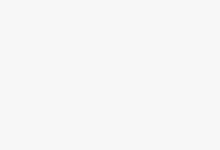
Zebra helps automotive suppliers with precise inventory and transportation management
[ad_1]
Johnson Controls Inc. (JCI) accelerates the service of auto parts aftermarket, and the service to customers such as Mopar, Toyota and Daimler-Chrysler is limited to 48 hours. Recently, the new automatic inventory management and transportation system installed by JCI has successfully improved the service. For customers such as Mopar, JCI has kept a stock of products for several years in order to provide distributors with fast delivery of special parts.
Plant Manager Tom Johnson is responsible for overseeing the work of JCI’s aftermarket service center in Winchester, Kentucky, USA. The center stocks car replacement parts, including seat assemblies and other large car interior components. “We need a system to ensure the correct extraction of existing inventory to meet daily customer ordering needs.”
Today JCI ships repair parts to nearly 8,500 car dealers in North America. It is expanding its automation system to handle parts from other car manufacturers. Johnson reports that the new inventory management and shipping system has greatly improved Mopar’s order fulfillment rate.
history
Johnson said: “Undertaking Mopar’s business means that the required storage space has increased tenfold,” and the storage unit (SKU) has jumped to 9,000. In early 1997, JCI began to evaluate some warehouse management systems (WMS) that could meet its own needs. JCI selected RT System Co., Ltd. and jointly developed a SMART system based on RT LOCATOR WMS products. In mid-1997, the SMART system was ready for operation.
System flow
Mopar Parts Division receives incoming orders through Electronic Data Interchange (EDI), and freight orders are sent to SMART system regularly through JCI system. Most incoming materials have barcodes. If there is no barcode label attached, JCI will make it by itself.
The system uses spread spectrum RF terminals and connected laser scanners to identify incoming products. After receiving the product, the system instructs the operator to enter the part number and quantity, store the product in the vacant storage area, and scan the location bar code to update the system’s product location information.
The freight order is sent to the SMART server, and there are an average of 350 copies per day, and each freight order usually consists of one part. The RT LOCATOR SMART system determines whether the order is a completed product or a part extracted for assembly. The finished product is sent directly to the packaging station. For assembled products, the parts are picked into the bar coded, and the picking box containing the components is sent to the assembly area. The assembled parts are placed in the same picking box and then sent to the packaging station.
At the packing station, the freight clerk scans the picking box, and the system displays the contents of the picking box. After receiving the instruction, the packer puts the parts in the carton of the default specification, unless the product is pre-packaged. Then, choose one of the ten UPS service codes, or select the “Other” item to choose another freight company.
The RT LOCATOR SMART system then prints the barcode shipping label on the thermal transfer printer of Zebra Technology Company, and prints the packing slip on the laser printer. All UPS shipments have a barcode on it, which contains the serial number of the box and the UPS service code used to determine freight charges. The freight information and order information of the UPS system are then transmitted to SMART for updating the JCI system.
Benefit
The RT LOCATOR SMART system improves the accuracy of orders and enables JCI to achieve a 95% customer order fulfillment rate. Since JCI can perform cycle counts in a 140,000 square-foot facility, inventory accuracy has increased to 99.999%. The delivery time of the order is also reduced at the same time.
Johnson said: “In the beginning, our goal was to complete the dealer’s order within 48 hours.” “Now, as long as the required materials are in stock, we can complete the order on the same day through the system.”
The improvement in warehousing response time allows JCI to use other shipping methods to save customers a lot of money. Johnson said: “We can use cost-efficient UPS ground delivery instead of second sky or next-day air transport, but still enable the product to reach the end user within 48 hours from receiving the order.” Response time improvement It has already saved Mopar $114,000 in freight costs.
The next step for JCI is to include General Motors (GM) in its scope of service. JCI began shipping parts directly to GM dealers in February, using a system similar to that used for Mopar. The RT LOCATOR SMART system was not used in order shipments to Toyota. However, JCI plans to transform Toyota’s processes to take advantage of the automation system.
Facts at a glance:
User: Johnson Controls, Winchester, Kentucky, USA
Application: inventory control, JIT freight
Technology: Warehouse Management System (WMS), barcode, radio frequency data communication (RFDC), electronic data interchange (EDI), Windows NT
Benefits: Increase inventory accuracy to 99.999%
Spot orders are shipped out on the day of receipt
Save $114,000 in annual freight costs for MOPAR
[ad_2]