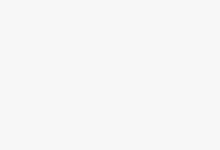
Detection of tiny details of medicine bottles under high-speed conditions
[ad_1]
Major drug manufacturers use the Cognex In-Sight vision system as part of their inspection machine, which is mainly used to detect vials containing serum, as well as detect possible small impurities in the serum. In-Sight 5603 has proven to be the only solution for this type of high-speed and sensitive inspection.
IPF Ingenieria is located in Barcelona, Spain, and specializes in producing special machines suitable for customers in high-end industries. One of the special customers is Fresenius Kabi, a global leader in injection therapy and clinical nutrition. The company needs a special machine that can effectively solve the problem of small serum bottle inspection. After the recommendation and integration of Cognex partner Edge Vision, IPF provided them with a set of machines equipped with Cognex In-Sight vision system. In this application, the installed In-Sight camera can not only detect the liquid level in the serum bottle, but also detect the impurities in the bottle at a rate of 10,000 bottles per hour.
Even 1mm can be reliably detected
After cooperating with many different vision suppliers, IPF finally chose Cognex vision system as their strong backing to solve the pressure of the industry. In this special application, In-Sight 5603 has been proven to be the only vision system capable of this task. reason? To ensure that no impurities are present in the serum, this application requires ultra-high resolution vision. You need to know whether the vision system you rely on can detect impurities as small as 1 square millimeter. The speed of the 5603 and its ability to memorize the test results at the highest line speed are excellent, unmatched in the industry.
10,000 bottles per hour
Each hood pack contains 5 bottles of serum. Two machines are equipped with two In-Sight cameras. When the medicine bottle passes along the conveyor belt, it is inspected by the camera. In-Sight uses the powerful Cognex vision tool PatMax™ for workpiece search and positioning, thereby positioning the serum unit for impurity detection on each vial. If any impurities are detected, the package will be rejected. All medicine bottles that pass the inspection will be sent to the packaging place for packaging. The vision solution has been fully integrated into the company’s quality management system. The user-friendly configuration environment in In-Sight Explorer has been proven to be easy to operate and has significant advantages. It has a convenient user interface that allows users to program for visual tasks.
Results and advantages
? Speed-10,000 bottles detected per hour
? Reliably eliminate defects at high speed
? No error rejection
? Simple and easy to use
? Simple integration with company systems
? Return on investment within one and a half years-by reducing labor costs
? Based on these favorable results, IPF plans to install three more machines with vision systems this year.
Major drug manufacturers use the Cognex In-Sight vision system as part of their inspection machine, which is mainly used to detect vials containing serum, as well as detect possible small impurities in the serum. In-Sight 5603 has proven to be the only solution for this type of high-speed and sensitive inspection.
IPF Ingenieria is located in Barcelona, Spain, and specializes in producing special machines suitable for customers in high-end industries. One of the special customers is Fresenius Kabi, a global leader in injection therapy and clinical nutrition. The company needs a special machine that can effectively solve the problem of small serum bottle inspection. After the recommendation and integration of Cognex partner Edge Vision, IPF provided them with a set of machines equipped with Cognex In-Sight vision system. In this application, the installed In-Sight camera can not only detect the liquid level in the serum bottle, but also detect the impurities in the bottle at a rate of 10,000 bottles per hour.
Even 1mm can be reliably detected
After cooperating with many different vision suppliers, IPF finally chose Cognex vision system as their strong backing to solve the pressure of the industry. In this special application, In-Sight 5603 has been proven to be the only vision system capable of this task. reason? To ensure that no impurities are present in the serum, this application requires ultra-high resolution vision. You need to know whether the vision system you rely on can detect impurities as small as 1 square millimeter. The speed of the 5603 and its ability to memorize the test results at the highest line speed are excellent, unmatched in the industry.
10,000 bottles per hour
Each hood pack contains 5 bottles of serum. Two machines are equipped with two In-Sight cameras. When the medicine bottle passes along the conveyor belt, it is inspected by the camera. In-Sight uses the powerful Cognex vision tool PatMax™ for workpiece search and positioning, thereby positioning the serum unit for impurity detection on each vial. If any impurities are detected, the package will be rejected. All medicine bottles that pass the inspection will be sent to the packaging place for packaging. The vision solution has been fully integrated into the company’s quality management system. The user-friendly configuration environment in In-Sight Explorer has been proven to be easy to operate and has significant advantages. It has a convenient user interface that allows users to program for visual tasks.
Results and advantages
? Speed-10,000 bottles detected per hour
? Reliably eliminate defects at high speed
? No error rejection
? Simple and easy to use
? Simple integration with company systems
? Return on investment within one and a half years-by reducing labor costs
? Based on these favorable results, IPF plans to install three more machines with vision systems this year.
About Cognex
Cognex Corporation specializes in the design, development, manufacturing and sales of machine vision and industrial systems or visual equipment. Cognex’s vision and ID systems are widely used in various inspection, identification and guidance applications throughout the manufacturing and distribution processes throughout the world. Cognex is a global leader in the machine vision and industrial ID industries. Since its establishment in 1981, it has installed more than 800,000 systems around the world and has earned more than $3 billion in cumulative revenue. Cognex is headquartered in Natick County, Massachusetts, with regional offices and distributors in North America, Europe, Asia, Japan and Latin America. For more information, please visit Cognex Corporation online at http://www.cognex.cn.
[ad_2]