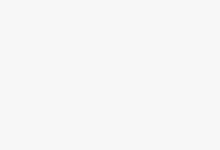
RFID technology enters the construction industry to challenge harsh environments
[ad_1]
The builder, Fluor, was responsible for all three phases of testing. Fluor is one of the world’s largest builders, a large company integrating design, procurement, maintenance and construction. Fluor assigned one of its material production companies, Shaw’s production plant, to conduct RFID testing.
At the same time, Fiatech, a non-profit construction company, material supplier, and academic research consortium, is also highly concerned about this project. The main task of the consortium is to promote the development and industrialization of advanced technologies in the construction industry. Fiatech was created by the Texas School of Architecture, the University of Texas, the National Institute of Standards, and the Construction Industry Research Library.
John Wadephu, Fluor’s chief logistics management manager, said: “To make the whole test more professional, Fiatech invited some other construction companies, production plants, and end customers to participate in this test to see if RFID technology can be introduced into the construction industry.”
Fiatech considers this technology very carefully. Charles Wood, program manager at Fiatech, said: “We heard that in tests a few years ago, passive tags did not prove to be much better than barcodes.” help, and must be seen like a barcode.
For testing, Fluor wants to put a label on the casing, which is a unique part of a steel or carbon steel forging that will later be welded to other casings in the field to make pipes that meet specific design requirements. Casings range in diameter from 2 feet to 8 feet and can be up to 40 feet in length.
“We wanted to put tags on items that we thought would need to be tracked all the time, but were very difficult to track,” Wadephul said. “The tubes are all pressed one by one, and the tags can’t be seen at all.”
Currently, the casing is barcoded at the production plant and then transported to the construction site, where the delivery is checked, but the process is far from satisfactory. Wadephul said, “Most sleeves have barcodes on them, and there are barcodes on the packaging list, but not on every sleeve. At the same time, the factory can easily identify each sleeve with the naked eye, and then use the Deliveries are recorded in the office via barcodes on the packaging list.”
The advantage of RFID is that it can automatically speed up the delivery and inventory identification process, while reducing the trouble of checking with the naked eye or needing to look at the barcode to read the barcode – especially for items that are neatly stacked during transportation. If RFID technology can be applied to the casing, the potential market is very large. Wadephul said, “A single project uses 1,000 to 10,000 casings.”
The first phase of testing is to see if the tag can work in an environment surrounded by metal. The basic characteristics of RFID are radio waves, which are susceptible to metal interference and rebound. When the tag is fixed on a metal object or there is a large amount of metal in the surrounding reading environment, reading errors may occur. Based on this, Fluor and Fiatech turned to Identec Solutions for active tags and readers. “This is the worst environment in which labels can be placed,” said Barry Allen, Identec’s technical director.
The goal of the first phase of testing: to find a labeling technology that can meet environmental requirements. Put Identec’s iQ active tags on 20 to 30 casings and see if the tags can be read at a range of 10 feet, the selected tags are 915 MHz active tags with a read rate of 100 per second tags (read-only ID number), or 35 per second (128bits data). In addition, the reader can handle 2000 tags in the same read and write area, and the read and write distance in an open environment can reach 100 meters.
Load the casing on the truck and attach the label. A worker holds a handheld PDA in the area around the truck with an Identec card reader inserted into the PDA to read tags. The reader can successfully read the tags 100% of the time, and tests have proven that the reading distance is around 10 feet. According to Identec, their active RFID technology is most suitable for this application environment. “Our long-range active RFID products are primarily designed for this application, and the test results of the tags themselves bear this out,” said Allen of Identec. “One of our customers has , 100,000 tags were used in a similar application environment.”
The test proved that the tag can be read in this environment, and the test successfully entered the second stage. At this stage, the fixed reader is first installed, and the truck loaded with the casing starts from the factory and passes through the area covered by the reader to copy the dispatch information.
During this testing phase, the RFID will be mounted on casings placed on trucks that will carry the casings through a test entrance on a steel pipe manufacturing facility. Once the test team finds the best way to measure read accuracy, they will Will be very satisfied with the test results. “The trial was so successful that we found a way to get the truck to settle down and record a 100% accurate reading rate,” Wood said. “The truck only had to stop a little and then it was ready to go. This process helped us record the readings we used during the test. To get the time, we need to collect more information than just the tag ID. As far as I remember, we also missed some tags in some trials, mainly because we didn’t stop the truck”
The testing team found that the best way to do this was to attach the tag to the sleeve. Mounting the tag inside the tube or welding a bracket under the tube can affect read rates. Instead, the label had to be placed on the flat surface of the tube. But if you want to get a better reading effect, you need to let the label hang on the casing at will. “The best read results are obtained when the label is not attached to the sleeve,” says Wadephu. “Poke a hole in the label and we can use a plastic tie or string to make the label wiggle in the air.”
Damage to the label during shipping is also an issue, given the size and weight of the item to be shipped. In this test, for example, the sleeves were labeled after they were placed in the truck, so this is an issue that still needs to be considered. Trial organizers weren’t very concerned about this, Wood said. “The label is strong, and I believe there is always some way to protect the label, so it’s not a big deal.”
The first two phases of testing have shown that RFID can be used in these environments, and the question now is how much benefit this technology will bring to the construction industry, and how much will it cost to implement.
The third phase of testing: tentatively scheduled for early next year – will expand the trial to install labels on many of the casings, as well as on the trucks that transport those casings out of the production plant. “We’re planning to prepare three or four trucks with casings to pass through the plant entrance, each with a different loading configuration, with a different casing, to get a 100 percent read rate in all cases,” Wadephul said.
Testing at this stage will help companies understand how much data can be stored in the tags. So far, each label has stored the same data, the information Shaw currently uses, stored in standard barcode labels. This information includes item number, user number, and a unique number for each casing.
Wadephul said: “The memory of the tag is getting bigger and bigger and can store more and more information, but we can see that too much data will delay the reading time, so we are trying to reduce the data stored in the tag, as much as possible. Store data in a central database”
If the third phase of the test is still going well, it also confirms that RFID is indeed a technology that can be applied to the construction industry, and the application of RFID technology to the construction industry still faces very serious business difficulties, as Wood said ” The construction industry has a long history, and it is very difficult to set a standard uniformly, and from the application of other technologies in this industry, the same standard problem does arise.”
According to Fluor, in order to make the mass use of RFID tags possible in production plants, uniform standards are very important.
Wadephul said, “If there are many builders who decide to use different tags, there will be protocol issues in the production plant, and the production plant will install different readers for different users. If different users use different readers, the cost will increase dramatically. At the same time any RFID implementation will be very complex, perhaps inhibiting all implementation plans. Budgeting each RFID project on a project-by-project basis is another issue. “Construction is a very cost-sensitive industry, Often guided by the project, the project bidder with the lowest bid often wins the bid.”
More and more industries are beginning to embrace RFID technology, however, spreading the additional costs to contractors will reduce the cost of RFID to some extent. Fluor said that if RFID technology is used, it can save time and cost of construction work, and customers will increasingly require RFID products in projects.
Wadephu said, “To strengthen the implementation of RFID products, we need a push from our customers. If our oil, gas and chemical users’ plants find that RFID can really bring them a lot of benefits, they will actively ask us to use this kind of Technology” Another work we have to do is to estimate the cost savings that can be achieved by applying RFID technology.
“But we know that if you put the raw material in front of a worker, he can work faster,” he says. Regardless of who uses RFID technology, Fiatech and Fluor agree that the cost of RFID cannot be ignored.
Wadephul said “I am concerned about the cost of active tags, although the price is falling now, all the suppliers I have talked to so far tell me that each tag is more than $50.” He continues, of course, there are ways to offset the cost. Batteries with active tags can last up to 10 years, so Fluor is looking to recycle these tags and use them in a variety of projects, “Because the duration of the project is 1-2 years, we can use one tag at the same time for 5 projects,” Wadephul said.
This recycling can help generate new business. For example, manufacturing plants and material suppliers can install labels on their merchandise and then charge an additional fee until the labels are returned by the project manager when the project no longer needs them. But this will only be possible after the introduction of RFID standards in the construction industry.
According to Wadephul, “to develop a uniform RFID standard across the construction industry, tags can be installed in production plants, and builders can pay and rent tags throughout the project.”
Although the performance of active tags has successfully passed the test, Fiatech and Fluor say that passive tags are less expensive than active tags if the performance of passive tags can be the same, or better than that of active tags. more, will replace active tags. But there are currently no plans to conduct similar tests on passive RFID tags.
Wood said Fiatech plans to send his members a research report on the RFID test at the upcoming conference in Houston in February. Fluor hopes that the large-scale demonstration of the results of this trial will generate great interest in the application of this technology to the entire construction industry and pay more attention.
[ad_2]