the assembly shop, a car body that has been welded and spray-painted requires many processes.
Including frame assembly, chassis suspension, power synthesis, etc.,
Therefore, by installing an electronic tag in a certain fixed position of the car body, similar to the front of the car,
This label will follow the entire assembly process of the entire car body,
And install RFID reading equipment at different nodes to guide the process.

Take an example to illustrate the application mode of RFID in intelligent manufacturing.
This is a job assembly line that can be seen in many manufacturing companies.
The raw materials flow in from the front end, through a variety of different process combinations, in a sequential operation mode, to complete the production of a product.
Traditionally, paper work orders, manual records, or barcode scanning are used. On the one hand, it is inefficient. On the other hand, too many human involvements will inevitably make mistakes and cause the production progress to stagnate.
Therefore, with the help of RFID technology, the electronic tags on raw materials, parts, semi-finished products and finished products enable production planning managers to quickly locate them and understand the consumption of raw materials, which will greatly improve the efficiency and quality of production.
At the same time, RFID technology can also collect and process product information, helping production personnel easily grasp the operation of the entire production line and further accelerate the production progress of the product.
Due to the readable and writable nature of RFID, it can provide a constantly updated real-time data stream. Complementing the manufacturing execution system, the information provided by RFID can be used to ensure the correct use of labor, machines, tools, and components.
So as to realize paperless production and reduce downtime, and promote the smooth progress of production logistics.
This can be seen as the use of RFID electronic tags as the information carrier to replace paper work orders. By deploying RFID collection equipment at each station of the production line, the planned information flow management based on intelligent production scheduling as the baseline ensures resource optimization and effective cost control. Completely solve the problems of printing production scheduling and work order scheduling; comprehensively solve the tedious management problems of printing production process.
Write all the production process information into the electronic label for storage, and complete the display guidance of the process through the display device of the station terminal.

These two pictures show a device installation drawing on the actual site, representing the application of two different final assembly links, and their basic commonality:
Through a simple automatic identification technology such as RFID, accurate and rapid identification of object information can be realized, and the back-end MES system can make scientific decision-making, thereby improving the production efficiency of the enterprise, improving the organization, shortening the production cycle, and improving the comprehensive competitiveness of the enterprise.
[ad_2]