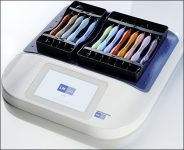
Columbia University School of Dentistry uses RFID technology to track dental instruments
[ad_1]
When entering the Columbia University School of Dentistry (CDM), students need to purchase their own dental instruments for patients to use in the school’s clinic. At the same time, they are also responsible for ensuring that these tools are not lost. Dental instruments include mirrors, probes and probes. Each instrument is approximately 6 inches in length, cylindrical, and most of them are made of steel. Tracking these items is a difficult task for students and clinics. Lost tools must be replaced, which is a huge expense for clinics and students.
Therefore, the CDM adopted aRFIDThe system is used to track each device and its packaging during clinical use, sterilization and storage. The technology was provided by LM-Dental, a dental instrument manufacturer, and was put into use in July 2015. Most of LM-Dental’s instruments are pre-attached with Xerafy RFID tags of the autoclave version, and have steel cores and silicone shells. CDM staff will also attach Xerafy tags to equipment not provided by LM-Dental. Currently, the CDM has attached 10,000 devices and it is expected that all 20,000 items will be attached by the end of next year.
(When the box containing the dental instruments is placed near the LM-Dental reader, the device will read the Xerafy tag attached to each tool, and then the system will confirm whether all items are on the box.)
Steven Erde, CDM’s chief information officer and assistant professor of oral health informatics, said that the RFID system is a good way to record the use of each tool, sterilization and compliance, and this is also the main driving force for CDM to use RFID systems. However, the management of dental instruments in schools with hundreds of students is far more complicated than in small dental clinics.
For clinics with 150 patients and dental students (approximately 80 new students are enrolled each year), the difficulty is not only when the equipment is in the hands of the students, but also the follow-up of the clinic’s own staff when they use autoclave sterilization is also a big challenge. . Before deploying the RFID system, each student had to purchase a large set of equipment to deal with all potential situations encountered in the box. These packaging boxes are made of a mixture of plastic and stainless steel, ranging in size from 14 inches * 6 inches * 1 inch to 6 inches * 2 inches * 2 inches. The students put these dental instruments in boxes in the central storage area, and then send them to the clinic for sterilization and disinfection until they are taken out when needed. During cleaning and disinfection, clinic staff do not need to check whether each box of instruments is complete. Instead, employees visually confirm this information.
In this solution, each device is attached with an RFID tag and bound to the asset data in the dental tracking system provided by LM-Dental. By using the RFID system, CDM eliminates the manual actions of students. Instead, the instrument box is inspected by the CDM, sterilized and stored.
During this process, CDM installed LM-Dental’s desktop RFID readers at several key locations (instrument inspection points, before instrument sterilization, and after instrument sterilization). In the future, readers will be installed in the storage area to help employees keep track of equipment that is not in use.
Stephen van Heerden, the company’s system sales manager, said that LM-Dental chose the Xerafy Dot XS and Dash XS RFID tags of the high-temperature and high-pressure sterilization version because other manufacturers cannot provide such small-volume tags that the company needs. In addition, Xerafy sales and marketing manager Moses Chang said that apart from this label, there is currently no similar verified and large-scale use label on the market. He said: “From a technical point of view, the biggest challenge is to create a small enough label that does not affect the use, while still providing the performance that customers need. Xerafy’s autoclave series of labels can perfectly solve these problems.”
Erde said that the RFID solution was to some extent catalyzed by CDM. CDM is proficient in technology and hopes to find a technical method to facilitate the tracking of tools.
CDM found LM-Dental and jointly developed an RFID solution to manage dental instruments. After 9 months of testing, the CDM system was put into use last summer.
When students need tools, they need to submit requirements in the equipment inspection area and read the ID card with the HID RFID reader, and then the ID number of the ID card will be sent to the LM-Dental software for verification. When an employee is looking for a specific student’s instrument box at the inspection window, he can find the location of the tool only by reading the ID card.
After use, the students will return the instruments that are to be sterilized. Before the disinfection process is over, the staff will place it at the entrance and exit of the autoclave for reading. The system will determine whether the device is missing based on these data. If it is lost, CDM can contact the student to confirm whether it can be found.
After disinfection, these tools and instrument boxes will be read again at the exit of the autoclave. At the same time, the system will update the status of these devices.
The clinic disinfects 200 to 300 instruments every day and probably finds a dozen problems. After the use of the RFID system, the number of problems has decreased.
In addition, the clinic also uses the system to automatically record tool inspection time, return time and disinfection time. These data also help clinics to better manage equipment.
In the next step, CDM intends to use the system for tracking in three storage areas. Employees in each location use RFID readers to read the tag ID. In addition, CDM is designing a large clinic with 50 dentist chairs, and the RFID system will also be used here.
Erde said: “We are tracking the usage rate of the device.” He said that the software will determine that the student picks up the tool based on the distance of the tag from the reader, thereby determining that the device is in use. By judging how often devices are used, CDM can better understand which devices are more useful and which are not needed. Erde said: “Through these data, we can also know what equipment utilization model is more effective.”
Erde also said that the clinic also hopes to track patients through RFID wristbands and readers to better understand the patient’s treatment time.
In addition, the software will be integrated with CDM’s own software in the future.
In addition, the third stage of the project may use RFID equipment cabinets to automatically monitor the status of equipment in real time.
[ad_2]