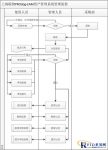
Shanghai Lianwu assists the asset management of SAIC Passenger Car TV Department
[ad_1]
1. Customer background:
SAIC Motor Group Co., Ltd. is one of the four major automobile groups in China, mainly engaged in the production, sales, development, investment of passenger cars, commercial vehicles and auto parts, as well as related auto service trade and financial business.
The TV department is an important department of SAIC Passenger Vehicle R&D Center. Its main responsibilities are to do new car trial production for new SAIC Passenger Vehicles, and to conduct auto parts and performance tracking for competitors.
2. Challenges faced by customers:
my country’s automobile manufacturing industry has not been as good as the blowout period in recent years, and SAIC Group is one of the leaders. Since 2004, SAIC Motor’s passenger car manufacturing and sales scale has continued to expand, and the TV department, which is responsible for new car trial production and research on auto parts and performance of its friends, is facing more and more challenges:
Excel-based asset management faces complex application challenges. Previously, the assets and important parts management of SAIC TV Department were manually created by administrators in Excel spreadsheets and archived. There are many problems with this: low entry efficiency; inability to comprehensively manage (two-dimensional data recording); and it is difficult to make associated modifications when assets are changed.
Paper forms and manual approval processes. The TV department has relatively strict procedures and procedures such as purchase application, order application, asset transfer, asset loss, asset scrapping, etc., but they are all approved through paper signatures, which are difficult to retrieve or view after a long time. Conducive to sorting, statistics, classification, low efficiency.
Periodic reconciliation of assets is time-consuming and labor-intensive, and data is inaccurate. In the year-end inventory work, administrators and employees generally record assets in Excel according to the declaration-record mode, which will lead to inaccurate inventory process and consume a lot of manpower and material resources.
Only manage asset data without lifecycle management. There are a lot of equipment assets in the TV department that require regular repair/maintenance/calibration, which becomes more difficult as the equipment assets increase due to the previous maintenance schedules that were performed manually. At the same time, it is impossible to grasp the overall usage of the assets.
ISO20000 audit requirements. Since the TV department is affiliated to SAIC Motor, it needs to implement the ISO20000 standard. Its standards focus on managing IT problems through “IT service standardization”, that is, classifying IT problems, identifying the internal connections of the problems, and then planning, implementing and monitoring them according to service level agreements, and emphasizing communication with customers. The standard also focuses on the capabilities of the system, the management level, financial budget, software control and distribution required for system changes. The current management system cannot meet this requirement.
3. Solutions:
Since the TV department is more sensitive to cost, bar code identification is used as the asset identification method, and the PROdog-EAM (hereinafter referred to as: EAM) system is used to digitally manage the assets. All material information is registered in EAM through barcode scanning, and the administrator enters all material information (maintenance, depreciation, responsible person, photos, etc.) into EAM. When the equipment needs to be counted, the asset manager can scan the asset with a barcode gun. At the same time, the original procurement-approval process is digitized in EAM. Summary This EAM system has the following functions:
All-round digital management of TV department assets;
The approval process is digitized. Utilize the EAM system to digitize the asset approval and purchase process without passing paper documents;
Asset barcode inventory. The inventory information can be quickly compared with the EAM ledger, and a difference report can be issued;
Digital management of maintenance and calibration information. Send the above information to the asset manager on time through EAM;
Report automation. The required asset reports can be generated automatically;
Synchronization with SAP ERP (asset information).
Asset management has the following processes:
4. Application benefits
Accurate asset management. The TV Department uses EAM to manage and record details of all assets, as well as contracts, orders, requisitions, prices, residual values, users, owners, repair records, warranty types, warranty expiration dates, software running, licenses, etc. Asset related information.
The EAM system is embedded with a workflow engine, which can help the TV department to complete asset application, asset ordering, asset transfer/borrowing, asset scrapping, asset loss processes, ensure the corresponding relationship between asset numbers and asset serial numbers, and ensure the integrity of equipment information.
Asset lifecycle state management. EAM manages the lifecycle state of assets. Asset administrators can easily query and count various asset information to provide accurate support for decision-making. At the same time, changes in asset lifecycle status will automatically trigger various background processes to ensure accurate and timely updates of asset data.
Borrowing management. A set of digital management process is formulated for the borrowing of assets, which makes the management process more standardized and traceable.
Report automation. According to the needs of the TV department, reports are generated for all registered assets by time period and other conditions.
5. Software interface
[ad_2]