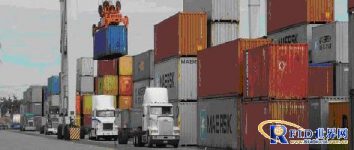
Application case of active RFID system in Georgia Port, USA
[ad_1]
The Port of Georgia is the fourth largest container port in the United States, with an annual throughput of more than 2.6 million TEUs.
The application of the system in the Port of Georgia, USA is mainly to achieve the following functions:
1) Accurately identify and verify whether the container and the truck chassis passing through the gate are compatible;
2) Locate and find containers and other equipment on the yard;
3) Use radio frequency identification (RFID) to track trucks passing through the gate and moving on the dock;
4) Wireless local area network for data transmission;
The deployment practice has proved that the system fully meets the following design requirements:
1) Greatly improve the truck traffic, capacity and service level of the gate per unit time;
2) Reduce the total idle time of trucks at the dock, improve production efficiency and customer service quality;
3) Obtained highly accurate quantitative statistics of truck traffic and other mobile equipment in the port;
4) Improve the speed and accuracy of data acquisition and processing;
The system obtains data without human intervention at the following nodes:
1) The flow of trucks entering and leaving the gate;
2) Exchange containers between cranes and trucks;
3) Mobile container handling equipment and vehicles exchange containers;
The system uses the following three main components:
1) Active 915 MHz read-write RFID tag, the tag has a unique identification number, installed on the rear bumper of the vehicle;
2) RFID readers with a reading radius of 100 meters deployed at gates, docks and mobile container handling equipment are used to scan and obtain data from tags on trucks;
3) The position markers on the driveway near the gate and on the crane bracket provide the precise position of the truck with the label;
The location marker can accurately know which lane the truck is driving on and the direction of the truck without using a more expensive real-time positioning system. The reading or writing of data at all data exchange points (checkpoints, gates, weighing stations) is completed by the RFID system, no manual input and output are required, which reduces the number of on-site personnel, thereby ensuring personnel safety and reducing The workload of personnel has also improved the speed and work efficiency of vehicles passing through various gates, and greatly reduced the queuing and congestion at the gates.
On the dock yard, when the truck stops at the feet of the crane, the position marker on the crane leg will write the current position and time information into the tag memory on the container, and this information will be sent to the nearby reader via the tag. The reader can query the database through the data center to get the current work order, such as unloading or loading, and send it to the crane operator. If it is unloading, the location of the container will be stored in the system for easy searching when picking up or transferring. The location, number, identification number, time information and loading and unloading requirements of the container are notified to the system and the crane driver through the interaction of tags and readers. All work does not require manual intervention, avoiding the use of walkie-talkies on the dock to instruct the crane driver to communicate, which guarantees The safety of the staff also provides productivity. The crane driver does not need to visually recognize the container number 20-30 meters below to confirm that the container he lifted is correct. When using a forklift to load and unload containers, the reader installed on the forklift can read the identification number of the container tag and update the system database.
Application effect
1) Wrong transactions at the gate are reduced from 10% to less than 3%;
2) The average turnaround time of trucks dispatched each time has dropped by 10-11%;
3) Reduce or eliminate the queuing flow of trucks outside the gate;
4) Create a real-time and measurable data stream for the movement of trucks passing through the terminal;
5) There is no need to arrange staff at the gate and container yard;
6) Provides more efficient working conditions for crane drivers.
[ad_2]