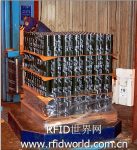
Tubing manufacturer uses RFID system to track production process and ensure material accuracy
[ad_1]
Tejas Tubular Products, a company specializing in oil tubing and other products and services for the petroleum industry, now uses RFID technology to track production processes, ensure product quality and improve production efficiency in product manufacturing.
The system, implemented by Ship2Save, went live last month at the company’s Houston facility. The system includes 915 MHz EPC Class 1 Gen 2 passive RFID tags, readers and Ship2Save’s operations management middleware. The middleware is used to manage the RFID hardware and share data with Tejas Tubular Products’ end systems, such as material requirements planning systems (MRP).
Tubing and other products wrapped in shrink plastic
“In this industry, product traceability is very important,” said Maximo Tejeda, president of Tejas Tubular Products. According to U.S. Petroleum Agency regulations, every product a company makes must be certified, which requires manufacturers to have a manufacturing history for every product they make. This record must be traceable to the specific heat index of a batch of steel used in the manufacture of the product.
“In the process of completing an order, we had to track every step of the entire production process to make sure that different batches of plates were not mixed up,” Tejeda explained. “There are different grades of plates. For different depths of wells You don’t want a product designed for a 6,000-foot well that ends up in an 18,000-foot well.”
RFID systems track production processes, ensure product quality and improve production efficiency in product manufacturing
To track the production process, workers place each paper order in a plastic interlayer, and paste the RFID-tagged orders on pallets loaded with steel plates used to manufacture the ordered products. The labels have unique ID numbers that correspond to the machining instructions required to complete the order in Tejas Tubular Products’ MRP system. When the pallet carrying steel plates flows through the production process, the RFID reader reads the tag to obtain instructions, which workers can see on the mobile smart mobile terminal. “This ensures that the products are processed in the correct order,” says Ship2Save director Konrad Konarski.
Workers can see production instructions on mobile smart mobile terminals
An order may list 10,000 couplings and dozens of tubing, and depending on the order volume, more than one pallet of steel may be used in the manufacture of the product. When the product is manufactured, the RFID tag on the work order can be programmed with information that the product is manufactured. In addition, the label contains heat index, product size and steel grade and other relevant information obtained from the MRP system.
“The whole idea of the system is to make sure the order is done accurately and we don’t want to send the wrong item. We read the label again and reconfirm the order before shipping,” Tejada said.
“We hope that customers can also adopt RFID technology and use a reader to automate the confirmation process when an ordered item is received, reducing human error,” Tejada said.
In addition, the automated system saves a lot of time because staff can avoid handwriting information. Salespeople can also get real-time production data through a large screen installed in the office. “The most important thing is that we provide our customers with the best service we can do, improving our efficiency and product tracking,” Tejada said.
To date, Tejas Tubular Products has ordered 5,000 tags, installed 2 fixed XR440 RFID readers and 4 handheld MC9090-G RFID smart mobile terminals. Tejeda said if the system were used in three other manufacturing plants, the company could use 10,000 tags a month.
[ad_2]