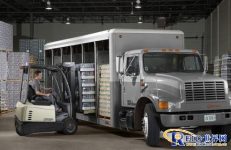
A large joint venture food company adopts RFID technology
[ad_1]
At present, RFID (Radio Frequency Identification) is widely used in warehouse logistics management system. In particular, the application in the three-dimensional warehouses of the tobacco factory fully demonstrates the advantages of RFID technology. RFID (Radio Frequency Identification) brings not only the improvement of information management mode, but also the improvement of benefits that users care about. Recently, as Chinese people pay more and more attention to food safety and hygiene, some large domestic food factories also hope to use RFID (Radio Frequency Identification) technology in the process of raw material processing, production, storage and transportation to realize material traceability and improve production. efficient.
Recently, as Chinese people pay more and more attention to food safety and hygiene, some large domestic food factories also hope to use RFID technology in the process of raw material processing, production, storage and transportation to realize material traceability and improve production efficiency.
All of this makes BLident feel like a duck to water in automation control and information management applications in the field of industrial control. Turck can provide perfect RFID solutions according to the various process conditions of customers.
industry analysis
The food industry is an emerging industry that Turck is currently focusing on. As Chinese people pay more and more attention to food safety and hygiene, the processing, production, storage and transportation of food raw materials are required to be traceable, so as to ensure the safety and reliability of the raw material processing process. During these processes,RFIDhas been fully applied. Especially in the raw material warehouse, the application of RFID further improves the automation and informatization of the control system, and the control scheme is more perfect.
client needs
This project is a monosodium glutamate production line invested and constructed by a large domestic joint venture food company. It has the most advanced production process and technology of monosodium glutamate in China, so the customer hopes to use products and systems with advanced technology, reliable performance and high cost performance in this project. In particular, a material traceability management system is established in the raw material transfer warehouse, and RFID technology is used to manage and trace materials in real time. The system should automatically convert the warehousing data sheet into the data information corresponding to a single pallet, and automatically write it into the code carrier through the RFID read-write head. Then, the system automatically allocates the warehouse area, instructs the forklift to place the materials in the corresponding position of the warehouse, and binds the position information and the code body information on the pallet together in the system. When leaving the warehouse, the system can automatically guide the forklift to extract materials from the warehouse according to the first-in-first-out principle and send them to the corresponding production line according to the production tasks decomposed into production orders. In the process of extracting logistics, the read-write head on the forklift should verify the carrier on the material pallet to determine whether the material is needed. If an error occurs when the material is put in, out of the warehouse, or entering the production line, the system should automatically alarm and prompt the operator to deal with it. In addition, pallets need to be reused throughout the warehouse management process.
digital tray
Trays embedded in code carriers are called digital trays and are widely used in all current warehouse management systems using RFID technology. This kind of pallet neither affects the loading of goods, but also facilitates the precise digital management of large quantities of goods.
Compared with traditional pallets with barcodes, digital pallets are easier to operate in the storage process. Because it does not require workers to print many barcodes in advance, then scan them one by one with a barcode gun, and then paste them on each pallet. Therefore, the working time is reduced and the difficulty of the work is reduced. In addition, the code carrier is suitable for harsh environments, and even if there are scratches and stains on the surface, it will not affect normal reading. Moreover, it will not be damaged by rain like barcodes and can be reused. The uniqueness of the carrier UID also improves the accuracy of material traceability.
RFID Forklift
In small warehouses, the use of RFID forklifts for material access is undoubtedly the best choice. Because the RFID read-write head is installed at the front end of the forklift, it is closer to the code carrier on the pallet, which greatly improves the reading effect. In addition, RFID forklifts track pallets in real time, ensuring the reliability of the entire warehouse management system. Moreover, in the entire storage process, human intervention is eliminated, which can reduce operational errors and improve operational efficiency.
BLident Solutions
Due to the scattered locations of production equipment and raw materials, the damp environment on site, the dusty materials, and the continuous production and variety of materials, we recommend customers to use the BLident system based on the fieldbus IP67 protection level. In addition, because the production raw materials are food products, a standard carrier with a protection level of IP68 and suitable for the food processing industry was selected in this project.
Since the material needs to be transported by a forklift, we install the read-write head on the forklift to read and write the code carrier on the material pallet. However, how the gateway also installed on the forklift communicates with the host computer has become a difficult problem before us. Because the forklift moves around, it cannot be connected to the host computer through cables. After many technical solution discussions and experiments, we finally realized the wireless network communication between the programmable Ethernet gateway and the host computer, thus solving this problem. At the same time, it meets the requirements of customers for real-time traceability of the entire production system and full-logistics and product life-cycle management.
Material Traceability System
The material traceability production management system is an important part of the real-time traceability of the whole logistics of the production system. According to function, it is divided into planning layer, configuration layer and execution layer.
Planning layer: This layer automatically counts product inventory, customer order status and raw material requirements, and then transmits these information to the material traceability production management system, and the execution system performs production or arranges inventory to meet customer order requirements.
Configuration layer: The system can automatically decompose the production order information provided by the user into production tasks and issue them to each production equipment and related departments. And according to the warehouse inventory, arrange production, and dynamically remind users to stock up. The relevant production information analysis results are sent to the relevant personnel’s mailbox in the form of a report or printed as a report.
Execution layer: The system mainly monitors the production process of all materials through BLident series products. According to the production process and logistics transportation process, RFID read-write heads are installed at the material entry and exit ports, and RFID read-write heads are installed at each entry line of the packaging production line to monitor the material flow throughout the process.
Customer Reviews
The system integrator for this project is the engineering department of Turck (Tianjin) Sensor Co., Ltd.
Li Jiaxuan, the project leader, said when talking about BLident products: “The shape of Turck’s RFID read-write head is similar to that of a proximity switch, and the installation is flexible and convenient; the code carrier moves at a speed of <0.5m/S to read and write, and can accurately read 200 Byte; the read-write distance is between 0~200mm, which fully meets the application needs; the working status of the read-write head and the read-write module can be understood through the LED light indication; the code carrier with IP68 protection level can be used in harsh places; Pre-cast cables ensure that data can be safely transmitted in harsh industrial environments; the maximum cable length of 50 meters greatly facilitates installation and reduces network nodes; standard PIB function modules simplify program development.”
[ad_2]