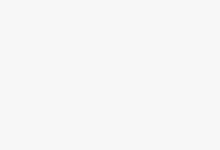
Application of RFID in Printing Production Management
[ad_1]
Shangji Electronics has revolutionized the introduction of RFID into the production management of the printing industry, and provides a complete set of solutions for factories by collecting workers’ production information and work efficiency in real time. Help managers obtain real-time production data from the system platform, and can understand production progress, optimize production schedules, and understand comprehensive information on employee performance, equipment status, and the quantity of work in progress anytime, anywhere. A variety of analysis data from different angles, so that managers can make objective decisions and deeply mine more meaningful data, thereby improving the production efficiency and management decision-making ability of printing enterprises.
1. The situation and characteristics of the printing industry
According to the information from the State Press and Publication Administration: At present, there are 101,948 printing enterprises in the country, with 5 million employees, and the total output value of the printing industry has reached 574.62 billion yuan, accounting for about 2.5% of the gross national product. “The printing industry, known as the ‘sunrise industry’, its development prospects are extremely attractive.
Compared with other industries, the printing industry has its own characteristics. For example, the production method is special, and the production must be organized according to the work order. The printed finished product can only be exclusive to a certain customer and cannot be replaced and processed; there are many kinds of products, and the order quantity must be treated separately regardless of the size, and the workload of production scheduling and accounting is large. ;Customers have high requirements for individuality, and products require high timeliness. If the product cannot be delivered on time, the product may be scrapped and bring huge losses to the enterprise. Therefore, in addition to advanced printing equipment and imagesetter software, production scheduling is particularly important.
Real-time control of production site conditions is an important basis for production scheduling, and is also one of the key points for the manufacturing industry to enhance competitiveness. However, without proper tools, it often becomes a difficult problem for enterprises. Even with the manual barcode reading work order (or RUNCARD, TRAVELCARD) used by most enterprises, it is time-consuming, and at the same time, the accuracy and real-time problem cause the production visualization to be delayed. Shangji Electronics revolutionized the introduction of RFID into the production management of the printing industry, which is the best tool for process management on the manufacturing site.
Second, the principle of system implementation
Shangji RFID printing production management system uses radio frequency identification technology (RFID) and wireless network technology. One of the characteristics of RFID is the rapid and real-time transmission of information. Through the rapid and real-time reading characteristics of RFID, the manufacturing process can be The status is presented to managers with extreme precision and speed, helping managers to understand production progress, optimize production schedules, and understand comprehensive information on employee performance, equipment status, and the quantity of work-in-progress anytime, anywhere. Various analysis data from different angles, so that managers can make objective decisions and dig deeper into more meaningful data, so as to improve the production efficiency and management decision-making ability of printing enterprises.
System Implementation Principle
◎Replace paper work orders with RFID tags, or attach RFID to work orders;
◎ Each worker is provided with a staff card shared with the attendance and meal access control;
◎Set up RFID readers in each production process;
◎ Workers first insert their own work card during production, then insert the material card on the work order, and start working, the system starts to collect data, and after completing one work order, the material card of the next work order is replaced, and there is no need to record manually;
◎ The system automatically records on-site information such as which work orders each worker is working on at what time period, the time consuming of each work order, and where the process is going;
◎ Employees can check their production records throughout the day through the self-service credit card terminal.
3. System Features
3.1 Plan information flow management based on intelligent production scheduling to ensure accurate matching and on-time delivery;
3.2 Logistics management centered on material requirements and inventory management to ensure resource optimization and cost effective control
3.3 Completely solve the problems of printing production scheduling and work order scheduling;
3.4 Comprehensively solve the cumbersome printing production process management problems;
3.5 The whole process management problem of printing quality;
3.6 Solve complex printing piece-rate wage accounting problems with simple methods.
4. Actual Results
1. Save labor and save labor costs;
2. Reduce the error rate, at least 5% of the error loss;
3. Improve production efficiency; the average finished product processing efficiency has increased by more than 30% compared with the same period; the highest finished product processing efficiency has exceeded 100% compared with the same period;
4. Key issues addressed by the system
4.1 The problem of low accuracy and unreliability caused by manual data collection.
Production enterprises in Guangdong and even southern China generally use manual or more traditional electronic systems to collect production and related data. A few large enterprises that use ERP systems actually rely on data, which will inevitably lead to inaccuracies such as errors and omissions. The application of RFID technology in the manufacturing process can reduce human participation as much as possible and realize automatic data collection, thereby solving the problems of low accuracy and unreliable data caused by manual data collection.
4.2 The existing system data update is not synchronized.
It is difficult for the computer system used by the existing manufacturing enterprises to collect data in time. For example, the most advanced bar code system also requires correspondingly trained staff to scan related goods with equipment such as bar code guns, but the scanned data is often not updated to the system immediately. If the barcode system is not adopted, the relevant data will be manually recorded in the form, and will be entered into the computer system at a fixed time every day. This practice caused the data in the system to be out of sync with the actual production-related data. As a result, excellent production methods, such as JIT production mode, cannot be realized due to the asynchrony of system data. The advantage of RFID technology lies in automatic and long-distance data collection, and the corresponding monitoring equipment can automatically detect the tag data within the coverage area, so it helps to solve the problem of asynchronous system data update.
4.3 Due to the repeated entry of data in each link, time, manpower and cost are wasted, and the possibility of data errors and omissions is increased.
Most of the manufacturing enterprises in Guangdong and even southern China have not adopted the world’s advanced production management model, and most of their businesses are actually independent. Raw material data is collected at the raw material supplier’s factory, product data is collected at the processing and assembly factory, and cargo data is collected at the logistics supplier’s warehouse. According to the principle of supply chain, most of the above data can be shared with each other and collected in advance. At that time, the principle of supply chain was difficult to implement due to the inaccuracy and unreliability of data due to the traditional way of data collection. On the premise of solving the accuracy of data collection, RFID technology helps to solve the problem of repeated data entry in each link of the supply chain. This saves a lot of manpower, material resources and time spent in data collection, and realizes the transformation from traditional manufacturing enterprises to modern manufacturing enterprises through the application of RFID technology.
[ad_2]