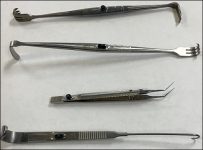
Michigan Podiatric Clinic uses RFID technology to track devices
[ad_1]
The Michigan Foot Clinic, Great Lakes Foot and Ankle Specialists, started using itRFIDThe technology automatically tracks surgical instruments or tools, thereby speeding up the process of loading tools into the tray, ensuring that no tools are left in the patient’s body or misplaced, and tracking the life of the instrument. This Surgical Safety Scanner system is provided by the start-up Surgical Scanner. The system uses passive UHF tags, handheld readers and software for managing data. The software can also bind each tag ID number with a photo of a specific device, manufacturer, part code, and usage history.
Jeff Szczepanski, a doctor at the clinic, said the program helped the clinic solve some challenges. Each operation requires the use of a specific set of tools, so it is difficult for doctors to distinguish between two trays with different instruments. Many instruments look similar, so unless there are multiple visual inspections manually, the instruments are sometimes placed in the wrong tray. After high-temperature sterilization of the tray containing the instruments, it is also difficult for us to judge which tools are inside. Therefore, the wrong tray may be brought into the operating room. In addition, Szczepanski said these tools are very expensive and are often lost. When they are lost, it is often impossible to trace the place where these devices were lost.
(Each medical device is glued or welded with an autoclaved Dot XXS or Dash XXS label)
Fred Schoville, president of Surgical Scanner, said that the Surgical Safety Scanner system was officially put into use three and a half years ago. He developed this technique after talking to Carol Schmucker, a retired nurse who understands surgical instrument tracking. This solution can be used to automatically count and manage instruments and consumables before and after surgery.
In the beginning, the system was designed to replace the instrument counting process before and after medical staff’s surgery. But this version used by Great Lakes Foot and Ankle Specialists also includes functions such as monitoring the use of equipment, disinfection and repair time and reminders. The system can also determine how often the device is used.
The manual tracking process is very time consuming. Surgical Scanner conducted a test, and finally found that it takes 2 employees to spend 4 minutes to count the surgical trays. After the operation, these tools need to be re-counted, which usually takes 10 minutes, because they are usually more difficult to identify. On the other hand, this system only requires one employee to complete the same job in 30 seconds.
To develop this system, the company spent several years testing a variety of passive UHF RFID tags, but eventually found that most of them were not suitable or could not be well attached to small, metal devices to be tracked. In the end, they chose Xerafy autoclaved Dot XXS or Dash XXS labels and inserted them into the secondary heat-shrinkable plastic sleeve designed by Surgical Scanner. Surgical Scanner welds or glues a label on each device, and then attaches a layer of thermoplastic film to the label. Xerafy has carried out 1000 times of pressure test for cleaning agent disinfection. At the same time, Surgical Scanner has been sterilized hundreds of times, and these labels are still in good condition.
The company has also developed a software to make the equipment tracking process before and after surgery more reliable and save manpower. The software runs on the user’s own server.
In this project, Surgical Scanner attaches a Xerafy passive UHF tag to each device, and binds the tag ID and item-related information.
When staff prepare surgical trays for doctors, they can check the hospital’s pre-entered equipment list in the Surgical Safety Scanner system. This list may be general for a certain type of surgery, or it may be specifically selected by the doctor for the operation.
After the instruments are packed into the pallet, employees need to use the CipherLab 1862 handheld reader to read them. The handheld reader transfers the read data to a computer running Surgical Scanner software so that employees can check whether the packaging is correct. Lost instruments will be displayed in red, while normal instruments will be displayed in green font.
Then, the tray will be sent to the operating room. Employees in the operating room are also equipped with RFID readers, and they will also scan the tray to confirm that all required instruments are in the tray. When using the instrument during the operation, the doctor will remove it from the tray and place it in the used tray. If the instrument falls to the floor, it will be supplemented with a new instrument, and this event will also be recorded with a handheld reader.
After the operation, employees need to read the labels of the unused and used pallets. The software can then determine if any equipment is missing.
When an item is lost, the software will issue a warning and display the photo and description of the lost item on the screen. The system also allows employees to enter relevant information during the operation, such as RFID tag failure.
Before putting the used instruments into the cleaning and disinfection unit, the labels need to be read again. After reading the label, the user can create a record of disinfection item information and time.
In addition, Great Lakes Foot and Ankle Specialists still use this technology to carry out pallet inventory three times a day. Currently, the clinic has attached labels to all surgical instruments.
Most clinics have 10 to 12 instruments in their trays, and currently there are 20 to 25 trays in clinics. Szczepanski explained that after the automated inventory process, it is very difficult for employees to lose surgical instruments as long as they do not lose the instruments during the operation.
Since the software can display the photos of each read item, the system can also provide training for every new employee who needs to learn the name of the device and the type of operation.
Szczepanski said that the system has improved efficiency and reduced losses caused by lost equipment, and he also plans to expand the scope of use of the system. He said: “In the future, we will also track the life of the equipment by identifying the number of times the equipment is used.” The system can also be used when there is a failure. For example, when the autoclave fails, the software can determine which instruments have been sterilized, so that employees can take out the sterilized instruments for use first.
To deploy such a system, a small clinic would cost about US$3,000 to US$5,000, while a large clinic would cost US$1 million. At the same time, the system also provides a pay-per-use version, charging based on the number of label scans. Schoville said that Surgical Scanner also plans to launch a dental version of the device tracking program.
(Exclusive manuscript of rfid world network, please indicate the source author for reprinting!)
[ad_2]