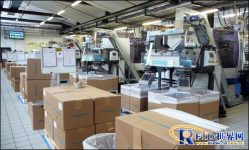
Coster Group adopts RFID technology to improve logistics efficiency
[ad_1]
Italian packaging manufacturers have introduced UHF RFID solutions into their production lines to track and locate information such as the location and status of products during production, storage, and transportation.
After the Italian packaging manufacturer Coster Group adopted the RFID solution, work efficiency was greatly improved, and its logistics operation time was reduced by 1.5 hours per day. Aton is responsible for providing software services such as passive EPC Gen 2 UHF RFID tags, handheld fixed dual-use RFID readers and middleware. According to Coster Group, after the implementation of the system, the efficiency of only managing product locations has increased by 90%. Coster tested the RFID solution from 2010 to 2011, and adopted the system in all of its 17 production lines in 2012. Coster Group is expanding the RFID solution to other production and distribution plants.
Coster Group has seven factories and three distribution agencies around the world, mainly producing packaging for consumer packaged goods, pharmaceuticals and other sprays, and automatic vending products. In order to improve the efficiency of production and logistics, Coster Group has adopted an ERP system since 1998. On the basis of the ERP system, the company began to cooperate with Aton and Atlantic software companies to develop RFID solutions for the traceability of the whole process (from the manufacturer to the distribution center to the consumer). Through the RFID tracking system, the company can know the location and production history of a specific product (production time, location, etc.).
At the end of the production line, workers stick EPC Gen 2 passive UHF tags on the surface of the carton.
Before the RFID system was adopted, product information was recorded manually, which was time-consuming, labor-intensive, and error-prone.
Atlantic is responsible for the research and development of management software that connects with the database system. Aton is responsible for the implementation of the RFID system, which includes the installation of hardware and onID middleware for collecting RFID data.
Coster initially tested the RFID system on its first production line in Calceranica (place name), only for tracking spray products. This production line is independent of other production lines and has a limited output, including about 20 to 25 large packages, each including 200,000 nozzles.
At the end of each production line, Coster workers paste EPC Gen 2 passive UHF tags on the surface of the carton. These labels are encoded by Datamax-O’Neil’s RFID printer. Through onID middleware, RFID tag information is stored in the back-end database.
The unique code of the label, product information and other data are stored in the system. After the carton enters the pallet, the worker holds the RFID reader to read all the information of the labelled carton. Workers can select the goods to be moved and the place to be placed according to the prompt information on the computer display on the forklift. Before the product is loaded and transported, the RFID read-write channel is used to check whether the order is consistent with the delivered product. If it does not, the system will issue an alarm.
So far, the company has installed 17 label printers on its first production line. The onID middleware and Datamax-O’Neil 4212 label printer jointly perform RFID label writing and verification.
After the implementation of the system, the efficiency of inventory search has also been greatly improved. Based on the good results of the first production line, the company plans to expand the RFID tracking system to other branches and three distribution centers. In the distribution center, a handheld reader is used to read the code of the tag, and the time of product reception and shipment can be displayed.
[ad_2]