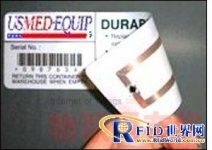
RFID solutions help hospitals greatly reduce inventory
[ad_1]
New York Hospital Queens is an emergency care hospital located in the Flushing District of the city. The Interventional Radiology Department of the hospital is currently experimenting with RFID technology to manage medical equipment and consumables such as stents, catheters and filters. Using LogiTag Systems to provide this set of solutions, employees can remove implants or other necessities from locked cabinets, and the system automatically records the removed objects and the corresponding identity of the personnel. In addition, this system also records the items actually used in the operation through barcode scanning. “In the future, the hospital will combine this information with existing management software to realize the corresponding charges for patients,” said Jed Golden, the hospital’s material management director.
LogiTag was founded in Israel in 2004 and provides a variety of RFID solutions for multiple markets, including active RFID real-time location systems (RTLS) for medical use. According to Glenn Tamir, the company’s business development director, every medical institution in Israel has LogiTag’s technology.
Queen’s Hospital in New York has adopted LogiTag’s Smart Cabinet and StockBox solutions, both of which use 13.56 MHz passive RFID tags that comply with the ISO 15693 standard. Smart Cabinet is used to track high-value and time-sensitive items, such as implants required for surgery, with embedded LogiTag readers (Tamir refused to disclose the number of readers and antennas installed in each cabinet) to read authorized employees to put in and Items taken out. StockBox is used to manage disposable consumables, such as surgical supplies. When the consumption of consumables reaches the preset value, the staff inserts an RFID tag into the StockBox, which triggers the system to send orders to the warehouse or storage room.
Queens Hospital installed two smart cabinets in its interventional radiology area in January 2012, followed by a StockBox. If this system proves to be able to realize the automatic management of inventory, the hospital will also adopt this system in other areas, such as the interventional heart area and the surgical area.
When medical supplies from the interventional radiology department arrive at the hospital, employees stick a passive high-frequency RFID tag to each item, and then use a barcode scanner to read the serial number of the item, and add the serial number, manufacturer, model, and serial number to each item. The size and shelf life correspond to the RFID tag attached. All this information is stored in the LogiTag software installed in the hospital’s back-end system.
Employees stick a passive high-frequency RFID tag to each item
Smart Cabinet is a lockable cabinet with five shelves that can store up to 350 implantable devices and other medical products. When a hospital worker needs to use an implant, he or she must show the employee ID with an embedded RFID tag. The RFID reader of the smart cabinet reads the unique identifier of the tag, and the LogiTag software determines whether the employee is authorized to use the cabinet. After the identity authority is verified, the software will automatically store the employee’s identity ID while sending an instruction to unlock it.
Many items may be taken away frequently, but they are not actually used. For example, during surgery, doctors may require implants of multiple sizes for occasional needs. After the operation, no items need to be returned to inventory. In the past, employees usually manually record the ID codes of items or scan barcodes in the entire process. Now the smart cabinet automatically sends information to the back-end system based on the item ID codes and employee ID codes that are no longer read.
When the operation is over, the employee shows his ID to the smart cabinet, puts the unused items back into the cabinet, and the system automatically records which items have not been used. For those used items, the staff keep their packaging bags, put them in a trash bin, and bring them to a barcode scanner connected to the computer; log in to the software, click on the patient’s record, and scan the barcode of the packaging bag. The system will automatically import the scanned data into LogiTag software.
At the end of a day’s work, LogiTag provides the management with detailed records of the use of items, such as which items have been taken, which items are returned to the cabinet, and the corresponding personnel and patients who used them, and reminded which items may be lost. In this way, Tamir said, the loss of high-value medical supplies was greatly reduced.
At present, the hospital has also incorporated the existing system to introduce the StockBox system into the consumable storage shelf. The hospital has adopted a preset system in the past, that is, setting the minimum amount of consumables stored. Combined with the StockBox system, an RFID tag is placed at the reading point of each shelf. When the consumables reach a predetermined value, the staff takes the RFID tag of the shelf and inserts it into the nearby StockBox.
The embedded RFID tag of StockBox reads the ID code of the tag, and sends the information to the StockBox software through the cable side connection. The software sends replenishment notices to authorized employees. When the consumables that need to be supplemented arrive, the staff unlocks the StockBox, takes out the RFID tag, and puts it back to the reading point of the shelf, and at the same time updates the inventory information stored in the software.
These two systems have helped hospitals greatly reduce their inventory. Golden claims that the system can also detect and remind staff to give priority to using medical supplies that are nearing the end of their shelf life and reduce hospital losses.
[ad_2]