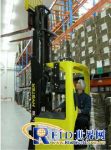
Biopharmaceutical company Novo Nordisk adopts Intermec mobile data collection terminal
[ad_1]
The world-renowned biopharmaceutical company Novo Nordisk uses Intermec mobile data collection terminals to make its warehouse management work faster, easier and more efficient. Novo Nordisk, headquartered in Copenhagen, Denmark, is a world-leading biopharmaceutical company with the widest range of diabetes treatment products in the industry. It has been the world leader in diabetes research and drug development for more than 80 years. And it is the world leader in many aspects such as hemostasis management, growth health hormone and hormone replacement therapy. Today, it has branches in nearly 70 countries around the world, with production plants in 6 countries, more than 21,000 employees, and sales in 180 countries.
Tianjin Novo Nordisk Pharmaceutical Factory is the production base of Danish Novo Nordisk in China. The factory covers an area of more than 5,000 square meters, including production workshops, normal temperature warehouses and low temperature warehouses. As Tianjin Novo Nordisk’s requirements for corporate management continue to increase, Tianjin Novo Nordisk Pharmaceutical Factory decided to implement the Prism ERP system and chose Intermec’s products to implement the operation. As a senior barcode system integrator, Xichuang Technology Co., Ltd. Provide overall barcode project solutions for Tianjin Novo Nordisk Pharmaceutical Factory.
Novo Nordisk has adopted Intermec’s wireless products, including: Intermec’s wireless access point WA21, wireless handheld terminal CK30, Intermec wireless vehicle terminal T2455, and Intermec1552 wireless scanner. By using Intermec products, the existing manual recording warehouse management is transformed into an integrated and efficient paperless warehouse management system.
The WA21 wireless access point provides wireless signal coverage to the entire factory. The T2455 vehicle-mounted terminal is installed on a forklift. The forklift is also equipped with a fixed scanner and a 1552 wireless scanner. The fixed scanner is used to scan the bar code of the warehouse and the 1552 wireless scanner is used. To scan the barcode of the goods on the pallet, all scanned data are input into the T2455 wireless vehicle terminal, and the T2455 transmits the collected data to the ERP system through the wireless network. The CK30 wireless handheld terminal has its own scanner, which can directly scan the bar code to obtain data and communicate with the ERP system wirelessly.
Use effect: improve the efficiency of location management
Tianjin Novo Nordisk’s warehouses all use high-level shelves. The density of shelves in the entire warehouse is very large, and the product value on each pallet is very high. Different types of products have very strict requirements on the storage temperature environment. Many high-value drugs must be stored in In the low temperature environment, the warehouse operations in the past mainly relied on manual records and form statistics to manage the goods in the warehouse. It often occurred that the products were sent to the wrong warehouse or sent to the wrong location. When the product needs to be extracted, the product could not be found or the wrong product was taken. The situation caused great losses. Because it is manual recording, in order to see the information of the items on the pallet, the forklift workers need to get on and off the forklift frequently during the operation.
After using Intermec’s T2455 wireless vehicle-mounted terminal, all warehousing operations can be completed on the forklift by a forklift worker, including bar code scanning for storage locations, bar code scanning for items on pallets, and T2455 keyboard input when necessary. Data, using the wireless network to submit the data to the ERP system in real time. Reduce the operation steps. Because the barcode is scanned to collect data, the accuracy of data collection is greatly improved. The real-time data of wireless network ensures the first-in-first-out of raw materials and products, which saves a lot of time, reduces labor, and improves work efficiency. .
It is worth noting that, based on the situation that Novo Nordisk’s warehouses are all high-level shelves, Xichuang has designed a set of linkage system so that the fixed barcode scanner can be linked with the position of the fork, even in the highest position. Forklift workers only need to press the scan button when the goods are fork-in/fork-out, and they can accurately and quickly scan the bar code of the bar code. System commands are scanned in one-to-one correspondence. Users appreciate this design.
Warehouse inventory is no longer restricted
Before realizing wireless data collection, Novo Nordisk’s warehouse managers needed to take a form to compare the inventory of the goods one by one when performing inventory operations, and then return to the office to enter the data into the computer for storage. The inventory operation would cost a lot of money. Manpower and material resources have to suspend other operations during the inventory, which is subject to many restrictions.
Using the Intermec CK30 wireless handheld terminal, the warehouse manager can directly scan the barcode of the item with the CK30’s built-in barcode scanner when performing inventory operations, and submit the data to the ERP system using the wireless network. The ERP system Complete the collection, update, and statistics of item information. With the CK30, the warehouse manager can arrange work intervals to carry out inventory operations. While reducing the workload of the administrator, the data is more accurate.
Tianjin Novo Nordisk uses Intermec’s wireless equipment to implement full-process control and management of all links in the warehousing process, and can implement barcode label serial number management for the cargo location, batch, shelf life, and delivery, and control the entire receipt and delivery of goods. All raw materials and finished product information are collected in the ERP system for standardized operations in each link, such as replenishment, collection, and delivery. This effectively improves the quality and efficiency of inventory management, reduces inventory costs, and makes it possible to track product quality.
future
After using the Intermec mobile data collection terminal for 10 months, Novo Nordisk’s inventory accuracy rate has increased to 99.8%, and by interacting with ERP data, it has ensured the accuracy of the implemented inventory data in the ERP. The dynamic and comprehensive allocation of human and material resources, the dynamic allocation of human and material resources based on the batch of goods in and out of the warehouse, and the full use of resources have significantly improved the management speed of its logistics chain, which is more efficient and faster, and improves the operating efficiency of the system. Significantly improve its market supply capabilities, and the satisfaction of customers and employees has also been significantly improved. In addition, the reduction of manual control also reduces the idle time of employees and the probability of human error, thereby improving production efficiency. As the system runs, the benefits that companies can get from it will continue to grow.
[ad_2]