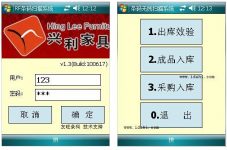
Xingli Furniture Warehouse Management Wireless Barcode System Application Case
[ad_1]
Case description:
In order to finely manage the furniture warehouse, improve the accuracy of goods in and out of the warehouse, reduce errors caused by human factors, and reduce the labor intensity of employees. We have implemented a furniture warehouse wireless barcode management system for our customers. The system uses mobile barcode data collectors for on-site operations and realizes the on-site execution-level information management of warehouse operations.
Hong Kong Xingli Group was established in the early 1990s and is one of the earliest domestic furniture enterprise groups engaged in the integrated operation of furniture design, production and sales. The group’s products include bedroom furniture, living room furniture, study furniture and upholstered furniture. With complete products, after years of continuous development, Xingli Group has grown into one of the largest civilian furniture manufacturers in China.
The group has domestic and foreign well-known furniture brands such as Zundian, Ou Rui, Pinzhi, Times Upstart, Century Sunflower, Saint-Louis, Degas and so on. The group is a furniture summit of neo-classical style and modern fashion style, European style and Chinese style. It satisfies the individual needs of consumers and distributors of different lifestyles, different lifestyles, different consumption levels, and different ages to the greatest extent. Business options.
Features of furniture warehouse management system:
1. The entire system is built on our company’s rapid development platform, which can meet the basic needs of SME warehouse management and can be quickly customized according to customer needs;
2. The wireless collector scans and proofreads in real time, and quickly handle warehousing, warehouse management and other tasks;
3. Documents are automatically generated, reducing errors in manual entry of documents, and ensuring that the number of products in the warehouse is consistent;
4. Record all warehouse operation information, facilitate inquiry and tracking, and standardize warehouse management;
5. Wireless real-time printing of barcode labels, saving warehouse staff from running back and forth between the office and the warehouse;
6. Reduce warehouse management costs and improve warehouse operation efficiency;
7. With ERP software interface, seamless connection can be realized.
Brief introduction of furniture warehouse management system module:
Basic information management
Product data (product composition management), customer data, supplier data, personnel files and other data management
Warehouse management
Material warehousing, finished product warehousing, warehousing return management, location management, purchase payment management
Outbound management
Finished product sales, finished product sales return, material picking, serial number registration traceability
In-stock management
Product adjustment, warehouse inventory, report loss and overflow, assembly and disassembly
Report management
Warehouse storage account, product sales outbound report, product purchase inbound report, product inbound and outbound summary report, product adjustment report, customer sales schedule, customer current account report, customer sales product statistics, customer transaction list, supplier supply Details, supplier current account, supplier transaction list.
[ad_2]