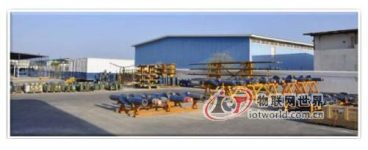
Application of zigbee positioning technology in Schlumberger oil warehouse management
[ad_1]
(Live picture)
With the continuous expansion of the scale of the enterprise, the number of types of materials managed by the warehouse has also continued to increase, the frequency of in and out of the warehouse has increased sharply, and the complexity and diversification of warehouse management operations have made it difficult for the traditional manual warehouse operation mode to meet the needs of today’s enterprises. The fast and accurate requirements of management have seriously affected the production efficiency of enterprises. At the same time, with the rapid development of computer and wireless technology, some enterprises have begun to apply wireless technology to warehouse management.
Scheme background
Schlumberger is the world’s largest oilfield technology service company headquartered in New York. It is recognized as the best software and service provider in the oil and gas industry, providing customers with real-time oil and gas field comprehensive services and solutions. The oil bases served by Schlumberger had the following problems with warehouse management: There were a large number of tools throughout the base, which were stacked in different areas of the base. Many tools are so similar in appearance that it is difficult to distinguish them with the naked eye. When a certain tool needs to be used, the staff often needs to move many other tools on site, and it takes a long time to search, and it is very difficult to find the specified tool. In addition, it is difficult to systematize inventory distribution records. It is very difficult to count the types and quantities of tools, and it is difficult to know which tools need to be replenished. The problem of tool management in the entire base is becoming more and more prominent, which seriously affects work efficiency.
solution
In view of the difficult situation of warehouse management in Schlumberger, in order to improve the efficiency of warehouse entry, exit and inventory, and to detect warehouse tool/item location and inventory in real time, Shenzhen Yiri Technology Co., Ltd. proposed the realization of a warehouse integrated management system based on ZigBee technology. plan.
The system is used to manage the entire process of items from warehousing to delivery, mainly including items warehousing, item query and positioning, item maintenance records, item inventory, item delivery and other functions. At the same time, the system provides functions such as area management, item type management, customer management, base station layout, shelf layout, equipment low-power management, equipment failure management, etc., so that the system can achieve the purpose of warehouse automation and intelligent management.
Implementation process
First, according to the specific conditions of the warehouse area, a certain number of card reader base stations are placed in the warehouse area, so that the signal in the warehouse area is fully covered.
The card reader base station in this system is used to receive the radio frequency signal from the positioning card, and wirelessly transmit it to the next card reader base station or transmission interface; the transmission interface processes the information and uploads it to the monitoring host, and then combines map monitoring to realize query , positioning and other functions.
●The staff binds a YR-AT307 intrinsically safe positioning card for the items to be put into storage.Card reader base stationReceive the information of the positioning card and upload it to the YR-CU01 transmission interface. The transmission interface is uploaded to the host. The host will process the software to obtain the specific location information of the item. When positioning, the host map can display the regional location of the item, and then combined with the positioning card. The sound and light prompts, the staff can find the item accurately and conveniently.
●After the item is bound to the location card, the information is uploaded to the system through the card reader base station, and the item information is displayed in the item information column in the item management. etc. to inquire.
●The indicator light of the positioning card and the sound of the buzzer have four states, which can indicate four different states of the item, namely: lack of accessories, pending maintenance, maintenance, and maintenance. Press the button on the positioning card for about 1 second to view the current status of the item, and press and hold the button on the positioning card for more than 3 seconds to switch between four states. Every time the state is changed, the system will record the state change, thus forming a state record, which is convenient for tracking and querying.
The system has the function of automatically counting various types of items. When the positioning card enters the warehouse, enter the item number, positioning card number, item type, and item description. The information is uploaded to the transmission interface through the card reader base station, and the transmission interface is uploaded to the host. After the host is analyzed and counted, Calculate the quantity of each type and complete the inventory of inventory items.
Item outbound statistics can record the item number, item type, inbound time, outbound time, destination and other information, and the system will automatically generate the item number, item type, inbound time, and outbound time when it is out of the warehouse, and the destination needs customers. Make a choice, and the choice of where to go is the information entered by the customer in advance.
(software interface)
Scheme effect
After Schlumberger adopted the wireless radio frequency management system of Shenzhen Yiri Technology Co., Ltd. to realize the automatic management of the warehouse, the efficiency of warehouse management was greatly improved. When searching for items, the staff does not need to look at the record book, but just directly enters the item code and clicks the location to complete the search of the item easily and quickly, effectively shortening the time to find the item.
The company has made the following statistics: the average time to find an item has been shortened from 65 minutes to 5 minutes. In 2012, the system was used to complete 4,586 tool searches, saving 4,586 hours of time annually. Considering the salary status of managers, technicians and helpers, the annual financial expenditure was saved approximately 302,867 US dollars. In addition, various departments of the enterprise can know the inventory status, status, and distribution of items in real time on a unified software platform; managers can easily know the tool management of the entire base, which greatly improves the operational efficiency of the entire base. .
[ad_2]