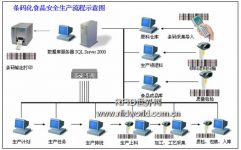
Dongfang Haowei Food Co., Ltd. adopts the sincere bar code food production and sales integrated business system to achieve high-quality production and sales management
[ad_1]
I. Overview
Beijing Dongfanghaowei Food Co., Ltd. was established in the early 1990s. It is a private joint-stock enterprise specializing in food production. It mainly produces and sells jelly, candy and other foods. The products cover the whole country; the annual turnover reaches 100 million yuan. With the gradual expansion of the company’s scale and the transformation of the production and operation model, the company urgently needs to establish a rigorous and safe food production management system, including planning management, procurement management, task management, process Process management, quality management and nationwide distributor and store management, so as to achieve one-stop, quality and systematic management from production to sales.
With years of rich experience in the development and implementation of management systems in production, commerce, and other industries, as well as professional consulting and software implementation service teams, Beijing Jingcheng Software Co., Ltd. stands out among many competitors and formally signed a strategic cooperation agreement with Dongfang Haowei Group for joint implementation. An enterprise integrated business management system based on Dongfang Haowei’s production and operation model.
2. Demand analysis
The actual needs of Oriental OmniVision in terms of business systems are as follows:
1. Establish a complete group management platform to realize the company’s basic business such as safety production, logistics and distribution, platform wholesale, store sales and post-account finance, cost analysis, comprehensive reports and intelligent decision-making. The centralized management of members, specialty stores, personnel, etc., organically coordinates the procurement, sales, logistics, finance, warehouse, personnel and other departments of the enterprise, and realizes a comprehensive management platform that runs through the core of the company’s overall business.
2. Warehousing personnel can complete daily raw material storage, finished product delivery, inventory, adjustment and drawing, production loading and other work through barcode scanning equipment; production department personnel can use barcode scanning equipment to automatically check the production process, working hours, production data and packaging batches. It is convenient for the company to control the production progress and substandard products in real time, and lay the foundation for worrying about the production process and safety traceability in the future.
3. The personnel of the quality inspection department can automatically record the inspection results through the barcode scanning equipment, automatically carry out early warning and statistics on the products that do not meet the standards, and provide the leaders of the production department with statistical reports on the products that do not meet the standards in real time. The system can automatically trace out the specific supplier, inspection, processing personnel and other information of this batch of products according to the batch that does not meet the standard.
4. The system can automatically generate task sorting lists according to production plans or customer orders, and worry about production tasks according to urgency.
5. Increase the management of gifts, gifts and promotional items, and support the packaging, disassembly and assembly operations of various commodities and gifts.
6. Local specialty stores can realize online orders, inventory inquiry, member management, POS sales, and collection management through the Internet, forming an advanced management model for unified management across the country.
7. Company leaders and system administrators have the highest authority, and can inquire about all data generated by production and sales, and can provide accurate basis for leadership decision-making through a large amount of data analysis.
8. Reserve the data interface of UF financial system, so as to realize the seamless connection of data in the future, and realize the collaborative operation of business system and financial system.
3. Implementation plan
In line with the informatization construction of Dongfanghaowei Company and the overall progress of the project, the implementation of the system follows the principle of overall planning and step-by-step implementation. After discussion, we divide the system into two phases to complete respectively. The first phase is defined as barcode food safety production. The system can promote the production efficiency of the production department and improve the company’s product quality. On the basis of the first-phase project of the second phase of the project, the group platform sales management of the national chain operating companies and stores is realized.
The first phase of the project focuses on completing the following basic functions:
System management, basic data definition, raw material procurement, production planning, production tasks and scheduling, material collection and return, production process, quality standards, packaging, finished product storage, progress and on-the-job query, quality management, statistical reports and leadership decision support modules, etc.
The second phase of the project completes the group’s platform-based sales management. Combined with the foundation of the first phase of the project, the improvement and evaluation of supplier, distributor, store and customer information can be achieved, and the food sales system can be processed and standardized, including post-accounting. A complete set of integrated management system for group production and sales such as financial data and UF interface.
The implementation of the system will form an integrated management from raw material procurement to quality inspection and storage, from production picking to finished product packaging, from finished product storage to sales and out-of-stock, from company out-of-stock to door-to-door sales. The management effect of the two-handed management of benefits, and the seamless connection with the existing UF financial system, finally realizes the collaborative work between the various systems of the company.
4. System structure
The system adopts C/S+B/S structure design, Microsoft SQL Server 2000 database, and the network topology is as follows:
Production process diagram
Organizational Topology
The system is based on a large number of network hardware devices and barcode scanning devices. The normal operation of these devices ensures the stability of the system and is the premise for the safe, efficient and stable operation of the production workshop management system, including:
1. Server: HP/IBM server: Zhiqiang 2.4×2/1G/72G×2/Gigabit network card or above
2. Wireless mobile collector: (CASIO DT300/DT900) used for logistics inbound and outbound links
3. Wired scanner gun in workshop: (SYMBOL-LS2208) for data collection of production line
4. Barcode printing equipment: (TSC-TTP243/Toshiba B-SX4T)
5. LED workshop kanban: (LED monochrome workshop display)
6. Station display: (9821SP LED industrial production line Chinese character liquid crystal display terminal)
7. Barcode label paper and related consumables, etc.
5. System function
1. Production planning and tasks: Generate detailed production planning sheets according to sales status or customer orders, and implement task assignment and monitoring for equipment, types of work, workstations, processes, and procedures according to production scheduling plans. Production instructions can be dispatched hourly, and Collect and monitor the execution of tasks based on production process data.
2. Task scheduling: According to the production instructions, the production scheduling is carried out, and the authority is controlled, and the system automatically prompts its operation instructions, cooperating personnel, quality inspection personnel, equipment, tools, materials, accessories and other operation guidance information.
3. Production feeding: According to the production task and material report form, the production picking and feeding are carried out to the warehouse.
4. Process management: Define different processing procedures, technological processes, key control points, quality standards and related process requirements for different foods, and form a complete food process database, which is convenient for version control, process optimization and process improvement.
5. Quality inspection and safety traceability: Through the real-time collection of on-site information, the determination, cause and scope of quality problems can be quickly and accurately located, and the traceability and analysis of product hidden dangers can be realized, and the problems on the production line can be effectively prevented and provided. .
6. Kanban management: at the processing quality inspection site, according to the actual production process and progress, display the current process information and completion information, including process regulations, food in process information, raw material information, completion information and quality information, etc., prompting operation, collaboration, Inspection and handover information, and can provide the current completion of the entire food process.
7. Packaging and warehousing: Provide automatic generation of packaging barcodes according to a certain number of packaging, automatically correspond to products and packaging, prevent leakage and wrong packaging, and automatically print packaging labels and packing lists.
8. Procurement management: realize the procurement management of raw materials, semi-finished products, packaging and other items of suppliers or external processing manufacturers, including procurement plans, purchase orders, purchase billing, purchase storage, purchase payment and other functions.
9. Inventory management: Realize the processing of raw materials, semi-finished products, packaging, and finished products in and out of storage, inventory, and adjustment.Including inbound order, production issue order, sales issue order, inventory order, transfer order, loss report and overflow order, inventory statistics table, etc.
10. Sales management of the head office: realize the multi-level distribution management of the company to the dealers, mainly including: price system management, reputation management, logistics and distribution management, etc.
11. Dealer and store sales management: Realize dealer’s sales management to end customers, including retail, price, promotion, collection management, etc.
12. Accounting management: The actual accounting data will be summarized and counted, so that the leaders can timely understand the business status of the enterprise and the data of receivables and payables, and can set the accounting warning prompts to avoid the phenomenon of dead and bad debts.
13. Statistical analysis and leadership decision-making: Through a series of later work such as mathematical statistics, mathematical analysis, and data mining, the analytical data required by the enterprise is derived, and various production reports and sales reports such as Plato, histogram, and Xbar chart are automatically generated. And feedback to the online system for performance analysis and improvement. Reasonably designed and optimized reports provide managers with quick statistical analysis and decision support,
14. Basic data: including information on suppliers, distributors, stores, departments, personnel, etc.; including basic information on raw materials, semi-finished products, finished products, and production processes, processes, etc., which can be directly imported through the original software or forms.
15. System management: It mainly includes data backup and recovery, user, password management, operation authority assignment, operation log and data interface functions.
6. Implementation Benefit
1. Build a transparent production platform for suppliers, production departments, raw materials, and processing personnel; build a tree-like networked sales platform between companies, dealers, and stores; 2. Realize production according to plan, sales, and order mode to reduce inventory pressure
3. Real-time grasp of the production workshop and food-in-process production situation, improve the management and control of in-process products in the production workshop, speed up the progress of product production, and improve the production efficiency of the workshop
4. Eliminate the manual data entry and data statistics work of the original warehousing and other departments, and change it to automatic collection of barcode equipment, reduce a lot of manual repetitive work, avoid human errors, and reduce the work intensity of personnel.
5. Realize the monitoring of the whole process of food production. Once a problem occurs, the cause of the quality can be accurately traced. If there is a raw material problem, it can be traced directly to the supplier of this batch of raw materials. Unnecessary financial compensation disputes
6. Provide a basis for effective assessment and scientific early warning of potential food safety hazards based on market feedback data.
7. Standardize the processing process in the production process and lay the foundation for quality production; standardize the business process in the sales process and improve the overall efficiency of business operations;
8. Achieve seamless platform-based and efficient integration between the company’s existing systems, such as UFIDA Finance, OA, etc.
[ad_2]