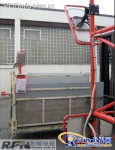
AL-KO uses RFID technology to improve production efficiency
[ad_1]
AL-KO, a German manufacturer of industrial air conditioners, is currently using RFID technology to track components at two production sites located 550 kilometers away.
Manufacturers of industrial air conditioners use parts with different configurations according to different customers. Before the production line is assembled, the appropriate parts are prepared. Since most parts processors are far away from AL-KO company, there are times when parts do not match and cannot be replaced in time, which causes certain losses to the company.
Forklift loaded with parts passes through RFID read and write door
Before the RFID system was installed, AL-KO’s production staff could not carry out an effective inventory of the parts in stock. Based on the above problems, the executives of AL-KO decided to use RFID technology combined with the existing SAP system to track the parts between the two places (the production place of the parts and the air conditioning assembly factory) in real time. The RFID-based solution is provided by B&M Tricon. After a period of testing, it was officially put into use in early 2009. Before the RFID system was adopted, the error rate of parts was 10%; after the implementation of the system, the data has not been counted.
In a system developed by B&M Tricon, a Deister Electronic UDC 160 UHF metal tag is attached to a Lutherstadt Wittenberg compression package and sent to the air conditioner production site.
Passive tags for outer plastic bags attached to the carrier
Various products for multiple orders are placed on separate carriers. After the parts are full, they are compressed and packaged, and a Handling Unit number is generated by the SAP system and assigned to each carrier. The processing unit code is written to the Deister tag via the Deister UDL 50 desktop reader. Then, attach the label to the carrier.
Next, the forklift is responsible for moving the carrier to the truck loading area. Forklift drivers use a tablet to record the truck’s license plate number, and then pass the loaded parts through the RFID read-write channel. The system records the label’s handling unit code, the truck’s license plate number, the time of loading, etc., and then sends a dispatch notification to the Jettingen-Scheppach plant. Based on this information, managers at the Jettingen-Scheppach plant can better manage product planning.
After the parts arrive at the AL-KO company’s assembly plant, they first pass through the RFID read-write channel, record the part information in the SAP system, and then remove the label for recycling. AL-KO recycles approximately 1,400 labels.
Before the implementation of the system, parts tracking between factories was manually recorded. About 200 pieces of information were recorded every day, which was time-consuming and labor-intensive, and the accuracy needed to be improved.
AL-KO spent a total of $296,000 on hardware and software, programming and consulting services for the solution. According to the company’s report, the solution has already benefited the company by not only providing accurate parts data in real time, but also greatly reducing the number of labor.
[ad_2]