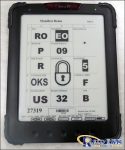
Omni-ID View 10 Tablet Device Integrates RFID Technology to Help Manufacturing Assembly Processes
[ad_1]
The View 10 tablet device uses passive and active RFID technology, WiFi and infrared (IR) technology, a 10.1-inch display and enough memory to store at least 160 pages of text information, which can replace paper operating instructions during assembly , save paper and improve assembly efficiency.
In an effort to save paper in the assembly process of the manufacturing industry, RFID research and development company Omni-ID has launched a device called the View 10.RFIDtablet device. The size of the device is 8 inches by 11 inches. The device includes a 10.1-inch electronic display, multi-protocol, multi-frequency RFID tags: active 433 MHz RFID tags (ISO 18000-7 compliant), passive UHF RFID tags (EPC Gen 2 and ISO 18000-6C compliant). In addition, a sensor is attached, which mainly receives data from infrared signals and wifi transceivers.
View 10 can be installed on automatic engines or other products on the assembly line, not only to locate products based on wifi data, but also to track product status on the assembly line based on RFID and infrared technology. At the same time, the operator can operate according to the operation instructions automatically displayed on the View 10 screen, and the operator no longer needs to manually turn the pages of the operation instructions.
The main target customers of View 10 equipment in the past 18 months are automatic manufacturers or manufacturers of large-scale goods production materials. The first customer, Detroit Diesel, has been testing the device for a year and is planning full-scale adoption. Omni-ID is currently in talks with a pharmaceutical manufacturer to implement the View 10 device into the pharmaceutical manufacturing process.
Omni-ID View 10 Devices
The new tab memory size in View 10 is 25M, enough to store 168 pages of visual text. The View 10 device acts as a real-time locator tag to track products as they go through the assembly process. Also, as an e-book, the operating instructions are automatically played.
The View 10 device is fixed in a plastic case and acts as a wifi transceiver, sending and receiving data such as location through the wifi network. EPC Gen 2 RFIDReaderInstalled at the job site, transmits a unique ID code to the tag. The UHF RFID reader works with the View 10: the tag forwards the data to the ProVIEW software (installed on the Detroit Diesel server, which uses the ID number of the specific reader and the engine tag to determine which page of instructions is needed and opens it .), meanwhile, the software stores the tag’s location data (based on the reader’s location). If an employee wears an EPC Gen 2 RFID tag wristband, the reader sends the wristband ID code to the ProVIEW software.
The solution can also use infrared transmitters instead of EPC Gen 2 UHF RFID readers to complete location determination and open appropriate operating instructions. The View 10 includes a 38 kHz IR receiver, of course, other frequencies of IR are also available, as needed.
When the operator encounters a problem or other request, such as “want more blue paint”, “need to weld steel wire”, he/she can press one of five operation buttons, different buttons represent different operation requirements. At the push of a button, the ProVIEW software will send an alert to remind you to replenish the ingredients. View 10 also alerts assemblers of, for example, errors in the assembly process.
After product assembly is complete, the View 10 can be used in other product assemblies. Assembly records and operator information are stored in ProVIEW software. Active 433 MHz RFID tags can also be used to replace the wifi network, and the 433 MHz RFID reader will transmit data such as tag location to the backend server.
The advantages of the View 10 compared to tablets are reflected in the following aspects: it can withstand harsh manufacturing environments more than ordinary tablets; it provides location data. Although the price is higher than the ordinary tablet, it will have a higher return on investment in 9-14 months, while saving the cost of paper. In addition, labor and data storage time are saved.
[ad_2]