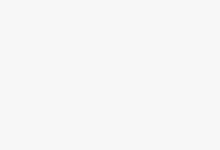
Danish hospitals are testing the application of RFID solutions in the tracking and management of surgical instruments
[ad_1]
Four hospitals in Denmark are testing a surgical instrument management solution consisting of processing software, reader devices and Xerafy’s RFID tags provided by Caretag. The solution is mainly used to track the use process, disinfection process and maintenance process of surgical instruments. Improve the efficiency of device management and reduce the labor required for device management.
Several Danish hospitals are testing the aforementioned RFID-based medical device tracking solutions. This program is provided by Caretag, which can improve the efficiency of medical device management and reduce the incidence of device loss. The test and follow-up evaluation are funded by the Danish government agency Markeds Modningsfonden and are expected to take more than one year. Early test results show that the RFID tracking system can save a lot of labor and reduce potential errors.
Xerafy EPC Gen 2 passive UHF RFID readers and dedicated readers provided by Caretag are used in this solution. As shown in the figure, on the left is the Dot-On XS passive UHF metal tag for medical devices provided by Xerafy, and on the right is the Dash-On XS passive UHF metal tag for medical devices provided by Xerafy.
The completeness of medical equipment and surgical tools is of great significance to the smooth progress of the operation, and these tools are part of the hospital’s assets, and the hospital attaches great importance to the effective tracking of the equipment and tools. Previously, manual recording was used for tracking management, which was time-consuming and labor-intensive, and there were still certain errors. In order to solve the above problems, the hospital decided to use RFID technology to improve the efficiency of tool management in the surgical process, disinfection process, and maintenance process. However, the use of RFID technology to track medical devices is challenging. There are two reasons: First, the particularity of medical tools (very small medical tools, such as scissors, tweezers and knives, etc.) determines the particularity of the labels used, and most ordinary labels cannot be used; second, surgical appliances need After the autoclave sterilization process, the label can withstand high pressure, high temperature and other special environments.
Caretag provides RFID tracking solutions for these hospitals in Denmark, including data processing software and reading and writing devices. When the tool is misplaced or lost, the system will issue an alarm to warn the manager. In 2012, Caretag demonstrated a set of laundry management solutions based on RFID technology for a hospital named Rigshospitalet in Copenhagen.
The test process simulates a complete operation, disinfection, and maintenance process. First, place the labeled tools in a tray. The tag ID is associated with the serial number of the pallet or the tool itself, and is stored in the Caretag software along with other information about the tool. The software also records the information in a tool kit composed of trays and tools used in an operation. An RFID tag is also installed on the tray. Before the operation, the tray with the tools is placed in front of the reader, and the tags are read to confirm whether the tools are complete.
After the operation, put the sorted tools together with the tray in front of another reading and writing device, and read the tags installed on the tools to see if there is any loss. After confirming that it is correct, send it to the sterilization room, and pass through the RFID read-write device when it is sent in and out.
The testing process will continue for 6 months. If the test results show that the RFID solution can improve management efficiency, reduce management costs, and improve safety, these hospitals will install the solution for their operations and disinfection processes. In addition, several hospitals in Sweden and Germany are interested in testing the program.
[ad_2]