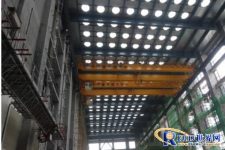
RFID technology is adopted in the construction of laboratory building project of China Construction Technology Center
[ad_1]
The experimental building of the China Construction Technology Center, which is about to be completed, is located in the Linhe Development Park in Shunyi, Beijing, and was built by the Third Company of China Construction Second Bureau. This is a rather special project. After completion, it will be an architectural research center and put into use as a research platform. Therefore, its architectural composition is also different from conventional buildings.During the construction of the project, the project department had encountered many difficulties, but allRFIDtwo-dimensional code and other innovative technologies, so that the problem can be easily solved.
Implanted RFID chip
The first domestic “QR code” plug-in board
The experimental building project of China Construction Technology Center is a large-scale construction project. The project has 2,438 clear-water concrete exterior panels with 214 types of three weights of 2.4 tons, 3 tons, and 7 tons, totaling 12,000 square meters, and the weight exceeds the heaviest exterior panels currently used in China. Among them, the largest single block has an area of 20 square meters, which belongs to the super-large plug-in board.
The more boards there are, the more difficult it is to manage; the heavier the weight, the more difficult it is to control. So many “heavyweight” external cladding boards, if the traditional manual method is used for construction management, are prone to misrepresentation, unclear wear and even omission, resulting in confusion. Eventually lead to inefficiency, which directly affects the construction period. In order to solve the problems of a large number of external panels, heavy weight, complex models and difficult quality control during mass production, the project department decided to introduce the lean construction concept and the RFID radio frequency identification technology developed by the Technology Center of China Construction Corporation, in order to better quality control.
After negotiation, the project department finally reached a cooperation with the external cladding panel manufacturer to produce a clear-water concrete cladding panel with built-in RFID chip for the first time. During production, the chip is implanted into the component, and the chip stores all the information of the specification, model, weight, quality condition, transportation time, installation time, location, etc. in the whole process of the production, transportation and installation of the hanging board. At the same time, in order to cooperate with the application of chip technology, the project department also combined BIM technology to simulate and locate the installation position of clear-water concrete cladding panels in advance, and passed repeated technical demonstrations.
After the cladding board is shipped from the factory to the construction site, the construction personnel scan it with a handheld scanner. Just like the scanning principle of the “QR code” in the supermarket, all the information about the cladding board can be seen at a glance. The installation of the external board still requires the perfect combination of man and machine. First, the crane lifts the external hanging board and moves it to the installation position, and then the construction personnel directly “joint” and use the manual hoist to tighten the external hanging board to push it into place; and then perform accurate docking and installation. In these processes, because of the “two-dimensional code”, the construction has become simpler and more convenient.
Li Jing said that the introduction of RFID technology of Qingshui concrete cladding board chip has effectively shortened the production cycle of prefabricated components, reduced the inventory of all parties, and realized the information sharing of design, production, transportation, and construction of prefabricated components, the linkage of all parties’ plans, and the source of manufacturing. Control and other process monitoring. Moreover, since the chip can accompany the plug-in board for life, it can realize the quality traceability of the whole life cycle. “In addition, the surface of the cladding board is protected by imported fluorocarbon resin paint, which has the functions of self-protection and self-cleaning,” added Zhao Zhiguo, the technical director.
It is reported that this project has achieved the most important in China and the first in China to use RFID chip technology to control and manufacture clear-water concrete external cladding panels, and the manufacturing technology has reached the domestic first-class level.
Overall upgrade of the unit
Innovative 33-meter-high recovery space construction
How to construct the 33-meter-high restoration space? Use the traditional scaffolding construction scheme, or other innovative construction schemes? After research and practice, the project department successfully adopted an innovative scheme for overall improvement of the unit.
The reporter saw at the scene that most of the restoration space with a total area of 2,450 square meters has been completed, and only some areas are still being completed. The construction site is still busy.
“It is very difficult to complete the construction of an outdoor space as high as 33 meters.” Li Jing pointed to a busy construction site and told reporters, “First of all, we must not adopt the usual method of construction, then the whole area needs to be set up with scaffolding and construction. The cycle is long, and ultimately directly affects the node target of the construction period.”
The usual construction method cannot be adopted, the recovery space is so high, and the quality assurance and safety must be guaranteed. What should we do? Li Jing said that after repeated research and demonstration, the project department finally adopted the electric hoist unit block to upgrade the construction plan. 3 mm thick aluminum veneer (150 cm x 300 cm), each 4 pieces per unit, assembled on the ground, the unit is lifted, placed in the air, connected and fixed, the elevation is leveled, and the construction is finally completed.
After the aluminum veneer is raised to the elevation control point, the installation and leveling construction has become a major difficulty in the construction. First of all, to ensure the flatness of the restored space ceiling; secondly, to ensure the uniformity of the aluminum veneer combination, it must be horizontal and vertical. In this way, the construction level and comprehensive quality of the construction workers are greatly tested.
“But overall, our construction is still very smooth.” Li Jing said with relief, “practice has proved that our new technology is completely correct.”
Do not stick to traditional methods, and strive to seek innovative breakthroughs. The project department takes technology as the guide, guides the construction with technology, and successfully realizes it, which not only improves the efficiency and saves the construction period, but also creates an immeasurable wealth of technology and experience for the project department.
[ad_2]