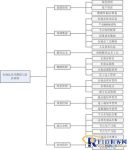
RFID-based work in process location tracking system case
[ad_1]
Project Background
along withInternet of ThingsWith the rise of technology, the domestic manufacturing industry generally realizes that through the Internet of Things and other technologies combined with management systems such as enterprise informatization MES, through the Internet of Things wireless sensor network, RFID tags and other technical means, the real-time process tracking and data collection of the production process of the manufacturing assembly line can be realized. , so as to improve the visualization and controllability of the workshop manufacturing process and increase the production efficiency of the enterprise. The visualization and controllability of the production process is an important reference factor for the formulation of production plans and the on-time delivery of products. The important role played by the digitization of manufacturing management, visualization and controllability of the production process has brought considerable economic benefits to the enterprise.
Situation Analysis
Due to the weak foundation of informatization and low production efficiency in my country’s traditional manufacturing industries, the implementation of informatization in the manufacturing industry, especially the traditional manufacturing industry, is an urgent task that needs to be solved. How to collect and manage workshop-level production information to achieve the effect of “pre-prediction planning, in-process analysis and control, and post-event tracking management” has become one of the directions of manufacturing informatization.
At present, the monitoring of the production process of XX Group’s garment factory is still conducted through the management personnel to the workshop site to understand the situation, and then manually input data to record, count and form workshop reports. The workload is large and the efficiency is low. Asset inventory is inefficient and data cannot be shared.
There are mainly the following problems:
– There are too many machines, and traditional manual records are used for entering and leaving workshops and warehouses, resulting in low work efficiency
-When each production line often borrows machines from each other, there is no record, which makes it difficult to track the whereabouts and location of the machines in real time.
– When a special product needs a special machine, it is impossible to find the corresponding car in time and make pre-production preparations, thus affecting the timely delivery of the order
-When the machine operated by the worker breaks down, the maintenance order needs to be filled out manually and delivered to the maintenance box. After the maintenance personnel get the maintenance order, they still need to spend a lot of time to find the specific location of the sewing machine, which leads to low maintenance efficiency and affects the production capacity of the equipment. operation
– Maintenance personnel cannot quickly record the start and end time of maintenance, which affects the company’s evaluation of maintenance personnel’s work performance
– Since the entry and exit records of the machines are all manual operations, it is impossible to count the utilization rate of the machines and equipment
– During the year-end and year-end inspection of the chassis, a lot of manpower and material resources are required for inventory, resulting in poor inventory accuracy and low inventory efficiency
– It is impossible to track the information of the current position and work step of the machine in the workshop in the whole process, in time and automatically.
– Real-time and accurate control of the actual working hours of each car cover restricts the effectiveness of the planned production schedule, and at the same time, it is impossible to carry out value engineering.
– Due to the non-real-time tracking of each link of garment processing and production, the timeliness of job scheduling and line-side material distribution is poor. At the same time, it also restricts the uniformity inspection of assembly materials, thereby affecting the production and distribution efficiency of warehouses, supporting manufacturers and supply chains, and restricting the JIT production model.
– Poor traceability, lack of tracking and tracing of the genealogy of the entire vehicle, including assembly time, operating workers, working hours, assembly parts and other information, which affects the efficiency and quality of quality control and after-sales service.
– The internal ERP/MES system cannot share data with the car clothing
System functional goals
This project plans to adopt radio frequency identification (RFID) technology to achieve real-time tracking and automatic warranty, material shortage reminder and real-time inventory of the whole process of car clothing. Through the implementation of this project, the following objectives can be achieved:
– Real-time status tracking of the whole process of the machine. Accurately know the location and status information of the machine in the electronic map.
– Record and store the motion trajectory of the sewing machine in real time, and trace the relevant historical data.
– Accurately record the start time and end time of maintenance, support the input of the failure cause of the sewing machine, so as to better manage the quality life cycle of the sewing machine.
– Carry out automatic inventory of sewing machines anywhere, reduce the loss rate of sewing machines, and improve the utilization rate of sewing machines.
– By classifying and managing different workshops, different long lines, and different types of sewing machines, and visually identifying them in the electronic map by color, it supports real-time query classification information in reports.
– Trigger applications such as material shortage and repair report in real time by using electronic tags.
– By using the reader to trigger the reporting method in real time, the reporting time is reduced and the reporting accuracy is improved.
– Through the tracking and real-time monitoring of the production process of the sewing machine, understand the processing and assembly process of the machine, reduce the abnormal processing time, and improve the on-time completion rate and delivery rate.
– Track and manage the genealogy of the machine (historical processing/source information of the vehicle and its components) to facilitate quality traceability.
– Integrate with MES and ERP systems within the group for data sharing.
– Integrate the collected production process information with ERP, MES and other business systems to drive the efficient and high-quality operation of business modules such as material management, distribution management, production scheduling, planning and scheduling, quality control, and after-sales service.
– RFID acquisition equipment can adapt to complex working conditions and environmental interference on site.
expected result
The expected results achieved by the system implementation include:
– Improve management efficiency and enhance the adaptability of enterprises through automatic identification and data collection methods such as RFID instead of manual processing of information;
– The information system will be extended to the underlying automation. A large amount of underlying real-time data is input into the system through RFID, so that the information system is bound to continuously expand to the underlying automation and improve the flexibility of the assembly process;
– Bridging the gap between planning and execution time in enterprise production systems. The information system using automatic identification and data collection methods such as RFID can obtain real-time production data in time, realize the automatic tracking of the whole process of the machine, and seamlessly integrate the data and application through the network information transmission channel to provide decision-making support for the enterprise management. Bridging the gap between plan release and production execution, reducing the blindness of plans;
– Changes in the concept of safety stock and manufacturing batches. The application of RFID in factories and warehouses will make the incoming materials of upstream processes (or enterprises) and the needs of downstream processes (or enterprises) completely transparent, thereby realizing just-in-time (JIT) and mass customization (MC) production methods.
In this solution, the key technologies/products and difficulties involved include the following aspects:
IoT integrated management platform:
Quick customization, adapt to various industry application systems through interface scripts;
Support mainstream RFID reader products, provide Http, Soap, JMS and other protocol support for the upper layer, and provide Web Service interface;
Provides monitoring, configuration and management of RFID readers. Provide a flexible and extensible framework to support ALE specification upgrades and rapid integration of new RFID readers;
Mount the label precise positioning module to support high-precision label positioning;
Provide label data automatic generation module;
Provide enterprise-level operating quality, stability, efficiency, security, manageability, and scalability.
Distributed reader technology:
Support low-cost large-scale incremental networking;
Large-capacity reader unit, more than 50 times more than traditional;
Flexible networking model of wired and wireless combination;
The reader control unit can be independently deployed in the core computer room for centralized maintenance;
Control unit supports hardware upgrade;
A single reader can control more than 500 RF nodes;
Decentralized coverage through the Internet.
Continuous, precise, real-time RF positioning technology:
Track value targets to pinpoint precise granular activity within coverage;
Low-power design, optimized active tag collision algorithm saves half the power;
Precise positioning, the world’s leading radio frequency positioning algorithm;
It can automatically record the station information and movement information of the sewing machine;
Only a small number of positioning readers need to be deployed according to a specific algorithm;
Need strong algorithm research support;
RFID WIP Production Line Positioning Tracking System Functional Diagram
Team Background:
Suzhou Xindao Intelligent Technology Co., Ltd. has a technical team of more than 10 people, of which more than 90% are undergraduate and postgraduate degrees, specializing in microelectronics, electronic information, computers, mechanical electronics, machinery manufacturing, etc. The core technology backbone has long-term He is engaged in the development of electronic communication products and manufacturing informatization, and has rich development experience and technical accumulation in the fields of weak current system integration, RTLS wireless positioning, RFID IoT integration and manufacturing informatization.
Suzhou Xindao Intelligent Technology Co., Ltd. and its partners have taken the lead in developing a full range of readers, read-write heads and label products (low frequency 125KHz, high frequency 13.56MHz, microwave 2.4GHz) dedicated to the manufacturing field. , high temperature and high pressure and other key technologies have domestic leading technical advantages. Widely used in RTLS wireless positioning, RFID asset management, food safety traceability and other fields.
[ad_2]