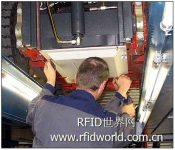
German beverage company Gerolsteiner’s unique warehouse RFID application system has achieved return on investment
[ad_1]
Gerolsteiner Brunnen, a German bottled non-alcoholic beverage and mineral water producer, adopted an RFID system two years ago to comply with EU regulations on food and beverage tracking (EU 178/2002). According to the company, they have now recovered half of their return on investment, and the RFID system basically does not require routine maintenance.
In Gerolstein, Germany, as many as 20,000 pallets enter and exit the Gerolsteiner distribution center every day. In April 2005, the company began to adopt the RFID system. Unlike the common way of pasting RFID tags on pallets, the company embedded passive 136 kHz tags in the floor of the distribution center.
Because Gerolsteiner carried out extensive hardware and frequency testing, the company and integrator SAP SI took a year to complete the project. The company needs to find a frequency band that can make the forklifts loaded with beverages run well when they pass by without affecting the labeling work when the beverages are spilled on the floor.
Gerolsteiner finally decided to use 136 kHz tags in glass bottles-commonly used for animal tracking. The tag (length 3 cm, width 3.5 mm) is implanted in the floor and covered with a layer of plaster. The label is supplied by TI and uses a proprietary air interface protocol.
Each pallet is affixed with an EAN 128 bar code. When the pallet is lifted, the bar code scanner installed on the forklift scans and recognizes the bar code. When the forklift drives the tag on the floor, the reader installed at the bottom of the forklift reads the tag. By linking the barcode number with the ID number of the RFID tag, the computer system updates the pallet position in real time. “Now, we know the inventory situation in the distribution center very well, and can quickly locate the required pallets.” said Roland Keul, director of logistics at Gerolsteiner.
Install an RFID reader on the bottom of the forklift to read the RFID tags on the floor
Gerolsteiner embedded a total of 2,500 tags on the floor of the distribution center. Approximately 5 labels are used for each row of shelves. There are 33 tags embedded in the area before each truck loading area (a marked area with an area equivalent to a large truck), and the tags are spaced 1 meter apart along the loading area. In this way, the forklift operator does not have to manipulate the forklift to a certain point to read at least one of the tags.
When arriving at the loading area, the truck drove into its assigned parking area. The tag is embedded in the floor near the parking area, covering the side of the truck. Forklift drivers load goods from that side, and each time they put a pallet on the truck, they pass at least one label. The identification codes of tags in the same area are the same.
The forklift operator receives the loading order through the computer on the vehicle, for example, loading 2 pallets of apple juice and 1 pallet of mineral water onto a certain truck. The computer identifies the ID code of the assigned truck and the assigned parking area of the truck, and combines this information with the serial number of the order number.
The forklift operator receives the loading order through the computer on the vehicle
The forklift operator drove to the warehouse to fetch the required pallets. Along the route, the forklift reader reads the floor tag and informs the system of the location of the forklift. If the driver enters the wrong cargo platoon, a warning message will be displayed on the screen.
The forklift operator picks up the required pallets in the warehouse and sends them to the loading area
The driver then removes the pallets from the warehouse shelves and transports them to the loading area. The bar code scanner of the forklift recognizes the pallet, and the reader of the forklift reads the floor RFID tag of the exit. The data is connected via the local area network and sent to Gerolsteiner’s SAP system. The system updates the data to indicate which pallets are shipped to which customer. In this way, the EU’s traceability requirements are fulfilled.
Before the system was installed, Gerolsteiner relied solely on barcodes to track pallets, and could not identify which pallets were sent to which specific customer. In this way, the company had to hire dozens of workers to scan bar codes manually.
“The company’s annual labor cost for barcode scanning is US$366,000; this project costs about US$1.47 million, which includes software upgrades and non-RFID hardware costs, such as barcode scanners. It is expected that the company will be in the next two years. The investment cost will be fully recovered.” Keul said.
[ad_2]