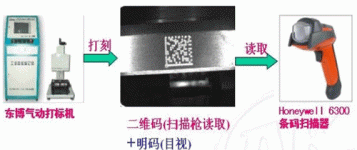
DPM 2D barcode traceability and anti-counterfeiting application case of a foreign-owned automobile axle company
[ad_1]
Company: Foreign-funded enterprise of an automobile axle
Solution: DPM 2D barcode printing and reading
The company has the production capacity and technology of the front, middle and rear axles of MAN Steyr in Germany; the advanced axle technology of the European wheel-side reduction drive axle and the single-stage drive axle of high-speed passenger cars; the advanced axle of the South Korean Hyundai single-stage middle and rear drive axle Technology. The main products are front steering axle for heavy/medium-sized trucks, wheel-side deceleration medium/rear drive axle assembly, single-stage deceleration drive axle assembly and balance shaft assembly, and front/rear axle assembly for large/medium-sized passenger cars. The products cover the rear drive axle of 8-13 ton medium/large passenger car, the rear drive axle and through drive axle of 9.5-16 ton heavy/medium truck, the front steering axle of 4.2-6.5 ton medium/large passenger car, the 4.5-7.5 Tonnage heavy/medium truck front steering axle, etc., a total of nine series, more than 260 varieties, the products are at the advanced level in China.
The company’s production process includes fifteen machining production lines such as axle housing, wheel hub, differential case, wheel side reducer housing, front axle, steering knuckle, etc. Reduced assembly line, front/rear axle assembly assembly line and axle assembly painting line, the company is equipped with a complete set of chemical and physical properties laboratory, axle housing fatigue testing machine, German Zeiss CMM and a number of domestic advanced It has an annual production capacity of 160,000 drive axle assemblies and 40,000 front steering axles.
The main customers of the company’s axle assembly are: Foton Auman heavy truck, Jianghuai heavy truck, Foton Zhucheng automobile, Dongfeng Liuqi heavy truck, Nanqi Lingye heavy truck, Valin heavy truck, Ankai bus, Jianghuai bus, Euro V bus, Yangzhou Yaxing bus , Xiamen Golden Passenger Bus, Zhongtong Bus and other well-known domestic companies.
The company’s quality system passed ISO9001-1994 quality system certification in 1999, passed ISO9001-2000 version change certification in 2002, and passed ISO/TS16949:2002 certification in May 2006. The current quality system covers the Texas branch.
The company adheres to the core concept of “systematic thinking, team learning, coordination and balance, and pursuit of excellence” and the value of “quality is the foundation of enterprise survival and development”, and creates the “super driving, carrying pioneer” Ankai axle brand, with technological innovation, Mechanism innovation, management innovation and marketing innovation enhance the competitiveness of the system, manufacture better products, create a better society, and promote the healthy, steady and rapid development of enterprises.
Application background:
Affected by the global economic crisis in the second half of 2008, the sales of Ankai axles dropped sharply, but the company’s service fees continued to increase. After market surveys and visits to service stations, it was found that counterfeit parts and components were used for Ankai axle products in the market, and the out-of-warranty was pretended to be out-of-warranty. Seriously damaged the corporate image and economic benefits of Ankai Axle. In order to prevent this from happening, an anti-counterfeiting project team has been set up.
The company has already used the MES system, but the system can only achieve the correspondence between the axle assembly and the key component manufacturers in terms of product traceability. Such a correspondence cannot achieve the correspondence between the axle assembly and each key component. This has led to the phenomenon of using counterfeit parts for Ankai axle products in the market, and the out-of-warranty is faked out of the warranty.
At this time, the anti-counterfeiting project team plans to use key components with unique identification codes to be installed in a unique bridge assembly to form a database of dependencies, identify components with a high failure rate in the market, and prevent non-company products and false information.
The first batch of components implemented: the main reducer shell, the wheel side reducer shell assembly, the hub, the brake drum, the balance shaft, the bracket, the balance shaft shell There are problems:
1. The key components in the axle assembly need to be cleaned before the final assembly, and the water pressure is large. The label paper made of traditional stickers will be washed away by the water, resulting in the inability to collect barcodes.
2. Most of the key components in the axle assembly are castings, and the surface has a certain roughness. After coding directly on the components, the contrast between the barcode and the surface of the component is poor, causing ordinary barcode readers to be unable to read the barcode.
Barcode Solutions:
The key components with unique identification 2D codes are installed in the unique bridge assembly, forming a database of dependencies, identifying components with a high failure rate in the market, and preventing non-company products and false information. For example, the component identification code in each bridge assembly is reflected in the product database, and these component codes are unique. It is connected with the quality information of the main engine factory. If there is a replacement of parts, the number of the replaced part will also be reflected in the database. If the identification code of the claimed piece does not match the code in the root bridge assembly in the product database, it will be determined to be a non-our company product.

Customer Experience:
Using DPM barcode as the information carrier improves the accuracy and speed of data entry into the MES system, leaving room for manufacturers to code freely. Suppliers mark according to the coding rules required by the OEM to achieve the uniqueness of key components. Permanent DPM Barcode identification eliminates the influence of traditional barcode identification. The concept of application identifiers runs through the whole process, which is convenient and flexible to read. The successful introduction of DPM barcodes also provides a powerful means for product anti-counterfeiting, and also provides a persuasive solution for product after-sales service. It provides a complete data platform for the realization of MES (Manufacturing Execution System).
[ad_2]