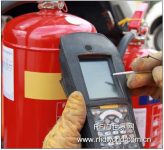
British construction equipment service company adopts RFID to greatly improve equipment inspection efficiency
[ad_1]
British construction equipment service company Magnor Plant Ltd. is a subsidiary of the construction company Morgan Sindall. The company now uses RFID technology to automate equipment inspections, thereby reducing the time it takes to manually record inspection results in the past. Before the RFID system was adopted, the same equipment inspection process would take a few more weeks.
Morgan Sindall’s local construction sites leased winches, construction equipment, weightlifting machinery, safety equipment (such as gas detectors, chemical respirators and oxygen masks), vehicles and office trailers and other equipment from Magnor. Using the RFID system, Magnor can learn the location of each piece of lifting equipment and safety equipment (a total of 4,000 pieces of equipment are distributed across 40 construction sites) and the equipment inspection results of the day, said Jonathan Hall, Magnor’s general manager. The company uses 4hSolutions’ Assettagz solution. The entire system includes a handheld reader, RFID tags and a server for storing data.
The inspector uses the handheld to read the RFID tag on the fire extinguisher
Morgan Sindall’s construction projects include railways, highways, residential and commercial buildings. According to relevant regulations, weightlifting equipment and safety equipment must be inspected every 6 months, so Magnor sent inspectors to all the company’s construction sites in the UK, Scotland and Wales to identify and inspect every piece of equipment used by Morgan Sindall workers. If the equipment fails the test, it will be discontinued and sent for repair or direct replacement.
Morgan has as many as 600 pieces of equipment at each site, many of which require regular maintenance. In the past, inspectors used paper and pen to manually record the serial number and test results of each piece of equipment, and then took or sent the records back to Magnor’s office in Rugby. There, managers read the records and manually enter the results into the computer. If they cannot recognize the handwriting of the inspector, they must call to confirm.
This manual recording process is not only error-prone, but also time-consuming. Usually, only a few weeks after the equipment inspection is completed, the inspection data can be turned into electronic files, and the manager of the construction site can receive the inspection report. In addition, during the inspection, if the site fails to provide the inspector with the quality certification and other documents of a tool, the inspector will take the equipment away, which often causes work delays.
At the beginning of 2009, Magnor found 4hSolutions, which provided Magnor with a tracking system similar to those used by other companies, such as Byrne Group. However, unlike Byrne Group, Magnor’s main challenge is to track detection results, not equipment. position.
Using the 4hSolutions solution, Magnor sticks Assettagz adhesive 125 kHz RFID passive tags (using a proprietary air interface protocol) to each piece of weightlifting or safety equipment. The unique ID code of each label corresponds to the data of the attached device on the server, said Andrew Davies, the company’s management director. The ID code, description and assigned site name are also entered into the Assettagz service software.
Magnor inspectors bring a Workabout Pro handheld computer with an embedded RFID reader to the construction site. The handheld computer runs Assettagz software and is equipped with a GPRS connection. When testing the equipment, Stuart Faulkner, Magnor’s security equipment manager, said that the inspector first enters a password that represents his identity, then reads the device tag, and the handheld will display a drop-down menu and instructions to guide the user through the entire inspection process. The detection information is then sent to the server, and Magnor management can view the information. When leaving, the inspector directly prints the inspection result and signs it on the construction site. If the device fails to pass the test, the tester will indicate the result on the handheld and then take the device away.
Since the application of this system was very successful and significantly improved the inspection efficiency, Davies said, Magnor also began to label fire extinguishers. There are approximately 30-50 fire extinguishers on each site. Unlike other types of safety equipment, fire extinguishers require more frequent periodic inspections. During the inspection, the inspector scans the RFID tag on the top of the fire extinguisher, the Assettagz software of the handheld device displays the detailed information of the device, and sends the inspection data to the server. The Assettagz software will also issue an alert to indicate the list of devices whose detection date is approaching or expired, and it can also provide a list of devices that cannot pass the detection.
According to Hall, the RFID system reduces the inspection time for inspectors from 45 minutes-1 hour to 15-20 minutes, and both the company and the site manager can get the test results in a timely manner.
[ad_2]