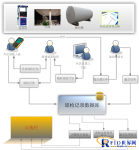
Application of Handheld Terminal in Gas Station Inspection Management System
[ad_1]
1. Background analysis
The gas station is the terminal of Sinopec’s sales business and a window to serve the public and display the corporate image. In recent years, by establishing a long-term mechanism for the standardized management of gas stations, Sinopec’s subsidiaries have carried out activities such as “Standards and Stars”, “Quality Service Month”, and “Safety Management Month” for gas stations to continuously improve the performance of each gas station. item management level.
Due to the wide distribution and huge number of gas stations, it brings considerable difficulties to precise management. Through management and practice, the superior management of the gas station has become more and more clear that it is impossible to continuously and steadily improve the management level of the gas station by staged and temporary surprise rectification of the gas station. Only by allowing the gas station to do a good job in the daily management of the gas station in accordance with various management specifications, adhere to the principle of self-inspection and self-inspection, and the combination of supervision and inspection by the superior unit, can the management level of the gas station be truly improved. .
1.1 Current Situation Analysis
In January 2010, on the basis of the former Northwest Shaanxi Branch of Sinopec Sales Co., Ltd., Sinopec Corp. reorganized and established Shaanxi Petroleum Branch.
Shaanxi Petroleum Branch implements the management system and operation mechanism of “flat management level, vertical business professionalism, clear position rights and responsibilities, and sensitive market response”, integrating warehousing, logistics, sales and service, and is mainly responsible for Xi’an, Hanzhong, Retail, direct sales and wholesale of refined oil products and sales of natural gas, lubricants and non-oil products in 10 cities including Baoji, Weinan, Xianyang, Ankang, Yulin, Shangluo, Tongchuan and Yan’an. As of the beginning of November 2010, the company has a total of 192 gas stations, 129 operating stations, 3 joint venture oil depots (1 in operation, 2 out of service), 1 leased oil depot, 3 oil storage depots, and 3 oil depots under construction. .
1.2 Demand Analysis
At present, the management and routine inspection work of gas stations and the inspection work of higher-level units generally still use handwritten records, so the relatively backward recording methods are not easy to organize and view, the inspection work cannot be effectively managed and supervised, and the inspection results are not easy to summarize and analyze. In addition, the failure of equipment and facilities is not reported in time, and it is impossible to report immediately after discovery. In order to improve this situation, an electronic, networked, safe, stable and applicable gas station inspection management system is urgently needed.
1.3 System goals
According to the current trend of informatization construction in the petroleum industry at home and abroad, comprehensively consider the general requirements of Sinopec Group Corporation for informatization construction in the future, combined with the current construction of the information system of Shaanxi Petroleum Branch and the requirements of Shaanxi Petroleum Branch for gas station management , build the “Sinopec Shaanxi Petroleum Branch Gas Station Inspection Management System” to continuously improve the timely rate and completion rate of the daily inspection work of the gas station and ME in the area, effectively improve the quality of the inspection work, and increase the attention to the gas station. The management strength of the new type of inspection work has been established, and the management level of the gas station has been stably and continuously improved.
1.4 Construction ideas
The gas station inspection management system contains a wide range of contents. It needs to be constructed according to the actual situation of the enterprise and the principle of overall planning and distributed implementation. The priority is determined according to the degree of urgent need in management and the degree of difficulty in implementation. The gas station safety management, equipment and facility management, sanitation management, and ME inspection in the area, which urgently need to be solved, are taken as the starting point, and are implemented in stages and steps to ensure the smooth implementation of the project and reduce the company’s implementation risk and initial investment.
1.5 Construction Scope
Provincial companies: retail centers, information centers, etc.;
Prefectural and municipal companies: local and municipal companies in Shaanxi Province;
Areas: Areas owned by companies in various cities;
Gas stations: Gas stations managed by companies in various cities.
1.6 Construction Significance
(1) Improve the quality of daily inspection work of gas stations
Due to the strong daily repetition of the daily inspection of the gas station and the ME inspection in the area, it is easy to cause some personnel to be bored. In addition, individual inspection personnel are lazy in their work, so the phenomenon of unscheduled inspections often occurs, which is obvious. The purpose of inspection is deviated. The gas station inspection management system can solve this problem, make the gas station inspection work in place, ensure that the inspection work is carried out in an orderly manner, and improve the quality of the inspection work.
(2) Improve the management level of inspection work.
Forms related to gas station inspection are generally filled out by hand, and the handwriting is not clear, which is particularly easy to misread the content, and is also not conducive to gas station viewing and analysis. After the system goes online, the gas station prints out inspection-related forms every day, and the inspection records can also be queried and analyzed in the system.
Managers at all levels of the province, city and district can easily understand the daily inspection of each gas station through the system’s query function, and can inquire, count and analyze the results of the inspection. For the difficult points that often occur in gas stations, we can focus on monitoring the points that are prone to problems in gas stations and solve problems in time.
(3) Strengthen the management of equipment and facilities, and reflect the refined management
The management of gas station equipment and facilities has always been a management problem, which mainly includes the management of gas station equipment implementation and the management of overhaul, maintenance and repair. After the system goes online, RFID chips will be attached to each equipment and facility, so that the equipment and facilities of the gas station are managed. At the same time, with the RFID chip, which equipment facility can be located, and all inspections of the equipment can be directly tracked. Records and inspections, maintenance and repairs.
(4) Timely feedback of information to provide work efficiency
In the actual work process, everyone’s work is very heavy, and it is impossible for everyone to continuously query the system during working hours in order to find problems and solve them in time. At the beginning of the design of the system, this application difficulty was fully considered, and the system made full use of the short message function, which greatly facilitated managers at all levels and gas station personnel. The message reminds the other party to ensure the continuity of the work. For example, during the inspection process, the faults found will be automatically sent to the gas station head and superior management personnel through short messages. The gas station will solve the faults found in the overhaul and maintenance of the equipment and facilities as soon as possible. If the gas station cannot solve the problem, the equipment and facilities fault information will be reported to the superior management department. At the same time, the system will automatically send the application information in a short and careful manner. For managers, managers can deal with faults in a timely manner.
2 System overview
The gas station inspection management system uses RFID radio frequency identification technology, replaces handwritten records with inspection PDA equipment, and replaces complicated paper forms with electronic data, so as to achieve scientific, efficient and accurate records and feedback, with reporting, statistics and analysis. Features. It not only meets the daily management requirements of gas stations, but also meets the management requirements of higher-level management units.
2.1 Basic principles
The core of the gas station inspection management system is the inspection PDA and RFID electronic tags.
The non-contact RFID electronic tag can provide a unique address code, install an RFID electronic tag for each equipment and facility that needs to be inspected, and correspond to the equipment and facilities one-to-one, which is equivalent to the identification of the equipment and facilities. The inspection personnel can read and record the address code of the RFID electronic tag and the inspection time and date by holding the inspection PDA. At the same time, they can input the status and data of the equipment and facilities through the keyboard and LCD screen on the inspection PDA. In this way, the inspection PDA can objectively record the inspection time, date, and related data of each equipment and facility.
After the inspection is completed, upload the inspection data of the inspection PDA to the gas station inspection management system database through wireless transmission, and then the gas station can print the inspection record through the gas station inspection management system, and the superior unit can print it through a portable printer. Inspection record sheet.
The gas station inspection management system also supports equipment failure reporting and inspection and analysis of inspection work (such as missed inspections, untimely inspections, etc.), and automatically generates various statistical reports through statistics and analysis.
[ad_2]