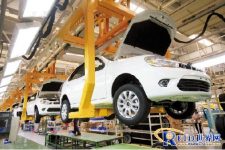
Application of RFID technology in automobile industry
[ad_1]
As the development of the Internet of Things is raised to the national strategic level, and the in-depth promotion of major national informatization projects,RFIDAs a perfect combination of wireless communication and automatic identification technology, it has broad application prospects in industries such as production, logistics, transportation, and public management. In manufacturing companies, RFID has been applied to logistics tracking, real-time monitoring of production data, quality traceability, automated production, warehouse management, asset management and other links. In the monitoring and management of the automobile manufacturing process of Haima Car Co., Ltd., RFID mainly uses its fast, accurate, and real-time data collection characteristics, and is mainly used in the automatic identification and tracking system of the body of the paint shop and the WBS of the body storage area of the welding shop. In the body scheduling management system of PBS and the body storage area of the assembly shop, through the scientific application of RFID, the company’s automobile manufacturing technology and craftsmanship are improved.
1 Application of RFID in painting
RFID is mainly used in AVI (Automatic Vehicle Identification) in the paint shop of our company.
1.1 Overview of car body recognition system in paint shop
The paint shop car body identification system (AVI) adopts RFID radio frequency identification and bar code recognition technology. The main purpose is to provide basic body data and control routing information for the workshop machine movement system.
1.2 Architecture diagram of AVI system
1.3 Main functions of AVI system:
Provide body information and routing information for the workshop machine control system;
The operation of the AVI system can be monitored through the screen of the AVI central control system; the man-machine interface configured by the AVI system can monitor and modify the car body information;
Record the basic car body data and routing information of each AVI site and form a report. Provide color separation routing function for color separation storage area. Provide car body color and model information to the robot spraying system.
1.4 AVI system composition
The AVI system is a Server/Client architecture. The hardware of the whole system includes the following main components, mainly including 10 RFID read-write antennas, 4 automatic barcode scanners, 4 AVI operator stations, 4 VersaView touch screens, 6 sets of machine system PLC, 1 AVI server And 1 AVI client.
The software system includes Windows Server 2003, SQL Server 2003, CIMPLICITY HMI and RSLinx, etc.
The AVI system communicates with AB ControlLogix L61/L62 PLC. RFID antenna, barcode scanner, and AVI operator station communicate through the Fieldbus DeviceNet; each area PLC, operator station touch screen, AVI server, and AVI client communicate with each other. Communication via Ethernet.
1 AVI server
The main function of the AVI server is to collect vehicle body information and alarms of the AVI site from the machine PLC through the Ethernet, and establish an AVI monitoring system database; these data will be processed and calculated in the background and sent to the client screen.
AVI system server adopts IBM X3650-7979-R05 rack-mounted server, quad-core Xeon X5420/2G memory, and 2X146G hard disk mirroring hard disk.
Data server
The AVI system shares a database server with the PMC system and the ANDON system to realize the storage of historical data, the management of the database, the recording of historical data, and the query of historical reports. SQL data server adopts IBM X3650-7979-R05 rack-mounted server, quad-core Xeon X5420/2G memory, and 2X146G hard disk mirroring hard disk.
AVI client
Real-time monitoring, graphical display of the configuration and operation of the AVI system; system alarm entry and viewing of alarm history records; vehicle information records at each AVI site in the paint shop.
The AVI system client uses a Dell computer, PIV/3.0G/512M memory/160G/50DVD, and a 19-inch LCD monitor.
Read and write antenna station or RFID system
Read the current code carrier information on the skid body to obtain the body information.
The RFID system uses COBALT HF RFID products from Datalogic Automation, including Cobalt HF controllers, Cobalt HF antennas, HF high temperature tags and related accessories.
The COBALT HF RFID system provides an easy-to-integrate and economical solution for factory automatic identification applications by virtue of its sturdy housing and easy connection. The dust-proof and moisture-proof features of the system enable it to work continuously and stably in harsh environments.
The serial communication connection method uses DeviceNet™, which ensures the rapid integration of the DeviceNe network with AB’s PLC system.
The high-frequency 13.56 MHz controller supports multiple RFID air protocol standards, including ISO15693 and ISO14443A standards, and can be used in conjunction with many types of tags and suppliers’ products.
Passive UHF read/write tags do not require batteries and can provide up to 2KB of user-accessible memory. When the working temperature is as high as 200℃, the high-temperature product model can also ensure reliable and accurate data storage during use. For standard temperature applications, the durable ABS plastic package can ensure the integrity of the label even in harsh working environments.
Human Machine Interface HMI
The human-machine interface HMI provides AVI system human-machine interactive operation for on-site operators, and communicates with the PLC control system through the network. The main functions that can be realized through the man-machine interface include: body information display, operation monitoring, fault alarm prompt and fault maintenance, and manual data input.
The high temperature resistant code carrier is hung on the skid body and is mainly used to store the information of the car body loaded on the skid body.
Barcode Scanner
It is used to scan the barcode car body information on the car body and pass this information to the PLC, and the PLC writes this information into the carrier code.
Quality button box
In the quality inspection station, the operator selects routing information for the current car body by operating the quality button box. The AVI system controls the car body’s process path and performs car body diversion according to the routing information input by the operator.
1.5 RFID site
Installed at each key identification point in the workshop, as shown in the following table:
1.6 The working process of an RFID site of the AVI system
● The machine provides signals of car body in place;
● The automatic scanner scans the barcode number. If the scan is unsuccessful, the system will alarm for manual intervention and manual input; at the same time, the system will check the legality of the barcode number: if the scanned barcode information is illegal, the touch screen will display a reminder message and you need to scan it again or Enter the barcode information until the barcode information is correct;
● The system receives the scanned barcode number, and at the same time displays the current barcode number on the touch screen;
● The system will write the scanned correct information into the Tag. If there is a write error or failure, the system will give an alarm and prompt manual intervention;
● AVI module provides departure signal to the machine;
● The machine transportation system provides a signal that the car body has left;
● The system sends information to the upper system, the information includes: scanning point position number, scanning time, skid number, barcode number and remarks;
● The upper system will back up the above information to the local database system.
1.7 Barcode rules used by AVI
In order to facilitate the identification and transmission of body information within and between the production workshops, according to the actual situation of our company’s vehicle models and workshops, the total number of digits in the body barcode is stipulated to be 16 digits. The meaning of each representative is as follows:
Body barcode (16 digits): 0123456789ABCDEF
● Bit “0”: Represents which production line (or workshop) this car body comes from;
● Bit “123”: represents the car model;
● Bit “4”: represents the year;
● Bit “5”: represents the month;
● Bit “6789AB”: represents the production serial number;
● Bit “CD”: represents the color of the car body;
● Bit “E”: Represents which workshop the car body is to be sent to;
● Bit “F”: stands for check digit.
1.8 A few notes on the application of RFID paint shop
“It does not rely on manpower, but uses equipment including hardware and software to automatically read the information of RFID systems, barcodes, QR codes, fingerprints, voiceprints, iris and other information media and recognize their content. The technology is called automatic Identification. This system that reads and recognizes “people and things” is the so-called ID system (Identification System).
● In this system, RFID and barcode coexist perfectly
Using RFID alone in an automated process is not a problem, but coexisting with “visual barcodes” in a manufacturing process with human participation is the best way.
● RFID can improve the quality, can be traced, and can carry out information management, but it needs the favorable support of the upper configuration software.
● RFID technology has many obvious advantages, but its advantages are mainly based on information collection and information sharing.
2 Application of RFID in welding and assembly
The application of RFID in the company’s welding and final assembly is mainly used in the WBS storage area and PBS storage area of the two workshops, similar to the routing application of the color separation area before the paint shop.
2.1 Introduction to storage line function
The storage line is equipped with a sorting and inverting channel, which can be sorted out according to the production plan. The fast off-line channel is used to meet emergency production requirements, and the car body can be directly sent to the part point on the painting line. After the car body falls into the painting line, the empty spreader will return to the place where the upper part is welded, and the empty spreader can also be directly entered into the storage warehouse, so that when production is stopped on holidays, all the remaining empty spreaders can be stored in the warehouse. The empty spreader transferred from the body storage conveyor chain can also directly enter the upper part without entering the paint shop.
2.2 Warehouse area management function
WBS (or PBS) sets the vehicle type into the computer at the upload point. Under normal circumstances, the worker enters the current car body information into the computer, and transmits the information to the Siemens PLC through the industrial Ethernet, and the PLC transmits the information through the PROFIBUS DP bus. For the read-write head, the read-write head writes the information into the code carrier and saves it. The read-write head reads the information at the warehousing point, and transports the car body to the corresponding warehouse area according to the warehousing rules. The read-write head reads out the information at the exit point and outputs the corresponding car body according to the exit rules.
When the vehicle input computer or Ethernet fails or needs to be shut down for maintenance, in order not to affect the production, an operation box is set at the loading point. By selecting the DIP switch, the vehicle body information can be manually written into the PLC on the operation box, thereby Continue to complete automatic warehousing.
Set up HMI at the entry point and exit point to display the read-out car body information and the current exit and entry rules, which can be manually judged and modified.
3.3 Monitoring system
The on-site monitoring industrial computer uses the WINCC configuration software to make dynamic pictures and randomly monitor the operation of the main transfer stations and station storage sections of the friction line system. It is also used as a tool for machine repair and debugging. Various on-site control signals and actuators are connected to the PLC through the field bus module, and the PLC controls the actions of the whole line. The on-site monitoring industrial computer displays the process operation status of the friction line and the storage status of the car body in the form of screens (display storage by vehicle type) Quantity), display the working status of each station sensor and control element, the current status of each I/O signal will be displayed in table form. The relevant data can be modified through the host computer to keep the data of the entire system consistent with the actual situation in the library. According to the production plan, set the color, priority and prohibition order of the entry and exit of each storage line. According to the production plan, control the number of vehicles entering and leaving the painting area.
3.4 Difference from RFID in paint shop
● The functions are exactly the same, but the system is smaller.
● Choose different brands
RFID system adopts Pepperl+Fuchs products, communication bus adopts PROFIBUS DP bus, PLC adopts Siemens S7-300 product, and configuration software adopts Siemens WINCC configuration software.
3 How do companies choose and use RFID correctly
Although RFID technology has many advantages, RFID manufacturers are uneven, and companies have deviations in their understanding of RFID concepts. The application of RFID systems will inevitably enter some misunderstandings, and the sword will go lopsided. Therefore, choosing the RFID solution that best suits your business situation is the best way to go.
RFID tags are usually placed on materials, equipment, and objects that need to be collected. The reader recognizes the data on the tag, and the collection after recognition and real-time upload to the host computer software such as production management software, MES system, etc., need The company plans and deploys its own network system internally.
Companies need to understand the development trend of RFID systems. According to different application links, such as production management, employee management, warehousing management, and logistics management, they should choose different implementation plans accordingly to avoid blindly seeking good information systems and excessive hardware configuration. Excessive pursuit of internationally famous products and using sledgehammers has resulted in unnecessary high investment.
To implement an RFID system, an enterprise needs to follow the trend, but also to do what is appropriate.
4 Development Trend of RFID Application System
● High frequency of the system
UHF radio frequency identification system has the advantages of long identification distance, unforgeable, repeatable reading and writing, and compact size. UHF radio frequency identification system is more and more widely used.
● Networking of the system
Different applications need to centrally and uniformly process data from different systems, and networked data systems have become inevitable.
● High system compatibility
There are more and more manufacturers in the RFID field, and it has become a trend to achieve compatibility between their products and to be able to handle products from multiple manufacturers.
● Higher data volume requirements of the system
In the future, RFID systems will process a larger amount of data. Therefore, RFID systems need to have greater data storage capabilities and data processing capabilities.
[ad_2]