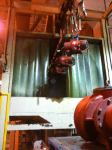
Hanbell Precision Machinery successfully implemented RFID application system for automatic spraying production line
[ad_1]
Project Description
After the automatic spraying robot is introduced into the spraying production line, workers must manually set the working parameters of the spraying robot by observing the types of parts and other information, so as to correctly set the process parameters of the parts to be processed. Manual settings will not only affect the production efficiency of the production line , and is extremely error-prone.
Due to the fact that there is a lot of dust, high temperature and humidity, corrosion and poor visibility in the spray production environment, the automatic barcode recognition technology cannot be applied.RFIDCompared with barcode technology, the technology has many advantages, such as long recognition distance, no need for labels to be visually visible during identification, can be used in harsh environments, content can be updated, multiple labels can be read in batches, and high-speed motion can be recognized. Items, large amount of information, not easy to imitate, etc. Therefore, UHF RFID technology is used to realize the data collection of key processes on the automatic spraying production line, and it cooperates efficiently with the automatic production line and spraying robot system, which overcomes the problems existing in the current system and improves the reliability and reliability of data collection on the spraying production line. Accuracy, greatly improving production efficiency.
key process
Hook labeling: Embed the heat-resistant and corrosion-resistant metal RFID tag on the workpiece hook;
Workpiece hook: When the workpiece is hooked, manually scan the barcode or keyboard to input the manufacturing number of the current workpiece, obtain the machine code corresponding to the workpiece that can be reported through the host computer program, and join the work queue to be sprayed;
Hook writing label: When the workpiece enters the sensor area of the initial process, the host computer program operates the RFID device to write the machine code corresponding to the workpiece into the storage area of the hook RFID tag according to the workpiece in-position command sent by the PLC;
Spraying label reading: When the workpiece enters the spraying process area, the RFID device automatically receives the sensor signal and reads the model code of the current workpiece stored in the hook tag, and returns it to the host computer program, which will transmit the model code through PLC. to the spraying robot;
Label clearing: After the workpiece completes the spraying process, when the workpiece enters the clearing station, the RFID device automatically receives the sensor signal and clears the storage area of the linked RFID tag. If the clearing fails, it is immediately returned to the host computer program and alarmed by the on-site alarm. The machine program controls the production line to stop through PLC;
Device Configuration
Read and write equipment: According to the requirements of the site environment, configure our high-protection, integrated, high-performance SR-4110 industrial-grade integrated reader (RS485 communication interface, 1 photoelectric isolation input/1 relay output, AC220V/0.2A power supply, IP65);
Electronic label: special temperature-resistant, corrosion-resistant and metal-resistant electronic label ST-2525C.
Implementation benefits
1. Automatically collect information such as the workpiece manufacturing code of the spraying process and the model code of the spraying process, which provides an information basis for automatic spraying;
2. Information technology combines sensor technology, automation technology and RFID technology to realize the automation of the whole process of spraying production line, and realize the real integration of the two;
3. The automation of the spraying production line greatly reduces the on-site staff and effectively reduces the damage to the human body from dust and paint;
4. Improve the production efficiency of enterprises, reduce labor intensity, and reduce mistakes;
5. Improve the level of enterprise information management.
Case study
RFID application system of automatic spraying production line of Hanbell Precision Machinery
[ad_2]