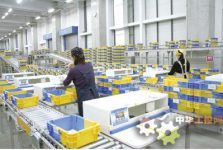
Fully introduce RFID to achieve correct and efficient logistics and distribution
[ad_1]
In 1980, FANCL started as a mail order company for non-additive cosmetics. It also deals in supplements (such as nutritious food) and sprouted rice/green juice. Since then, starting from mail order, large-scale direct-sale stores have been opened in Japan, and then expanded to traditional distribution channels such as convenience stores, and the business has continued to grow.
In August 2008, FANCL opened its newest logistics base in Chiba Prefecture, Japan-FANCL Co., Ltd. Kanto Logistics Center, integrating eight logistics sub-centers that have been operating separately according to product categories and sales channels. Here, there are advanced material handling equipment, and the most eye-catching is that as many as 14,000 RFID electronic tags (the RFID system uses 13.56 MHz) to build a high-performance, high-precision logistics system. Through the opening of the logistics center, FANCL increased the shipment rate on the day of order acceptance to over 90%, and improved the shipment accuracy to the level of “basically zero errors”. Put the freshness and quality of the products first, and provide customers with a satisfactory supply chain.
Integrated management of 2500 varieties
At the beginning, FANCL had set up logistics centers in Chiba and Yokohama, where there were production plants. The business is managed by the headquarters, but due to the development of the business and the diversification of the products it manages, the logistics center is gradually unable to meet the needs of production. To this end, FANCL used external warehouses in Yokohama, Saitama, and Nagano to establish eight logistics bases for different businesses and product categories. However, due to the scattered locations, the delivery locations of the same order items are different, causing problems such as “multiple collection and delivery”, “increased logistics costs”, and “complex freshness product management”. To this end, Hitachi Logistics Kitakashi Branch has developed a Kanto Logistics Center with a total area of 13?200?m2 specifically for FANCL. Focusing on 600 kinds of cosmetics and 300 kinds of health foods, it has integrated management of more than 2500 kinds of commodities. In addition to the daily mail order business of up to 30,000 items, it also undertakes the delivery to 200 direct-operated stores and nearly 2,000 other types of distribution stores in Japan, as well as the shipment to overseas markets.
Utilize RFID tags to realize the most advanced logistics management
With the support of the newly developed WMS system, the Kanto Logistics Center has set up a mail-order product inspection area and a picking area; store, distribution, and overseas product inspections based on the “Fine Stocker” automatic warehouse for storing products provided by Daifuku. Districts and picking districts. A variety of picking systems based on the “high-performance digital picking system (DPS)” for automatic replenishment of stackers, and a logistics system composed of more than 100 inspection stations have been constructed. The biggest feature is that 14,000 RFID electronic tags are applied to a large number of picking turnover boxes, which is convenient to control the conveying process of each process (Figure 1).
In the mail-order inspection and picking area for small items, RFID tags (117 readers) have been applied from the picking of the turnover box, and the information contained therein corresponds to the information in each product order. There are a total of 15 workstations, where orders for different commodities are manually placed in different turnover boxes; at the same time, the use of handheld terminals also serves the purpose of making sure that the order information is correct. In this way, the complete paperlessness of sorting orders is realized, which greatly reduces the order risk caused by manual labor.
After that, the turnover box passes through 4 C-DPS and 1 conveyor belt synchronous DPS, and is transported to different picking areas. During the conveying process, a total of 164 readers and writers are installed on the conveyor belt, which can also be accurately and quickly dispatched.
In order to improve the processing capacity, in the picking area, the goods of the next order are manually placed on the temporary placement table in advance; another function is to install the automatic stacking box type goods side by side on the back of the shelves in this area. Replenishment system (Figure 3). The replenishment stacker picks up the goods from the box-type automatic warehouse, whether it is a plastic box or a corrugated box, and it also supports various sizes of packaging boxes. Using this automatic replenishment system can save a lot of manpower. After that, the products are sent to the inspection and packaging station through the conveyor belt, where each product has to be read once the JAN code to ensure that the packaged products are accurate. After the packaging is completed, it is transported to the first floor of the logistics center by a conveyor belt, and the goods are sorted and transported according to different transport companies through a sliding block-type automatic sorting system (Figure 4).
For the inspection and picking areas for large-size products for shops, distribution and overseas, the working methods are roughly the same; here, four sorting lines are set up according to the classification of health food, basic cosmetics and other commodities (Figure 5). At the starting point, use the reader to write visual information to the RFID plastic card that can be erased multiple times, and insert it into the turnover box. The rewritable card adopts RICON “RECO-View”, which can read and write at most 1000 times. All commodities are sorted digitally, and before entering the packaging process, different commodities will enter different packaging stations according to the classification of stores, circulation or overseas commodities under the “judgment” of the RFID reader. Here, the turnover box can also be stacked in two sections, so the RFID antenna can also be set up as two up and down (Figure 6).
Reduce logistics costs and strive for environmental protection
In the construction of the new center, FANCL invested 600 million yen. In terms of equipment usage costs, pay to Hitachi Logistics in 7 years, which can control one-time expenses.
At present, the center manages a total of 2500 varieties of products, and the shipment volume is about 300,000 pieces per day. Among them, nearly 1,000 batches are managed for fresh-keeping products, about 7000-8000 SKU. Among the about 2,000 direct-selling products, there are about 300-400 hot-selling products. The total order quantity is an average of 12,000-15,000 pieces per day, and the maximum can reach 30,000 pieces per day, all of which are processed by a digital sorting system.
Through the use of advanced IT systems, FANCL has greatly improved the processing capacity and delivery accuracy of large-volume goods. The delivery rate of orders on the same day has risen from 78% to more than 90%, and the mis-shipment rate has also been reduced from the original 0.04%. To less than 0.005%. After the intensive and integration of 8 logistics sub-centers, the number of transfers/inventory transfers between warehouses has been reduced, unified management and unified distribution of goods have been realized, and the increase in logistics costs due to the increase in turnover is currently at an annual rate of 10% Make cuts. What’s more, the jobs that used to require 280 people are now enough for about 200 people.
In addition, the opening of the new center has also reduced the amount of truck transportation used for movement and distribution between warehouses, thereby reducing approximately 1.3 million tons of CO2 per year. In terms of bills required for logistics business, after using RFID, paperless management can also save about 7.4 million sheets of paper each year, which is equivalent to 30 tons.
Mr. Nagasaka Junji, Manager of the Logistics Promotion Group of the Kanto Logistics Center of FANCL Co., Ltd. concluded: “The automatic reading rate of RFID tags is quite good. An error occurs. RFID is easier to deal with small data such as the turnover box ID, and the reading speed is much higher than that of the bar code. In the conveyor belt assembly line of this center, it can achieve 90m/min non-stop tag reading, and the system runs stably and normally. Compared with barcodes, after the introduction of RFID, although the overall investment will be doubled, the investment can be recovered after one and a half years. At the same time, due to its maintenance-free characteristics, the savings are very considerable.”
[ad_2]