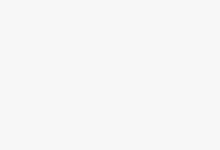
German auto parts suppliers use RFID technology to speed up the delivery process
[ad_1]
At present, the application of RFID technology in the automobile industry is becoming more and more common, and the purpose of application is also diverse, such as parts identification, vehicle management, vehicle cleaning, vehicle anti-theft, and so on. In the following links, readers can click to view a few more representative cases. The automotive application case selected by RF Express this time focuses on the delivery process of parts and components. It is similar to the perspective of Swiss Post’s application of RFID technology to manage container logistics, but the field is different. We take ZF Friedrichshafen, a German supplier of automotive transmission and chassis components, as an example to do a detailed case analysis:
ZF Friedrichshafen, a German supplier of automotive transmission and chassis components, implemented a container management system based on RFID technology as part of the facility upgrade. The application of RFID technology has greatly improved the transportation process of auto parts by reducing the processing time of containers. The company is currently conducting a test to determine what other processes RFID technology can improve.
Customer needs
ZF has 119 factories in 25 countries around the world and employs approximately 57,000 people. In 2007, its annual revenue was US$19.5 billion. In its factory near Friedrichshafen on Lake Constance, the company is responsible for supplying gearboxes and drivetrains for commercial vehicles produced by MAN and Iveco.
Now the demands of truck manufacturers are becoming more and more diversified. They require not only “instant” delivery but also “instant” assembly. ZF also wants to improve the manufacturing process so that the correct goods can be sent out in time with the appropriate assembly sequence. ZF personnel saw an article in a trade magazine about the deployment of an RFID system by Tricon, an Austrian RFID system integrator, and contacted the company in time.
Lessons from Tricon
Ttricon deployed an RFID system in 2006. In the first phase of the project, Tricon observed and tested the RFID hardware. The biggest challenge Tricon faced at the time was to find the correct transponder to identify these containers in a metal and mechanical environment. They need to provide labels that can provide long reading distances, especially suitable for metal surfaces. In addition, such labels must be easy to stick and low-cost. In the end, Tricon chose the labeling system provided by Intermec.
This system uses 15000-20000 869 MHz passive UHF tags that comply with the ISO 18000-6B standard to track the movement of about 1,000 containers every day. According to Ttricon project manager Jürgen Kusper, there have been no problems since the operation at the end of 2006, and the company is now considering using the system in other factories.
ZF trip
After the containers are transported back to their original locations by trucks and buses, they are usually stacked in temporary storage areas. In a few days, workers will transfer these containers to the high-bay warehouse through a fully automated conveyor system. During the transmission process, the RFID reader provided by FEIG Electronic will identify the container. Based on the read tag position information, the system can determine whether the container is in the correct position and whether it needs to be rotated 180 degrees.
This is an RFID reading point of the system in the entire application process. When the container is automatically filled and ready to be sent, the system can calculate the corresponding position of each reading point of the container in the future. After the new container is added to the portfolio, the employee will use the provided handheld interrogator to read it. Each container is assigned a number. This number and the carrier’s description information will be incorporated into the label, and ZF can use this to obtain the data information of the specific container delivered to the specific customer. Workers can select the information describing the container from the option menu after visual recognition. Generally, ZF will use 9 types of containers.
Workers who need to assemble engines and auto parts can enter electronic orders into the company’s warehouse management system. Next, the automated system will place components of various sizes (RF bulletin: component sizes ranging from 80 cm x 120 cm to 80 cm x 160 cm) in labeled containers, and then place the containers in designated locations in the production area. The entire automated process eliminates the labor of workers and speeds up the production and delivery process of parts. After the container is returned to the factory for identification, the system will automatically update, so that ZF can grasp the container entries received by a specific user within a specific time.
Effectiveness
Before implementing the RFID system, ZF Friedrichshafen had to select a few days to manually count the containers to roughly determine the inventory. After adopting this system, the company’s inventory counting has become more accurate. Kusper said that RFID has also helped reduce the cost of containers, although the company is currently unable to provide further information on the cost of purchasing containers each year.
ZF is currently considering improving this system so that customers can read the tags immediately after returning the container to ZF’s warehouse, instead of having to store the container for several days before reading it with an RFID reader. The improved system will enable the container to be identified when it passes through the automated portal, and the earlier the tag is read, the better it will be for the company to control the container’s overview.
[ad_2]