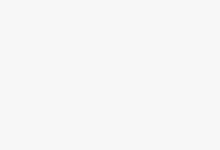
The sign card of Mulan Electronic Personnel Mobile Positioning System was successfully applied in Zhangjiagang Cross-Ocean Wharf
[ad_1]
1 Introduction
In recent years, some flammable and explosive factories are prone to fire, explosion and other safety accidents. Although there are obvious warning signs in the factory area, people often ignore these warnings and still go their own way and ignore them. Some places in the factory are not allowed to enter, exit and stay casually, but people have time to be curious and sneak in when no one is around; there are also some management and responsible personnel who cannot go to work on time and check, Bring hidden dangers to safety accidents.
How to strengthen the preventive measures for safe production, how to correctly handle the relationship between safety and production, safety and efficiency, how to accurately and real-timely perform the safety inspection function of the flammable and explosive industry, and ensure the efficient operation of emergency rescue and disaster relief and safety rescue, are placed in the country. In front of competent departments and leaders at all levels. At the same time, how to change the current management mode of flammable and explosive enterprises’ backward management of on-site workers, and how to realize the modernization and informatization of management have also become the concerns of all flammable and explosive enterprises. We believe that it is imperative to establish informatization and intelligentization with disaster prevention, accident rescue, and electronic information management as the main goals.
To this end, we have launched a plant personnel positioning monitoring system and a plant equipment management system.
The above system can achieve the following functions:
1.1 Real-time display of geographic information through GIS technology can display the situation of the factory site in real time
1.1.1 At any time, how many people are there in the factory site or at a certain location, and who are these people.
1.1.2 The trajectory and route of each person’s activities in the production area at any time can be displayed on the software
1.1.3 Query the actual location of one or more people, so that the control center can contact the person.
1.1.4 Inquiring about the arrival or departure time of the responsible personnel at any location and the total working time of a series of information can supervise and confirm whether the important inspection personnel conduct the testing and processing of various data on time and point, fundamentally Try to avoid related accidents caused by factors that you believe.
1.1.5 Multi-point sharing can be achieved for multiple leaders to view at different locations.
1.2 Real-time dynamic distribution of on-site personnel at every moment, and make corresponding dynamic diagrams according to the on-site situation, so that the on-site situation is clear at a glance.
1.3 Automatically count various reports of various personnel
1.3.1 Production staff’s attendance schedule, monthly attendance report, overtime report, leave and absence report, salary report, etc.
1.3.2 Formulate and count the inspection reports of the inspectors
1.3.3 Other personnel: such as whether the visiting and inspecting personnel arrive at the designated area as required, and whether they walk according to the designated route, etc.
1.3.4 In the event of an accident, it is immediately possible to find out how many people are in distress, who they are, where they are in distress, etc.
1.4 The functions implemented in device management include
The exact location of the vehicle and other important equipment
Record the number and frequency of in and out of work vehicles for easy management.
2. System introduction
System Features
○Highly automated
○Advanced network communication system
○Perfect data analysis system
○ Geographic information display and query system based on GIS technology
○Safe and reliable, it can work normally for 24 hours under severe wake-up
Product performance
○Long distance, the effective recognition distance is adjustable from 2 meters to 80 meters.
○Highly anti-collision, using a variety of anti-collision schemes, can identify more than 200 signs at the same time.
○ High speed, the moving speed of MLRFID can reach more than 200 kilometers per hour.
○High recognition reliability, the misread rate is less than 5/100,000.
○Easy installation, integrated design, no need for external antenna or ground sense.
○Intelligent, two-way high-speed data exchange can be realized between RFID and transceiver, making the application flexible,
○Data security is guaranteed.
○ Can realize directional and non-directional recognition.
○High reliability, suitable for industrial and mining working environment (-40℃-85℃), waterproof and shockproof.
○Low cost, all 0.18uM chips are used, and the cost is lower.
○Ultra-low power consumption, healthier and safer.
○The global open ISM microwave frequency band does not need to apply and pay.
○High anti-interference, no special requirements for various on-site interference sources.
How the system works
First, place several card readers at each intersection of the factory area and in the passages that all personnel may pass through. The specific number and location are determined according to the actual working conditions on the site and the functional requirements to be realized, and they are wired through the network and the ground control center. Computer networking. At the same time, on a work card (radio frequency card) worn by each staff member, when the staff enters the factory area, as long as they pass or approach any card reader placed in the factory area, the card reader will immediately sense the signal and immediately Upload it to the computer in the control center, and the computer can immediately determine the specific information (such as: who, where, and specific time), and at the same time display it on the large screen or computer display of the control center and make a backup. Managers can also click on a certain position in the factory area according to the distribution diagram on the big screen or on the computer, and the computer will count and display the personnel situation in this area. At the same time, the computer in the control center will sort out various attendance reports (such as attendance rate, total attendance time, late arrival/early departure record, non-attendance time, etc.) In addition, once an accident occurs in the factory area, the personnel at the accident location can be immediately found out according to the personnel distribution information in the computer, and then special detectors can be used to further determine the location of the personnel at the accident location, so as to help rescuers rescue them in an accurate and fast way. trapped persons. Vehicles and other equipment are managed in much the same way.
System composition
System Design Principles
○Realize the effective identification of workers entering and leaving the factory, and make the system management fully reflect “humanization, informationization and high automation”
○Provide senior management personnel with various information inquiries such as attendance work, personnel entry and exit restrictions, etc.
○In the event of a safety accident, the number of workers in the plant can be immediately known through this system, ensuring the efficient operation of emergency rescue and disaster relief and safety rescue work.
○After a safety accident occurs, through the mobile identification device of this system, it is possible to detect whether someone exists within 10 meters of the accident site, which is convenient for the timely development of rescue work.
○The security, scalability, easy maintenance and easy operation of the system design.
System Design Features
(1) Highly automated. The system can automatically detect the time and location information of factory workers passing through the monitoring point, and automatically realize the statistics and management of attendance.
(2) Advanced communication system. The identification system installed in each area of the factory area transmits the data passed by the relevant personnel to the network server in real time, and the whole process does not require human intervention.
(3) Complete data statistics and information query software. The system software has a dedicated database management system, including the information collection and statistical analysis system for workers through the factory area, the statistics and management analysis system for attendance operations, and displays and prints various statistical report data, providing a full range of query and management for senior management personnel. Serve.
(4) Safety, stability and reliability design of the system. The system product adopts the tunnel wall-mounted design, which eliminates the need for on-site construction in the tunnel, and ensures the continuous and normal operation of the system for 24 hours in harsh environments;
(5) Perfect abnormal situation (including invalid sensor, invalid sensor entry) alarm call system configuration.
system design
This system follows the principle of “unified issuance of work permits, unified equipment, and unified management”, and implements the “one-person-one-work permit” system for the permitted personnel and teams. The specific plans are as follows:
(1) The production unit installs a certain number of card readers in all plant areas. The specific locations are determined according to the site conditions, and the radiation area shall prevail.
(2) The production unit issues a work permit to the relevant personnel, and the work permit is worn at the appropriate position of the personnel.
(3) The basic information of the employee corresponding to the radio frequency card when the work permit is issued, including name, age, gender, team, type of work, job title, and personal photo, etc., are logged in the system database.
(4) The work permit will take effect after the work safety department authorizes it. The scope of authorization includes: the area where the employee can be qualified to enter the work surface, the time limit, invalidation, and loss of the work permit, etc., to prevent irrelevant and illegal personnel from entering specific areas of the factory;
(5) Personnel entering the factory area must wear work permits and safety helmets. When the person passes through the identification monitoring point in a certain area, it is immediately recognized by the system, and through the information exchange of the system network, the information such as the road section and time passed by the person is transmitted to the safety monitoring center on the well for recording, and can be recorded in the geographic information at the same time. A prompt message appears on the screen wall, showing the name of the person passing through. If the sensed sensor number is invalid or enters the restricted channel, the system will automatically alarm, and the on-duty personnel of the safety monitoring center will receive the alarm signal and immediately execute the relevant safety work management procedures.
(6) Once a safety accident occurs in the plant area, the safety monitoring center can know the basic situation of the trapped people at the first time. Safe and efficient operation of ambulance work.
(7) According to the actual situation of the factory area, we solved the technical problems of applying system products to the flammable and explosive factory area:
a. The problem of safe operation of the equipment itself in the factory area: According to the special environment and working characteristics of the factory area, our equipment (card reader) has achieved: it adopts an all-metal shell, with a solid structure, anti-collision and shock-proof. Fully sealed design, waterproof, moisture-proof, anti-corrosion,.
b. The operation of the equipment must not affect the safety of the factory area: the equipment has ultra-low power consumption, and the peak power is less than 1 mW.
c. The problem that the working voltage of the system in the factory area is less than DC 12V
d. The equipment is suitable for various installation environment problems in mines, underground and inflammable and explosive occasions: the equipment has a very high anti-interference ability and basically has no requirements on the installation site, which ensures the high reliability of the equipment operation and greatly simplifies the operation. Install a maintenance workload.
e. The whole system is designed to be “fool-type”, which requires extremely low technical level of users, and has simple and adjustable functions, automatic inspection functions for faults, and so on.
f. Simple construction and installation problems in the factory area: The product is directly wall-mounted and can be connected to the DC power supply and the network cable connector. It is also very convenient and easy to change and add the inspection points in the factory area in the future.
g. Simplification of fault handling: when a machine fails, it can be directly replaced with a spare machine.
3. Contact information
Tel: 86-0512-87655880
Fax: 86-0512-87655879
Email: [email protected]
Website: http://www.mlrfid.com
Address: Room 505, Building 1, Industrial Building, No. 625 Binhe Road, Suzhou City
Contact: Bai Chunyu Hui Gang
Mobile: 13862423497 15962169748 15306134346
4. Copyright Notice
The copyright of this technical solution belongs to Suzhou Mulan Electronic Technology Co., Ltd. Without written permission, any organization or individual shall not quote it in any form, otherwise Suzhou Mulan Electronic Technology Co., Ltd. will reserve the right to pursue legal responsibility.
[ad_2]