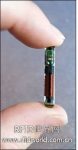
RFID underground oil well valves help drillers maximize oil extraction
[ad_1]
Over the past few decades, oil companies have attempted to apply a variety of techniques to control tools in oil and gas wells thousands of meters underground; however, due to the high pressures, high temperatures and corrosive environments in oil and gas wells, manycan’t work stably.
Now, Scottish company Petrowell has designed a system that uses RFID technology to wirelessly communicate with underground oil well tools such as valves.This system can help oil companies strategicallyExtraction, extracting the maximum amount of underground oil and gas, the company said. Petrowell has now patented the system.
This is first and foremost thanks to the technology of directional drilling, which allows oil companies to extract oil vertically or horizontally. The miner drills down the field vertically, then rotates the bit 90 degrees and drills laterally at the lowest vertical point. A well can reach 3-4 kilometers deep and 10 kilometers laterally.
Due to the lack of large, untapped oil fields in the world today, this type of directional drilling is highly cost-effective. The vertical extension of oil wells can connect some small-area, non-connected oil fields or natural gas fields, avoiding the exploitation of new fields. In other words, directional drilling enables a single well to connect 6-10 small fields without drilling 6-10 different wells from the surface.
If the small oil and gas fields in the vertical direction are fully exploited, the company may not be able to extract the maximum amount of oil and gas in the horizontal direction, according to Petrowell design engineer Daniel Purkis. The company has been working to solve this problem for the past 5 years and has recently started selling RFID underground tools for surface manipulation.
According to Purkis, oil and gas flow first from the bottom of the well — the vertical zone, the point at which the drill bit rotates 90 degrees. If the oil at the bottom starts to run out, the well produces water, which blocks the bottom of the well – the horizontal area of the well.
“It costs about US$72-14,300 to drill a well in Angola, and if the new well only comes out with water after a month, that’s a big problem,” Purkis said.
By controlling the valves in the vertical and horizontal directions of the oil well drill pipe, the company can first exploit the small fields furthest horizontally and then come back vertically, preventing water from clogging the flow of oil. However, this timed and strategic extraction is not ideal if surface tools cannot control the valve stably.
There are a few systems on the market that control tools in wells, but Purkis said the mining industry considers these systems to be unstable. Hydraulic lines are a common method of underground tool control.
“It’s like a car’s brakes,” Purkis said, adding that hydraulic lines can be as long as 20,000 feet. Hydraulic lines are very expensive and fragile. If a well needs to control 6 tools, then the system must use 6 hydraulic lines.
Another option is cable. However, the cables also need to be 20,000 feet long and are expensive, Purkis said, and are prone to damage because they have to withstand the corrosive and high temperature environment in the well. In addition, the hydraulic lines and cables require surface control boxes and engines, which take up surface space. “You know that the bottom of an oil rig is an ounce of gold,” Purkis said.
The Petrowell designed system installs RFID readers in other tools such as underground valves. Mining workers place passive RFID tags into the fluid flowing down the well, and the tags send relevant commands as they pass the reader.
Downhole Glass Sealed Labels
In Europe and North America, Petrowell and Marathon Oil Co have jointly conducted several tests. For the test, Petrowell installed a battery-powered RFID reader on the drill pipe valve. Mining workers drop a handful of loose, glass-sealed RFID tags down the well, which travel with the liquid horizontally or vertically and communicate with the readers they pass through the valves.
“By controlling the valves, the system balances the flow of oil, allowing us to get more oil faster” The tag sends coded information to a specific valve in the well, instructing the valve to remain static or active, such as open or closed, as in the code The number 6 may represent the valve closed or open, or 10% closed.
According to Purkis, the system is designed redundantly, with multiple tags programmed with the same instruction being thrown down the well at the same time, in case some RFID tags become unreadable or break. In addition, the system also has a detection mechanism, if a tag passes through the valve, then it is impossible to re-pass the same valve, causing the valve to react unnecessarily.
“The worst that could happen,” Purkis said, “is a loitering tag activating the valve at the wrong time, or activating the wrong valve. This could lead to an explosion and a fire.” To prevent such situations, Petrowell must guarantee the security of the system. A tag must be timed and sequenced before it is thrown into the well. In this way, after a certain period of time, the tag commands are invalid and the reader only reacts to new tags. The tags end up at the bottom of wells or embedded in rocks.
The labels are available in two sizes, one with a diameter of 4mm and a length of 24mm; the other with a diameter of 2mm and a length of 8mm. Labels were purchased from TI and modified by Petrowell.
The tag read rate is determined by the speed at which the tag falls into the well and the turbulent eddies. The average read rate of each tag is 60-79%, and mining workers generally put in 10 identical tags at the same time to increase the read rate to 100%. For example, an operator drops 10 tags with commands to close a valve by 5%, and the rate at which the well is pumping shows the change in valve setting.
The RFID system is installed and tested during the well’s commissioning phase, and Purkis said the miner initially had to toss the tag 3-4 times a day to adjust the settings. When the well is in production, the tags only need to be thrown out once a month, or on demand.
The system is currently in use, although Purkis declined to name any other testing company other than Marathon Oil. However, he said the system was recently sent to a Canadian company and international oil company Saudi Aramco
Additionally, a major company is currently considering installing a system to monitor heat, pressure and fluid flow rates in wells.
“Our RFID application is so unique that our partners say it will change the way oil wells are drilled in the future,” Purkis said.
[ad_2]