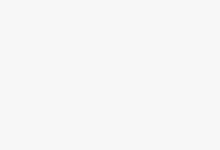
Ford’s RFID supply chain management is surprisingly effective
[ad_1]
With the relevant mandatory instructions from retail giants such as Wal-Mart, the U.S. Food and Drug Administration (FDA) and the U.S. Department of Defense (DOD) and other military representatives, RFID technology has developed from an inconspicuous new wireless technology to the present level—— It ignited like a raging fire all over the earth.
Although there are currently no mandatory requirements for the application of RFID technology in the automotive industry on a global scale, there have been many successful cases of using RFID technology in the automotive industry. Bil has used the Wi-Fi technology-based RFID real-time tracking and positioning system to conduct real-time and accurate management of more than 1,000 car trading activities in the store. According to rough statistics, the number of companies using RFID technology in the automotive manufacturing supply chain shows Regardless of the growth trend, aside from many foreign cases, in China, there have been precedents for the introduction of RFID technology by Sinotruk Group and Taiwan Yulon Motor; we believe that a single spark can start a prairie fire. I believe that in the near future, the global automotive industry will be like the logistics and retail industry, RFID can be seen everywhere!
In 2005, when the overall development of RFID was extraordinary, the North American TNT logistics company launched the first RFID reading device, mainly to provide real-time visibility operation management for the automotive industry, improve inventory (list) management efficiency, and prevent complex supply chains. For interruptions and other issues, the initial test was conducted in Ford’s truck assembly shop.
TNT Logistics in North America mainly provides design, implementation and operation of complex supply chain solutions for large state-owned private enterprises and some medium-sized enterprises. The original goal is to provide RFID technology for Ford’s supply chain, strengthen supply chain innovation management and increase additional auto industry value.
As part of this experiment, the active tag technology and wireless network sensor technology provided by WhereNet are fully utilized. These devices are installed in Ford’s workshop to achieve real-time positioning and provide real-time information. TNT’s Material Sorting Center (MSC) is also installed Related equipment. With an area of 375,000 square feet, this center can realize a series of work such as receiving, packaging and transporting Ford products. The product materials are delivered to the production line in a set order. The RFID reading device is installed at the door of the MSC to read the RFID tag information and ID code on the material. By automatically acquiring data, the system can determine whether the material has arrived and is fully utilized. In addition, the Ford RFID system can also be combined with an advanced transportation system (ASN) function to obtain location information of materials in transit.
There are also other uses, such as the system can automatically monitor the cargo loading and unloading process, implement tracking monitoring and real-time setting control, and promote communication between MSC and assembly workshops. In order to prevent operation interruption and reduce manual operation, Ford adopted real-time control software provided by Tibco. When all of Ford’s supply chain links are involved, the RFID system can provide real-time monitoring, which involves the cooperation of material suppliers, sorting centers, production workshops, and product distribution links.
The sorting center can provide parts, arrange the order of materials, and provide analytical instruments for the Ford assembly line. Parts can be delivered by workers through plastic kanbans. Generally, the delivered parts will not exceed 35 pounds. The sorting operation is mainly to deliver the required materials in order, usually between 1,000 and 2,000 pounds, and need to be transported by forklift. Although the instrument is smaller than the parts, it needs a forklift to transport more than 500 pounds at a time. Before the use of RFID technology, most of them were manually operated, and the process was often interrupted due to various reasons, such as transportation delays, missing parts, misplacement, and loss are common.
WhereNet’s RFID active tags emit signals every four minutes, and can be received by RFID readers installed in the TNT sorting center and Ford’s assembly shop. These tag data information can be collected, classified, evaluated, analyzed and summarized. Ford also installed chart analysis software and installed a portable computer on the forklift to analyze the data. In order to use RFID technology, TNT uses a series of software, such as warehouse management system, warehouse tracking system and WhereNet’s visibility service software, etc., all of which are integrated through Tibco’s middleware.
TNT uses WhereNet’s active RFID solution. As Ford continues to increase RFID tag requirements and use sensors, WhereNet’s software and infrastructure are also continuously improved. With the addition of different parts of the supply chain, the network becomes more and more. It’s important.
RFID technology has great potential for manufacturing and retail. TNT and early users have truly felt the benefits of this technology. It can optimize operations and improve efficiency. By using Tibco’s second-generation active RFID software, TNT can accurately complete tasks in accordance with orders, and can deliver goods to customers on time and provide real-time information.
This cooperation integrates the strengths of Ford, TNT, WhereNet and Tibco. Now the RFID active project has been implemented very successfully. The real-time control management works well on various platforms, and the synchronization and coordination are also very good. Ford believes that if global supply chain integration can be achieved, then RFID technology will achieve greater success.
[ad_2]