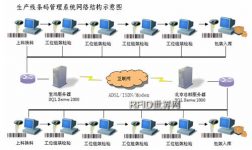
Schneider Electric realizes factory automation with Jingcheng MES “lean production, agile manufacturing” solution
[ad_1]
I. Overview
Schneider Electric is the only company in the world dedicated to power and automation technology, in power distribution, terminal distribution solutions, secure power, building automation and security, industrial control, PLC, sensors, drives and other automation professional projects. Global leadership.
With the gradual expansion of the company’s scale and the diversification of its product structure, the company has long foreseen the importance of informatization construction to enterprise management. Signed a contract to jointly implement the SAP ERP management system.
The implementation of the SAP ERP management system has established a complete set of information management platform for the company from raw material procurement, warehousing, material picking and returning, production management to sales, inventory and financial accounting. Effective control of accounting and other links has established a complete set of information logistics management platform that conforms to the actual management mode of the group company.
However, after the understanding and practical application of the ERP logistics system in the past few years, it is found that although the ERP logistics system has improved a lot of efficiency in materials, warehouses and finance, the SSBEA product line and the SBMV product line are in the execution of production tasks and the progress management of work-in-progress. , product quality traceability, after-sales service tracking and other links still have not played a good role in supervision and control, especially the large amount of data input in the production line, which takes time and is prone to errors, and the data cannot be updated in time, which brings a lot of inconvenience to production management.
Therefore, based on the collection of production line data and the tracking and tracing of product quality, the company also needs a highly refined and intelligent manufacturing execution system (MES) to control the entire production process, so as to make the enterprise flexible in production and management. Direction development, improve the real-time and flexibility of market response, reduce defective product rate, improve the operation efficiency of production line, strengthen production site data collection and work-in-process management, product quality and after-sales service capabilities, reduce production costs, etc.
With years of experience in the development and implementation of MES barcode system, professional consulting and software implementation service team, Beijing Jingcheng Software Co., Ltd. has reached a strategic partnership with Schneider Electric, which is another typical case of Jingcheng MES software in the electrical and electronic industry.
2. Demand analysis
Schneider Electric’s current actual needs in MES barcode software are as follows:
1. According to the actual workstation settings in the workshops of Beijing and Baoji factories, it is urgent to realize the basics such as feeding, changing batches, replenishing materials, production process (technical process) control, production data collection, quality management and barcode traceability of various raw material parts. It can realize the process control of the product production process and the data collection and quality traceability of the whole life cycle.
2. Through the MES barcode system, collect the production process data of key processes and workstations (5 in Beijing and 7 in Baoji), record the production process data, count the productivity and efficiency of employees, equipment and production lines, and analyze the product production process. Process defects in the process, easy to adjust in time.
3. Through the distributed network structure design, the timing data synchronization between Baoji and Beijing factories is realized, which is convenient for the centralized management and control of the headquarters, and the internal employees of the company can know the production progress and quality status of the factories and workshops in real time.
4. Through packaging barcode scanning, establish the relationship between packaging and products, complete outbound scanning and after-sales service traceability, and associate all raw materials, parts, suppliers, customers, production through any barcode information on the packaging or the product itself Process, quality inspection and other key information.
5. Establish a product after-sales service tracking system, recall and repair products with quality problems, record maintenance information, generate various after-sales service reports, and automatically query products with quality defects through barcode traceability.
6. Establish a data interface with the SAP ERP system, realize the unified maintenance and operation of various basic data (material information, personnel information, process data, etc.), reduce enterprise information islands, and realize the collaboration between MES production execution system and SAP ERP system Work.
3. Implementation plan
In line with the overall progress of Schneider’s informatization construction and ERP project, the implementation of the MES system must follow the principles of overall planning and step-by-step implementation. After discussion, we believe that this MES system can be divided into two phases to be completed respectively. The first phase of the project is defined as The two production workshops in Beijing and Baoji are implemented, focusing on completing the production, processing and assembly management of raw materials, semi-finished products, parts, and finished products, enabling basic data collection and quality traceability. The second phase of the project can be based on the first phase of the project. The management system is optimized and promoted in other related factories and workshops, and finally the whole process of barcode tracking management of the group company is realized. The first phase of the project must implement the data interface of the SAP system, and the interface is reserved for the second phase of the group company’s barcode management. The company’s overall informatization construction has laid a solid foundation.
The first phase of the project focuses on completing the following basic functions: (discussion)
System management, basic data definition, process and process route, production task and dispatch, picking and returning materials, production execution (material loading, assembly, testing, inspection, packaging, etc.), progress and on-the-job inquiry, quality management, barcode traceability , Comprehensive reports, ERP system interface, etc.
The second phase of the project completes the barcode management in the entire factory. Combined with the foundation of the first phase of the project, a complete set of enterprise resource management systems such as procurement, sales, production, receiving and returning materials, barcode traceability, supplier evaluation, and customer analysis can be realized. Comprehensive collaborative work.
The implementation of the EAS-MES barcode traceability system forms an integrated barcode for the enterprise from raw material procurement to inspection and storage, from production picking to production control of assembly, debugging, maintenance and packaging, and from finished product storage to sales and delivery. Track, realize the life cycle control and management of products, and seamlessly connect with the existing ERP system, and finally achieve comprehensive integration and collaborative production.
4. System structure
EAS-MES production execution system, as the execution layer between ERP enterprise resource management system and CRM/MRP/DRP and other management information systems, is mainly responsible for production management and scheduling execution.
EAS-MES enhances manufacturing competitiveness by controlling all factory resources including materials, equipment, personnel, process instructions and facilities, providing a method to systematically integrate functions such as quality control, document management, production scheduling, etc. on a unified platform In this way, the integration of real-time EPR/MES/process control system is realized, which forms a bridge for information exchange, enabling enterprise managers to grasp production information in real time and make production decisions.
The system adopts C/S (Client/Server) structure design, Microsoft SQL Server 2000 database, and the network topology is as follows:
After adopting the production line barcode technology, the order number, part type, and product quantity number are first formed into barcodes, and the barcodes are printed and pasted on the production line of product parts and assemblies. In this way, it is very convenient to obtain the production process of the product order on a certain production line and the required materials and parts.
After the product is completed on the production line, the production line quality inspector will scan the product barcode and production line code number after passing the inspection, and scan the worker’s barcode in the sequence of the process (it can be determined once and unchanged). For unqualified products sent for repair, the cause of the failure (process location) will be determined by the repair.
After the packaging process is finally completed, it enters the warehousing link of finished products, and then completes the sales, forming an overall process association.
Jingcheng EAS-MES manufacturing execution system is based on a large number of network hardware equipment and barcode scanning equipment. The normal operation of these equipment ensures the stability of the system and is the premise for the safe, efficient and stable operation of the production workshop management system, including:
1. Server: HP/IBM server: Zhiqiang 2.4×2/1G/72G×2/Gigabit network card or above
2. Wireless mobile collector: (CASIO DT300/DT900) used for logistics inbound and outbound links
3. Wired scanner gun in workshop: (SYMBOL-LS2208) for data collection of production line
4. Barcode printing equipment: (TSC-TTP243/Toshiba B-SX4T)
5. LED workshop kanban: (LED monochrome workshop display)
6. Station display: (9821SP LED industrial production line Chinese character liquid crystal display terminal)
7. Barcode label paper and related consumables, etc.
5. System function
Jingcheng EAS-MES manufacturing execution system complies with ISA-SP95 international standard and is designed in combination with China’s localized application requirements, providing resource management, production scheduling, data acquisition, process control, dynamic analysis, operation guidance, product traceability, dynamic inventory management, Quality management, quality early warning, automatic reporting and other functions can reflect production progress, man-machine efficiency, inspection results, and delivery status in real time, ensuring order receipt, orderly production, quality control, and strong traceability.
1. Production scheduling: Generate detailed production tasks according to monthly or daily production plans, and use large scheduling, weekly scheduling, and daily scheduling to assign tasks to production units (such as: workshop, assembly line, laboratory, team) , and control the daily capacity load status.
2. Task allocation: According to the production schedule, tasks are allocated and monitored for equipment, types of work, workstations, processes, and procedures. Production instructions can be allocated by the hour, and the implementation of monitoring tasks is collected and monitored according to production process data.
3. Plan execution: According to the allocation result of the production instruction unit, the authority is controlled, and the system automatically prompts its operation instructions, cooperating personnel, quality inspection personnel, equipment, tools, materials, accessories and other operation guidance information.
4. Process management: Define product BOM structure and operating procedures, process flow, key control points, quality standards and related process requirements, and form a complete product process database for version control, process optimization and process improvement.
5. Resource management: unified management of personnel information, material information, equipment information, auxiliary material tools and other information related to production resources in the production process, to achieve personnel performance appraisal, material procurement, storage, picking, returning, uploading The management of basic resource information such as materials, dynamic inventory, cost analysis, etc., is convenient for the effective tracking of various resources in the later stage.
6. Material management: material management for the whole process of purchasing, stockpiling, preparing, picking, loading, changing, returning, replenishing, and finished product stocking, selling and stocking out of the raw material workshop. Check and record the products and scraps, provide the location and status of specific materials in real time, and record the actual consumption and loss rate in real time.
7. Production and assembly: The corresponding parts assembly and key data collection are completed according to each operating station. The system automatically completes the correspondence between finished product barcodes and material batches, key condition barcodes and collected data based on the BOM list, and automatically checks the actual operators. The correctness of quality inspectors, procedures, materials, equipment and tools to achieve the traceability of assembly process data.
8. Quality inspection: Through the real-time collection of on-site information, the determination of quality problems, the causes, and the scope of the impact can be quickly and accurately located, and the traceability and analysis of product hidden dangers can be realized. The stability of the process, product yield, and distribution of defective defects Real-time monitoring and early warning of the fluctuation of the production line, and effective prevention and provision of problems on the production line.
9. Data collection: generate or read barcodes at the source according to barcode rules, and can use wired, wireless, RFID, magnetic cards and other methods to complete the collection, and quickly obtain information such as personnel, materials, production processes, products, processes, inspections, etc. The manual keyboard and hardware interface can be used to realize the automatic collection of equipment data such as automatic scanning equipment and sensors.
10. Early warning reminder: According to statistical principles and special quality assurance principles, advance warning is implemented, and automatic warning is given for equipment, processes, personnel, materials, quality standards and other data that may have potential quality problems. It can effectively prevent the wrong installation, missing installation and multi-installation of spare parts.
11. Kanban management: at the processing, assembly, and inspection site, according to the actual production process and progress, display the current process information and completion information, including process regulations, work-in-progress information, material information, completion information and quality information, etc., prompting operation and collaboration , inspection and handover information, and can provide the completion of the entire process of the current product.
12. Packaging and warehousing: Provide automatic generation of packaging barcodes according to a certain number of packaging, automatically correspond to products and packaging, prevent leakage and wrong packaging, and automatically print packaging labels and packing lists.
13. Maintenance management: Products with quality problems in the production process and after-sales can automatically record maintenance details, quantities, reasons for failure, replacement of replacement barcodes, maintenance accounting and maintenance historical data statistics through maintenance management, so as to realize the production and after-sales service process. Trace back to the root cause of quality problems, and implement quality management throughout the entire life cycle of the product.
14. Traceability management: According to the quality defects of the material batch, all finished products using the batch of materials can be traced, and the reverse tracking from finished products to raw materials can also be supported to adapt to the recall system of certain industries and help manufacturers reduce losses. Minimize, better serve customers.
15. Statistical analysis: Through a series of later work such as mathematical statistics, mathematical analysis, and data mining, the analysis data required by the enterprise is derived, and various quality reports, charts and reports such as Plato, histogram, and Xbar graph are automatically generated, and fed back to the Online system performance analysis and improvement.
16. Decision support: Numerous reasonably designed and optimized reports provide managers with quick statistical analysis and decision support, and grasp every link in production in real time. The comprehensive report shows the first-hand process data of the production site in real time, and summarizes and analyzes the real-time output of the production line, the output rate of the process, the operation status of equipment and personnel, and provides an effective tool for the improvement and improvement of production execution status and product quality. Evaluation basis.
17. Data interface: This system can realize seamless integration with mainstream ERP systems such as SAP, ORACLE, UFIDA, Jindie, etc. It can also provide secondary development according to user needs to meet the needs of personalized management of growing enterprises.
18. System permissions: system user management, permission management, log management, system settings, announcements and notifications, online short messages, data backup and recovery, password modification, ERP interface, LED interface and other functional modules.
6. Implementation Benefit
Through the MES execution system developed by Jingcheng Software Company, combined with the application of barcode technology in the management process, the company’s management of inventory commodities, semi-finished products, and original materials has been solved. On the one hand, commodity barcodes will run through the entire logistics process. Search and trace in the system at any time. On the other hand, the system can strengthen the on-site management system, standardize business processes, improve everyone’s overall collaboration ability, improve efficiency and accuracy, and provide a basis for later data query analysis and headquarters data docking data sources;
Through the integration with the ERP system, the MES system completes the assignment of workshop tasks, and at the same time conducts management and control at the level of workshop production operations, making up for the weakness that the ERP system cannot manage and schedule in the field of production and manufacturing. It meets the requirements of enterprises for production timeliness, quality reliability and traceability, more detailed cost control, and better material control.
The successful implementation of the system has injected new vitality into Schneider Electric’s informatization. At the same time, the effective integration with the ERP system will greatly improve the effective coordination of Schneider Electric’s procurement, inventory, production, sales and financial management. A unified and integrated manufacturing management platform has brought the information construction of Schneider Electric Group to a higher level.
[ad_2]