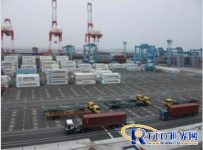
Application of APM Group’s Tire Crane Precise Positioning System
[ad_1]
User background:
Yokohama Port (Japan) is the second largest port in Japan, one of the world’s largest ports of 100 million tons, and one of the top ten container ports in the world. Yokohama Port has been renovated and expanded many times after the Second World War. The water area of ββthe port area is 7,339 hectares, and the wharf coastline is 40 kilometers, of which the water depth is more than 9 meters and more than 17 kilometers. The port area has a total area of ββ2,813 hectares, of which the industrial port area is 1,708 hectares and the commercial port area is 983 hectares. There are a total of 10 wharf ports, with a total of 245 large, medium and small berths, of which 120 are above the 10,000-ton class, with a maximum water depth of 23 meters and reliable 200,000-ton class oil tankers. The annual throughput is about 120 million tons, and the main export goods are steel, ships, vehicles, chemical products, machinery and equipment, canned food and textiles, etc.; the main imported goods are crude oil, coal, fiber products, ores, food and machinery.
Reasons for choosing a product:
The primary goal of the Port of Yokohama in the 21st century is to provide high-quality services and significantly reduce the operating costs of the port’s terminals. Further improving the automation level of terminal equipment can help to achieve this goal.
The use of Tangen tire crane automatic driving system greatly reduces the workload of drivers in driving, improves the daily workload of tire cranes, reduces collision accidents caused by fatigue, and reduces equipment damage and maintenance rates. While creating economic benefits for the port area, the related maintenance costs are reduced. Improve the overall capacity of the terminal to handle container containers.
System specific functions:
1. Precise positioning function of tire crane: using differentialGPStechnology, obtain centimeter-level positioning data when the DGPS system is working stably, calculate high-precision tire crane position, driving deviation and heading data by fusing GPS data and encoder data, accurately locate the tire crane, and report it to the terminal machinery total control system.
2. Tire crane automatic deviation correction control function: The tire crane position, driving deviation and heading data calculated by the DGPS system are calculated according to the established motion trajectory model, and the reference speed of the tire crane at the next moment is obtained. 5Hz or 10Hz The frequency is output to the PLC to control the cart drive motor to realize the automatic deviation correction control of the tire crane.
Customer Reviews:
The system operates stably around the clock, and the data is accurate and reliable, which has been affirmed and praised by users.
Related cases:
Maersk Group was founded in 1904 and is headquartered in Copenhagen, Denmark. After more than 100 years of development, it has become a world-leading company with strong strength in shipping, oil exploration and production, logistics, and related manufacturing industries. It operates in 125 countries and regions have business activities. As the container shipping branch of the Group, it is the world’s largest container carrier with a service network covering six continents.
Currently Maersk Container Terminal (APM Terminal) uses our company’s products including but not limited to the following ports:
[ad_2]