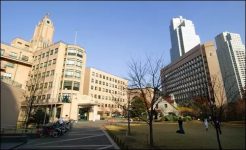
Tokyo Hospital uses RFID shelves to track equipment status
[ad_1]
St. Luke’s International Hospital in Tokyo completed a pilot project for mobile RFID tracking of equipment. The hospital found that the technology can determine the inventory of each ward in real time and reduce the number of visits to the central clinical engineering room by approximately 55%. The technology is called Recopick and is provided by Teijin, a Japanese carbon fiber and plastic technology company.
St. Luke’s Hospital receives 2550 outpatients every day and has a total of 520 beds. The hospital building has 13 floors with an area of approximately 60,000 square meters. Currently, the hospital is continuously expanding to meet the needs of the community. Recently, the hospital added a maternity clinic with 19 beds.

St. Luke’s International Hospital
In this hospital, most of the equipment that is no longer in use (such as infusion pumps, syringe pumps, low-pressure continuous suction devices and oxygen flow meters, etc.) are stored in the central clinical engineering room. This means that many employees looking for equipment enter and leave the central clinical engineering room every day. For equipment management, the hospital used a bar code system, and the bar code must be scanned when the equipment is loaned out and returned. But this process is very time-consuming, so nurses store these devices in their wards for quick access. For hospitals, this means that items are lost, and they need to frequently replenish equipment.
Therefore, St. Luke’s International Hospital began to look for a better solution in 2016 and began to deploy Recopick in the spring of that year. Approximately 1,300 pumps and oxygen flow meters are attached with passive UHF RFID tags with waterproof enclosures.
Natsuki Aramoto, head of the company’s intelligent perception application development team, said that all shelves in the medical engineering center and 22 wards are equipped with Recopick RFID-enabled sheets. The marked items are placed directly on these sheets. Each shelf unit is equipped with a CS468 card reader provided by CSL and a Teijin antenna to read the tag ID number.
The card reader will forward the collected data to the software, indicating the storage location of the item. Recopick also provides a processing unit that supports RFID so that users can view discarded items. The engineering room shelf is divided into two categories: the area of equipment to be cleaned or maintained and the area of equipment that has been cleaned and maintained.
When the hospital marks the equipment, the software will store the item-related information and bind it with the tag ID. This information will be processed by Recopick software.
When a nurse takes an item from the engineering room, he only needs to remove it, and the system can automatically update the status. If the tag has not been read for more than 120 minutes, its status will be updated to “in use”.
After the equipment is used, the nurse needs to return it to the engineering room for cleaning and maintenance. Employees only need to place it on the shelf, and the system will automatically update the status. After cleaning and maintenance, employees will place it in the maintained area for next use.
When looking for a specific device, employees can search within the software to confirm the real-time location of the item. Aramoto said: “The hospital can analyze these data to confirm the utilization of the equipment.” In 2012, Teijin officially launched the Recopick solution. Since then, the company has been improving the technology.
[ad_2]