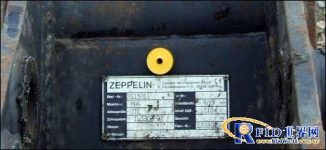
Engineering firm Ludwig Pfeiffer deploys RFID system to optimize equipment tracking
[ad_1]
Recently, Germany-based structural and civil engineering company Ludwig Pfeiffer deployed Advanced Panmobil-suppliedRFIDsolution that eliminates the need to manually trace back 6,000 devices located in Europe, while cutting the time for annual stocktaking in half. According to Ludwig Pfeiffer, the solution saves staff time on traceability equipment and reduces error rates.
Headquartered in Kassel, Ludwig Pfeiffer has 60 construction sites across Europe. Company president Frank Menzel said 6,000 pieces of equipment, including cable drums, excavators and excavator shovels, were deployed on these jobsites. Employees need to monitor equipment when it is in use, inspected, repaired or moved.
In the past, to track equipment, employees needed to manually record all equipment data (location and status) on paper and enter it into a computer. When equipment is moved, the construction site manager fills out a form and forwards it to headquarters for recording. This process takes a long time, the form transportation takes time, and if the handwriting is scribbled, the employees need to confirm the data.
In 2009, the company Ludwig Pfeiffer deployed an RFID solution from Reutemann.net and PANMOBIL. The company attaches a passive 13.56MHz RFID tag to each device, which has a built-in NXP ICODE chip and is compliant with the ISO 15693 standard. For most devices, the labels are attached using glue. For those devices that require a higher degree of adhesion, the labels are screwed or riveted on. Jens Reutemann, sales director at label provider Reutemann.net, said the unique ID number of the label is tied to the device description, serial number and history, and the information is stored in Reutemann.net.
Project squad leaders at each construction site distributed Panmobil Scanndy handheld RFIDReader, the reader can also be used as a barcode scanner. When idle, these readers are placed on docking bays mounted on the project squad leader’s truck.
When the equipment is moved, inspected or has problems to be reported, the squad leader needs to use the reader to read his own badge RFID tag and the tag of the equipment. After being put back on the docking cradle, the reader will transmit the tag ID number and GPS location information to the server via GPRS or UMTS connection.
As the data are received, the Reutemann.net software on the server analyzes them and displays them on the Scanndy screen. In addition, the squad leader can enter more specific information such as equipment failure details, inspection results, etc.
“Because the squad leader needs to scan his badge information, the data of these devices also has a relevant person in charge,” Reutemann said.
When the equipment is moved away from the construction site, the squad leader needs to read the item tag and change the status to “away”. When the device arrives at the new location, the squad leader at that location can read the tag and change the status to “received”.
For those devices that don’t have the right space for RFID tags, the company installs QR code tags. Although QR code tags can also be read with a reader, RFID tags are a better choice, Reutemann explained. He said: “Civil engineering equipment needs to work in some harsh conditions. And when there is some mud or scratches on the QR code tags, they are difficult to use. RFID tags are more durable. So for outdoor work , the QR code is just a plan B.”
When equipment needs repair, the foreman needs to send it back to a repair point at headquarters. Maintenance personnel can view equipment problems on the system. Once the repair is complete, the technician needs to enter the repair details.
“Most employees like this way of working,” Menzel said. “They’re more convenient and less time-consuming. At the same time, supervisors can find the status of equipment in seconds.”
The system is also used for annual inventory counts, where employees need to take stock of all construction sites and equipment in stock. The system is said to cut inventory times in half.
(The exclusive manuscript of rfid world network, please indicate the source author for reprinting!)
[ad_2]