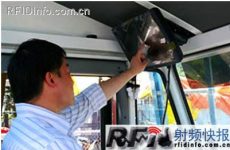
Home furnishing retailer CPWM uses RFID system to manage transportation vehicles
[ad_1]
Cost Plus World Market (CPWM, headquartered in Oakland, California), a world-renowned household goods retailer, uses an RFID real-time positioning system to monitor trailers arriving at a distribution center in northern California and speed up the receiving process.
CPWM has nearly 300 stores in 34 states and revenue in 2007 exceeded $1 billion. Previously, CPWM had been using the Yard Hound parking lot management system designed by PINC Solutions to track 75 trailers. The system uses EPC Gen 2 RFID tags in a plastic case and can be permanently installed on a trailer.
When the trailer enters the parking lot, the RFID reader will read the tag on the trailer. After the trailer enters, its tag will be read by the RFID reader installed on the truck in the parking lot to rearrange the position of the vehicle. When the truck moves around the yard, its tracker will collect the ID number of the trailer tag, and then connect it with the location data determined by the built-in GPS receiver.
Since the truck is mobile, fixed sensors must be installed on the trailer to measure the acceleration and steering data of the truck. This data plus the signal strength of the tag reading can accurately locate each trailer using the algorithm developed by PINC.
Real-time operation picture of the parking lot
The tracker stores the location and time stamp data of the trailer and sends this data to PINC’s website software platform. The PINC server collects the truck information data of each depot, combines the data with the depot map, and then provides a real-time operating picture of the depot.
CPWM parking staff can access this map by logging in to the Yard Hound software connected to the company’s parking management system. The yard management system will contain a freight list for each trailer. In this way, each worker can see the ID number of the trailer and the product information in the trailer. In addition, CPWM can set alarms to the Yard Hound software. For example, when a trailer does not enter the unloading area within a given time but enters the trailer storage area, the Yard Hound software will issue an alarm. This feature is mainly set up to ensure that seasonal products can be unloaded and distributed according to the schedule, and also to ensure that the perishable products stored in the refrigerated trucks are processed before they rot.
Vehicle RFID tags
Retailers have stated that the use of the PINC system has improved the efficiency of parking lot management and reduced the cost of manpower to manage the parking lot. However, they did not discuss the specific application of the system to the RF Express, nor did they release the exact time when the results were achieved and the exact information on the labor savings brought by the Yard Hound system. Aleks Gollu, CEO of PINC Solutions, said that CPWM will definitely get tangible benefits by using the performance provided by the Yard Hound system.
According to Gollu, the first level of these performances is: companies can only use the reader at the main entrance of the parking lot to automatically identify which trailers have entered the parking lot when. The second level is: install a tracker on the truck in the parking lot to detect the location of the tagged trailer on the map. The third level is to enable the parking lot manager to exchange graphics and text information with the truck driver via Wi-Fi wireless local area network. This process is mainly carried out through the PINC software module running on the mobile touch screen computer in the truck at the depot.
Using this feature, CPWM’s parking lot manager can prompt the driver to park the trailer at the specified location. They can also use this feature to require the trailer to return to its position. The driver can tap the touch screen to confirm the command request, and the manager can ensure that the correct driver drives the correct trailer into the designated parking spot. If the truck is heading in the wrong direction, managers can use this feature to warn the driver. Gollu said that in the past, the parking process at the parking lot was done through radio communication and paper maps, so errors were not easy to detect early.
Gollu said that another PINC customer has been able to eliminate a rental truck based on the measurable performance provided by the PINC system. “When you calculate the labor, gasoline, maintenance, and rental costs for that extra truck, you know that you can save $90,000 per year after excluding it,” Gollu said. “Of course, if your company adopts green management, that effect can be achieved.”
Gollu added that the customer has also reduced the number of manual inspections of the parking lot—from 6 times a day to once a day. Manpower inspection of the parking lot is mainly for reviewing the operating quality of the website software, and each inspection takes 90 minutes on average. Gollu said that another customer expects to use this system to reduce the detention of trailers outside the lease by 80%. He also pointed out that this customer also hopes to reduce the number of empty trailers parked in the yard through this system.
[ad_2]